Uygulamalı Kılavuz
Giriş
CNC kesim makineleri genellikle iki boyutlu tasarımları kesmek için tasarlanır ve metal, ahşap, plastik gibi malzemeleri kesmek için kullanılan X ve Y olmak üzere iki eksen içerir. Bu makinelerde ayrıca kesici memenin iş parçası yüzeyine olan mesafesini ayarlayan bir Z ekseni de bulunabilir. Ancak bu makinelerde Z ekseni kontrolü genellikle otomatik değildir ya da G-Kodu ile gerçekleştirilmez; bunun yerine operatör memenin mesafesini manuel olarak ayarlamalıdır. Z ekseni motorları AC, DC, step motor veya servo motor olabilir ve malzeme türü ile kalınlığına bağlı olarak kesici meme hava gazı, plazma, su jeti, lazer vb. ile donatılabilir.
CNC Kesim Makineleri için Radonix Arayüzleri
CNC kontrol cihazları üreticisi olan Radonix, bu tür makineleri kapsamlı şekilde analiz etmiş ve onlara özel arayüzler tasarlamıştır. XY-Cutter ve XYZ-Cutter arayüzleri bu makineler için özel olarak tasarlanmıştır:
- XY-Cutter Arayüzü: Z ekseni olmayan ya da Z ekseni için AC ve DC motor kullanan makineler için.
- XYZ-Cutter Arayüzü: Z ekseni olan ve step motor ya da servo motor kullanan makineler için.
Bu arayüzlerde tüm girişler, çıkışlar ve fonksiyonlar C- öneki ile tanımlanır.
Radonix Arayüzlerinin Temel Özellikleri
- G-Koda dönüştürmeye gerek kalmadan tasarım dosyalarının doğrudan çalıştırılması.
- Büyük bir dosyadan belirli parçaların seçilerek, her bir parça için kesim sırasının ve yönünün tanımlanabilmesi.
- Yazılımda ölçekleme, döndürme ve aynalama gibi tasarım düzenleme özellikleri.
- Özellikle ağır saclar için iş parçası hizalama hatalarının yazılım tabanlı olarak düzeltilmesi.
- Kesim öncesi, sırasında ve sonrasında ayrı ayrı duraklatma seçenekleri.
- Kesim çıkışı aktif olmadan tasarımların tersine çalıştırılması ve demo yapılabilmesi.
- Boru gibi silindirik yüzeylerde 2D tasarımların çalıştırılması.
Bu özellikler, Radonix arayüzlerinin kesim sürecinde daha hassas kontrol ve daha yüksek verimlilik sunmasını sağlar.
Bu arayüz XY Cutter olarak adlandırılır
Radonix, XY Cutter makineleri için Z Ekseni stratejisi ve işlevselliğine göre kategorize edilmiş üç farklı arayüz sunar. Bu ayrım, çeşitli makine türleri ve operasyonel ihtiyaçlarla uyumluluğu sağlar. Aşağıda bu arayüzlerin detaylı açıklamaları yer almaktadır:
1. XY Cutter Arayüzü (DC Motor Kontrollü Z Ekseni)
XY Cutter arayüzü, DC motorlar kullanarak Z Ekseni kontrolü sağlayan makineler için tasarlanmıştır. Bu yapılandırmada:
- Z Ekseni çıkış bağlantıları ile kontrol edilir:
- Yukarı hareket için C-Zfree,1
- Aşağı hareket için C-Zfree,-1
Bu basit kontrol yöntemi, pulse ve yön sinyalleri içermediği için temel XY kesim makineleri için uygundur. Operatörler Z Ekseni’ni yukarı veya aşağı hareket ettirmek için çıkışları manuel olarak etkinleştirebilir.
2. XYZ Cutter Arayüzü (Manuel Step/Servo Kontrollü Z Ekseni)
XYZ Cutter arayüzü, manuel modda çalışan step motor veya servo motor kullanan makineler için tasarlanmıştır. Bu yapılandırmada:
- Z Ekseni, pulse ve yön sinyalleri aracılığıyla doğrudan eksensel kontrol pinlerine bağlanır.
- Operatörler, takım yolu yürütme sırasında Z Ekseni pozisyonunu manuel olarak ayarlayarak kesici takımın (örneğin plazma torcu) iş parçası yüzeyine olan yüksekliğini koruyabilir.
Bu arayüz, işlem sırasında hassasiyet sağlamak için manuel müdahalenin gerektiği uygulamalar için uygundur.
3. XYZ Cutter + THC Arayüzü (Otomatik Step/Servo Kontrollü Z Ekseni)
XYZ Cutter + THC arayüzü, Z Ekseni’nin otomatik modda, THC (Torch Height Control) modülü tarafından kontrol edildiği makineler için tasarlanmıştır. Bu yapılandırma, plazma ünitesinin ark voltajı geri bildirimiyle çalışır:
- Geri Bildirim Voltaj Kontrolü:
- Plazma ark uzunluğu arttıkça, plazma ünitesinden gelen geri bildirim voltajı artar.
- Ark uzunluğu azaldıkça, voltaj düşer.
- Otomatik Ayarlama:
- Z Ekseni, kesim mesafesini optimumda tutmak için geri bildirim voltajına bağlı olarak yüksekliğini dinamik olarak ayarlar.
THC modülü, gerçek zamanlı ayarlamalar yaparak sürekli ve hassas kesim performansı sağlar. Bu arayüz, otomatik yükseklik kontrolünün kritik olduğu yüksek hassasiyetli plazma kesim makineleri için idealdir.
Özet
Radonix’in XY Cutter makineleri için sunduğu arayüzler, çeşitli operasyonel ihtiyaçlara göre uyarlanmıştır:
- XY Cutter Arayüzü: DC motor kontrollü Z Ekseni olan temel makineler için, yukarı/aşağı hareketler için C-Zfree,1 ve C-Zfree,-1 çıkışlarını kullanır.
- XYZ Cutter Arayüzü: Pulse ve yön sinyalleri ile manuel kontrol edilen step/servo motorlu makineler için.
- XYZ Cutter + THC Arayüzü: Plazma ark geri bildirimi ile dinamik olarak yönetilen step/servo motorlu makineler için, Torch Height Control (THC) modülü tarafından kontrol edilir.
Bu arayüzler, Radonix kontrol cihazlarının geniş bir kesim uygulama yelpazesinde esneklik, hassasiyet ve uyum sunmasını sağlar.
Başlarken
Çalışma Alanı Açıklamaları
1- Fotoğrafla adlandırılıp belirtilmiş arayüzün farklı bölümlerini inceleyin. Bu, Butonlar, ekran, çubuklar, ses seviyesi, değerler gibi tüm erişilebilir arayüz öğelerine aşina olmanız gerektiği anlamına gelir.
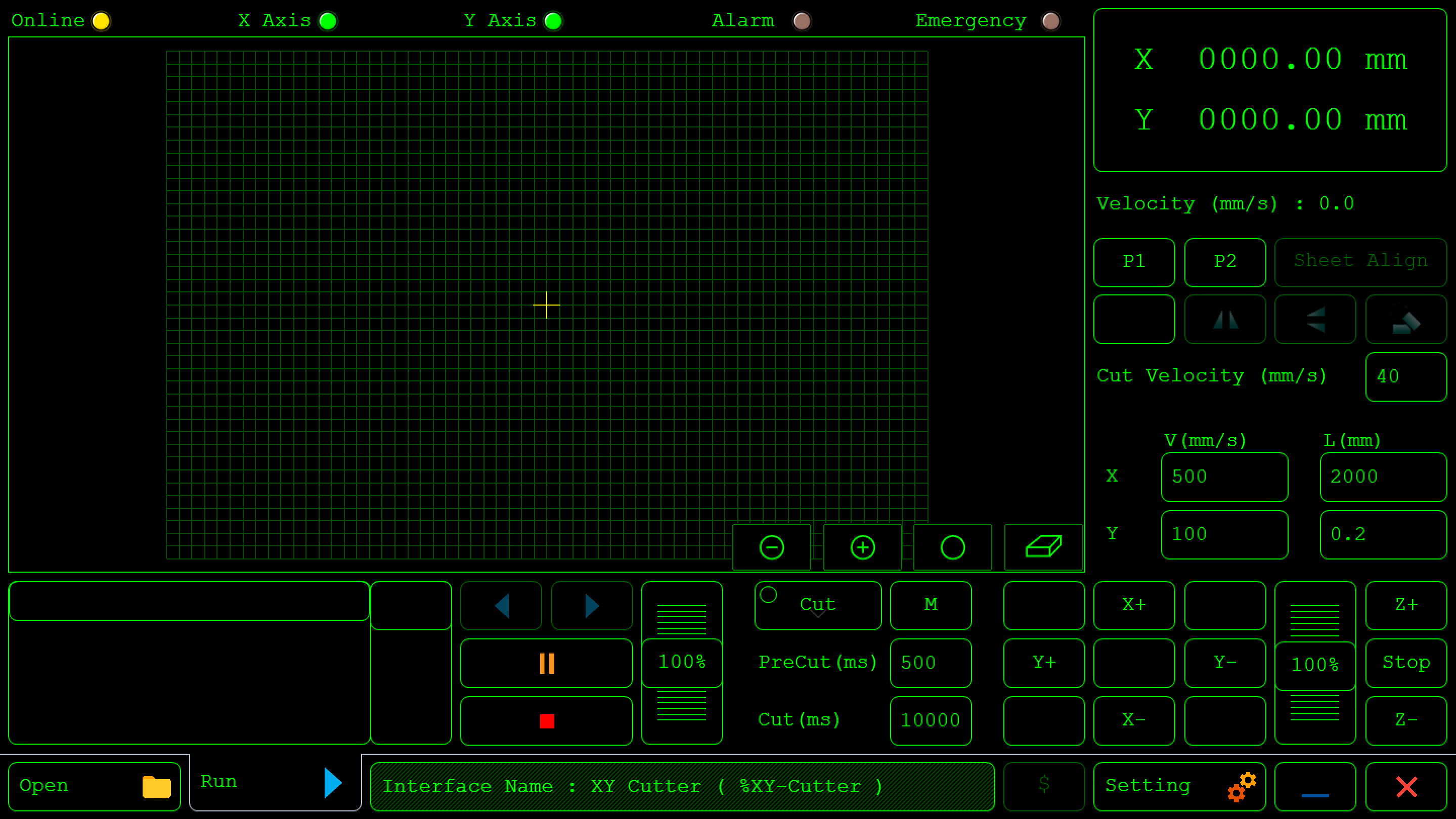
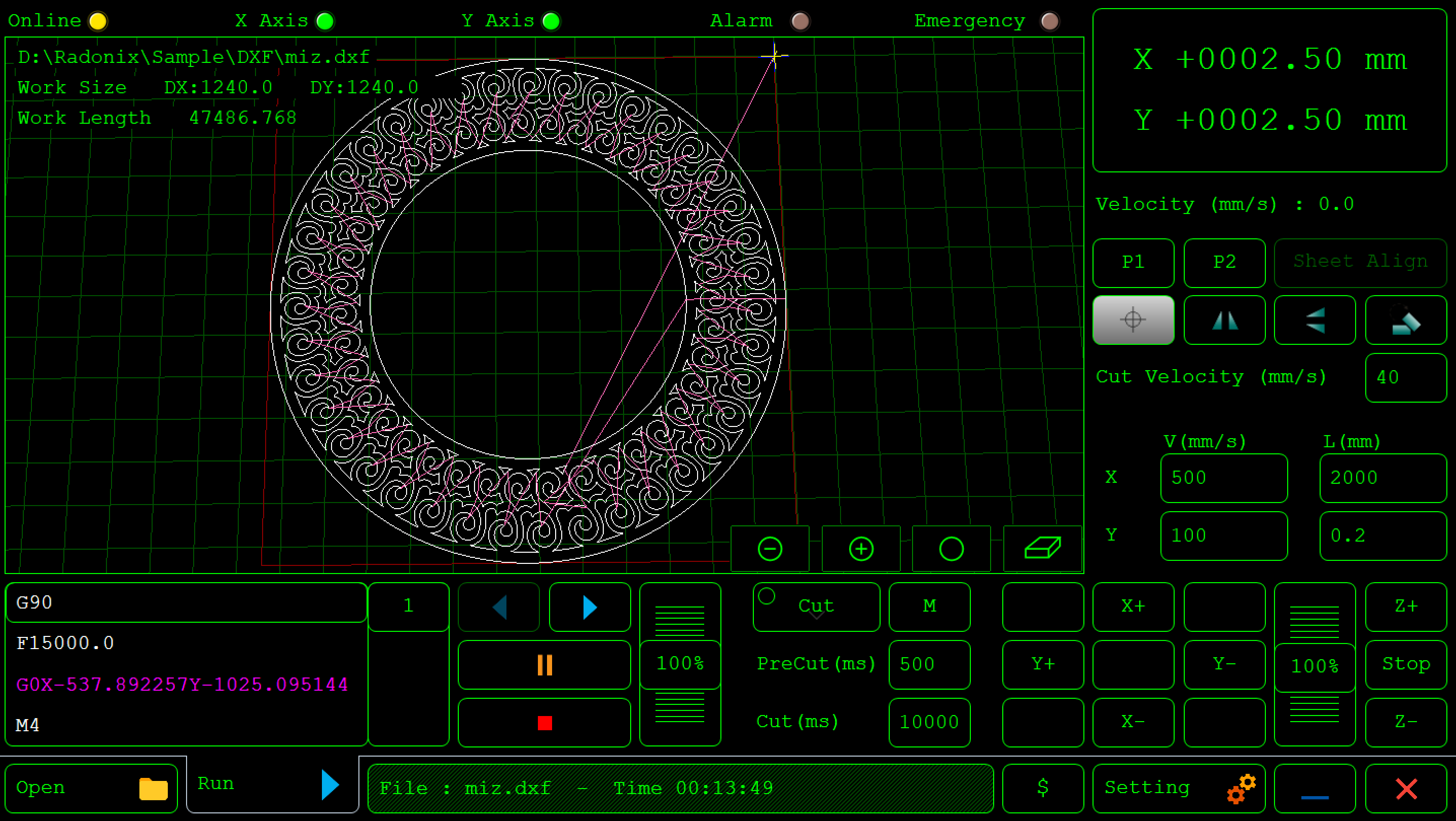
Üst Durum Çubuğu

- Online (Sarı Işık): Makinenin bağlantı durumunu gösterir. Sarı ışık bekleme modunu veya tam çevrim içi olmadığını gösterebilir.
- X Ekseni, Y Ekseni, (Yeşil Işıklar): Bu ışıklar her eksenin çalışma durumunu gösterir. Yeşil genellikle eksenin aktif veya hazır olduğunu belirtir.
- Alarm, Acil Durum (Kahverengi Işıklar): Kritik güvenlik durumlarının göstergeleri. Aktifleştirildiğinde kırmızı gibi bir renge geçebilirler.
Pozisyon ve Hız Göstergeleri (Sağ Panel)
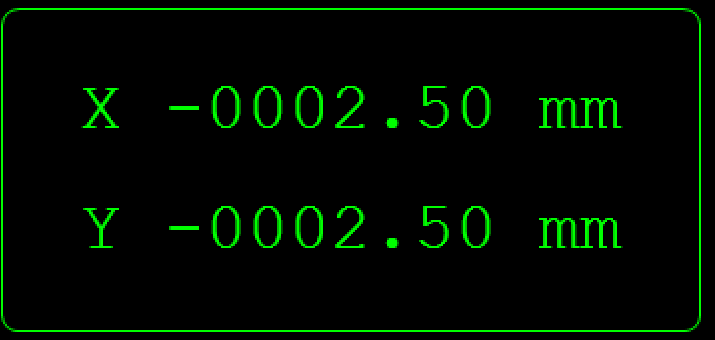
- Pozisyon :
Bu pozisyon, referans noktasının nerede seçildiğine bağlı olarak gösterilir.
- Hız (Göreli Pozisyonun Altında): Mevcut çalışma hızını mm/sn cinsinden gösterir, gerçek zamanlı kesim veya hareket hızlarını izlemek için kullanışlıdır.

Radonix Arayüzlerinde Gerçek Zamanlı Referans Ayarı
Radonix arayüzleri, operatörlerin işlem sırasında herhangi bir anda referans noktasını yeniden tanımlamasına olanak tanıyan dinamik referans ayarlama özelliği sunar. Bu özellik, iş akışlarında esneklik ve hassasiyet sağlar, böylece çeşitli uygulamalara uygun hale gelir.
bu, operatörün iş parçasının tezgah üzerindeki başlangıç noktasını değiştirebileceği anlamına gelir.
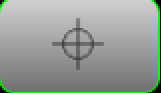
- Kesme Hızı : Bu parametre kesme hızını tanımlar.

- Manuel Jog Kontrolleri :
- Oklar (X+, X-, Y+, Y-): Bu butonlar, makineyi X ve Y eksenleri boyunca manuel olarak hareket ettirerek, takım başlığının kademeli hareketiyle hassas konumlandırma ayarlamaları yapılmasına olanak tanır.
Jog modunu, şekil 01-05'e göre bu butona basarak değiştirebilirsiniz ve şekil 01-06’ya dönüşecektir; bu da sürekli hareketten kademeli harekete geçiş anlamına gelir. Bu, şekil 01-07’de kırmızı alanla gösterildiği gibi bu bölüme bir değer tanımlayabileceğiniz ve koordinat ekseni jog butonuna bastıktan sonra eksenin girdiğiniz değer kadar hareket edeceği anlamına gelir.
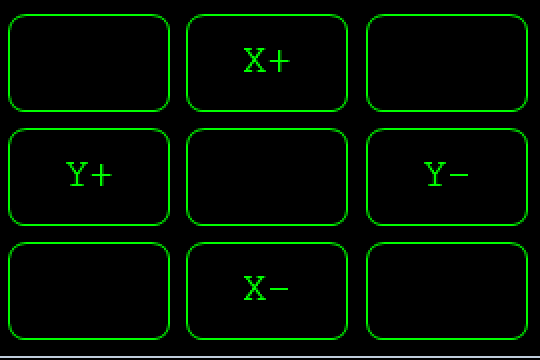
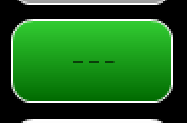
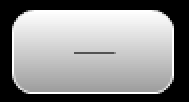
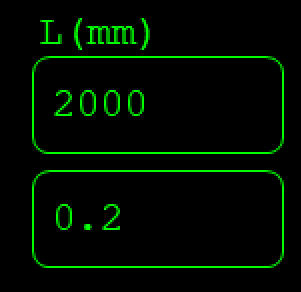
İlerleme Hızı ve Takım Parametreleri (Sağ Alt Panel)
- V (mm/sn) ve Step**(mm)**: Her eksen boyunca ilerleme hızlarını ve hareket sınırlarını ayarlamak için giriş alanları. "V", hızı (veya sürati) mm/sn cinsinden kontrol eder, "L" ise manuel jog için adım büyüklüğünü tanımlayabilir.
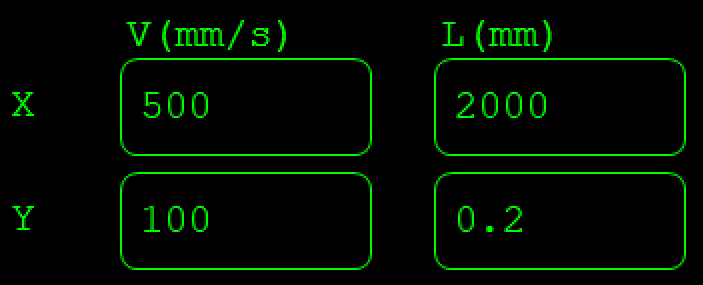
- Kaydırma (Sağ Alt Köşedeki Dikey Sürgü): Şekil 01-08’e göre kırmızı alanla işaretlenmiştir veya ilerleme hızını ya da hızı yüzde olarak gerçek zamanlı olarak ayarlamaya olanak tanır. Bu kontrol, program değerlerini doğrudan değiştirmeden hızı hızlıca değiştirebilir.
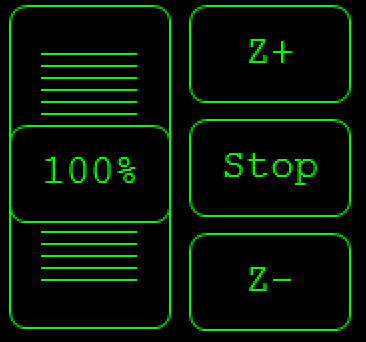
Ana Program Kontrolleri
- Ayarlar (Dişli Simgesi): CNC makinesi için ayrıntılı ayarların yapılandırılabileceği yapılandırma menüsünü açar.

- Çıkış simgesi programı kapatmanıza olanak tanır.
- Eksi simgesi programı küçültmenizi sağlar.
- $ simgesi iş parçasından bir rapor oluşturur ve operatör fiyat tahmini yapabilir.
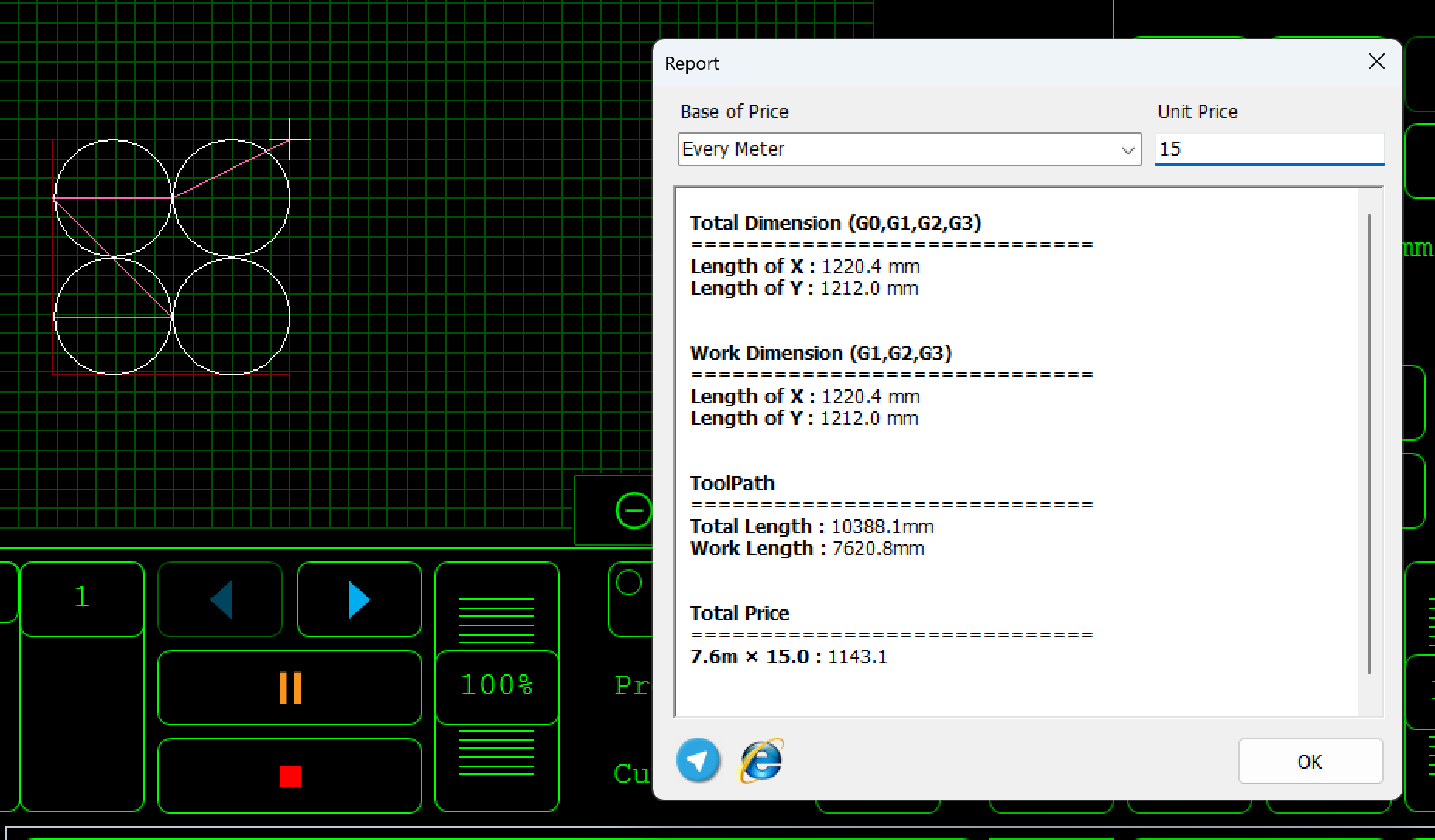
Arayüz Özellikleri

Arayüzün bu bölümü, sistemin mevcut durumunu ve özelliklerini gösterir. Ayrıca her saniye alarm ve süreçleri gösterecek şekilde güncellenir. Ayrıntılı bir rapor için bu bölüme çift tıklayın.
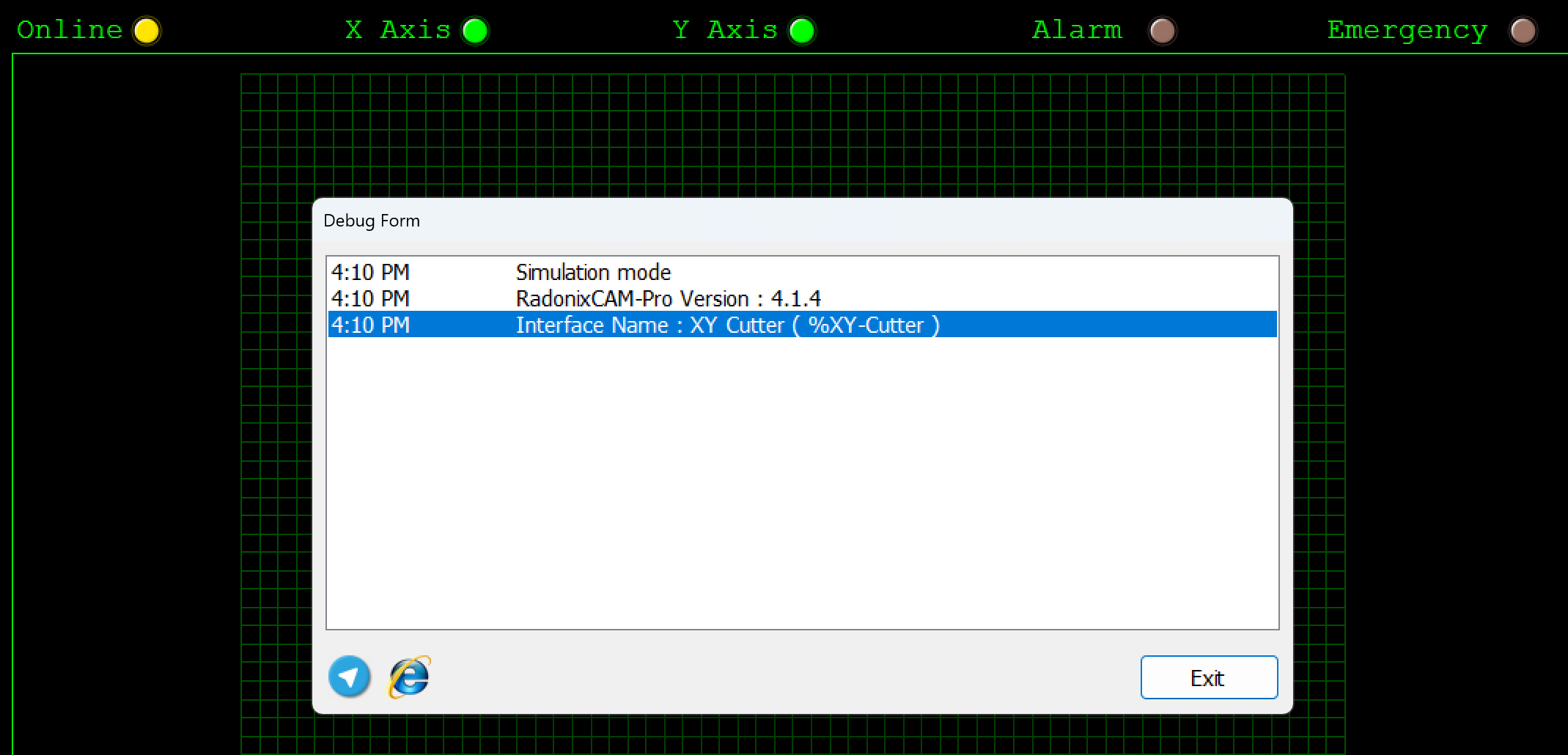
Ana Program Kontrolleri (Alt Merkez)
- Dosya Aç (Klasör Simgesi): Bir CAM (Bilgisayar Destekli Üretim) dosyası, genellikle bir G-code veya DXF programı yüklemek için dosya penceresini açar.
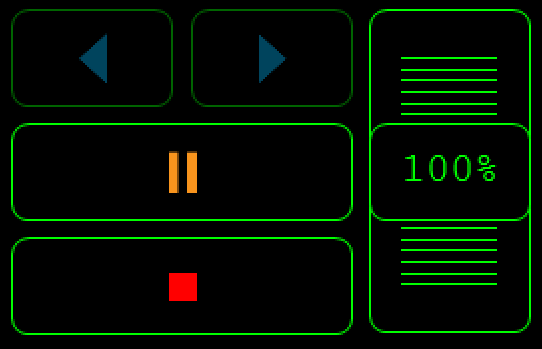
Bu bölüm, G-Kodu yürütmesini kontrol etmeye ayrılmıştır:
- RUN: Bu buton G-Kodu sürecini başlatır.
- Geri: Backward butonu, operatörlere G-Kodu takım yolu yürütme sürecinde geri adım atma imkanı sağlar. Bu özellik, sorun giderme, tekrar kontrol etme veya G-Kodunun belirli bölümlerini yeniden çalıştırma için gereklidir.
- Pause: Bu buton takım yolunu durdurur.
- Reset: Bu buton takım yolunu sıfırlar.
Girişler
Bu bölümde, Girişlerin yapılandırmasını inceleyeceğiz.
Temel olarak, Inports dalı açıldığında bu ayarlar görünecektir.
Girişleri Ayarlama: Genel Bakış
CNC sistemimizde girişleri yapılandırmak, sorunsuz çalışma, hassas kontrol ve güvenlik sağlamak için önemli bir adımdır. Girişler, yapılandırma ve amacına göre iki ana kategoriye ayrılabilir: Donanım Tabanlı Girişler ve Yazılım Tabanlı Girişler. Bu esneklik, sistemin çeşitli uygulamalara ve makine gereksinimlerine uyum sağlamasına olanak tanır.
1. Donanım Tabanlı Girişler
Donanım girişleri, kontrolöre bağlı fiziksel cihazları içerir ve makinenin çevresiyle doğrudan etkileşim sağlar. Bu girişler güvenlik, makine kontrolü ve gerçek zamanlı geri bildirim için kritiktir.
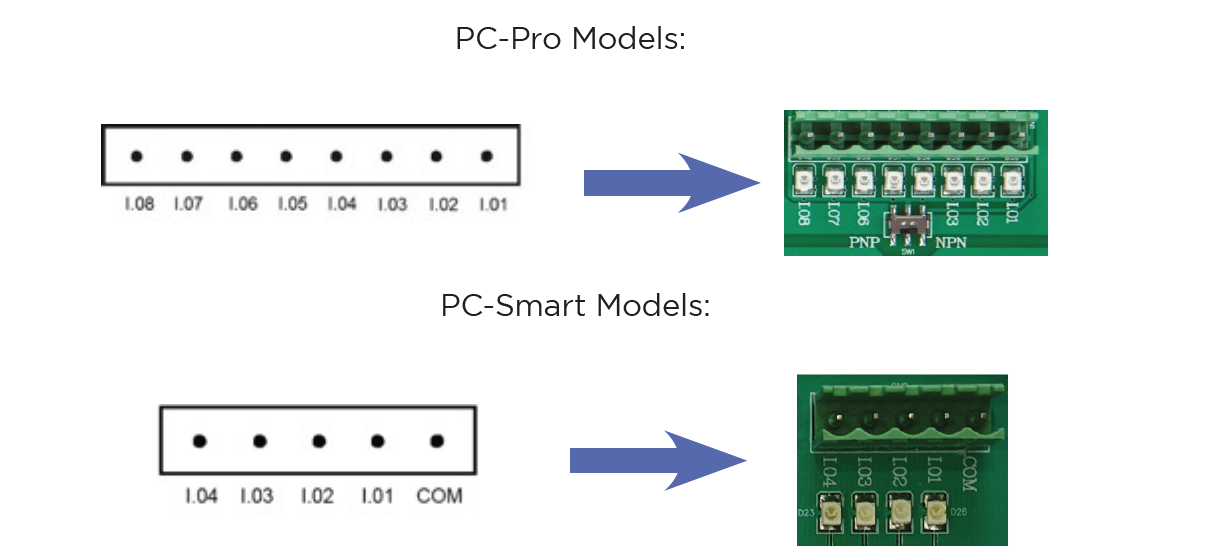
Radonix kontrol cihazlarının dijital girişleri I.[n] şeklinde adlandırılır, burada n sıfırdan büyük bir sayıdır ve giriş numarasını temsil eder. Bu girişler optik kuplörlerle izole edilmiştir ve düşük empedans nedeniyle düşük gürültü toleransına sahiptir.
Radonix kontrolörlerindeki dijital girişler, cihaz veya sensör çıkışına bağlı olarak NPN ve PNP modları arasında geçiş yapabilme yeteneğine sahiptir. PNP çıkışlı cihazlar için mod anahtarı PNP konumuna, NPN çıkışlı cihazlar için NPN konumuna getirilmelidir.
Endüstriyel otomasyonun çeşitli dallarında, PNP ve NPN için eşdeğer terimler vardır. Bu terimlerden bazı örnekler şunlardır:
NPN = Sink = Low Active
PNP = Source = High Active
Radonix Sistemlerinde PNP ve NPN Modları Arasında Geçiş
Radonix kontrol cihazlarında PNP (pozitif mantık) ve NPN (negatif mantık) modları arasında geçiş yapma yeteneği, kullanılan kart modeline bağlıdır. Bu esneklik, sistemin farklı kablolama ve sensör yapılandırmalarıyla uyumlu olmasını sağlar.
- PC Pro LAN:
- Kart üzerinde küçük bir DIP anahtar bulunur.
- Bu anahtar, kullanıcıların PNP ve NPN modları arasında geçiş yapmasına olanak tanır.
- Nasıl Kullanılır:
-
Kart üzerindeki DIP anahtarını bulun.
-
Anahtarı istenen moda (PNP veya NPN) çevirin.
-
Değişiklik yapmadan önce kartın kapalı olduğundan emin olun.
-
- PC Smart:
-
DIP anahtarı yerine, PC Smart modeli her 4 giriş pini grubu için bir Come Pin kullanır.
-
Bu pin, ilgili girişler için giriş mantığını (PNP veya NPN) tanımlamanıza olanak tanır.
-
Nasıl Kullanılır:
-
Come Pin’i uygun voltaja bağlayın (PNP için pozitif, NPN için toprak).
1. PNP Modu (Kaynak Modu):
- COM pini 0V’a bağlanırsa, giriş pinleri bir 24V sinyalle tetiklenir (etkinleşir).
- Bu yapılandırmada, sensörün çıkış kablosu girişi etkinleştirmek için 24V sağlamalıdır.
2. NPN Modu (Sink Modu):
- COM pini 24V’a bağlanırsa, giriş pinleri bir 0V sinyalle tetiklenir (etkinleşir).
- Bu yapılandırmada, sensörün çıkış kablosu girişi etkinleştirmek için 0V’a çekmelidir.
- COM pini 0V’a bağlanırsa, giriş pinleri bir 24V sinyalle tetiklenir (etkinleşir).
-
Her 4 giriş pini grubu kendi Come Pin’ine sahiptir ve bu da aynı kart üzerinde karışık yapılandırmalara olanak tanır.
-
-
Donanım Girişlerine Örnekler:
- Limit Switchler: Eksen hareketi için fiziksel sınırları tanımlar.
- Home Sensörleri: Makinenin referans (Home) konumunu belirler, çoğu yakınlık sensörüdür.
- Acil Durdurma Butonları: Acil durumlarda işlemlerin anında durmasını sağlar.
- Diğer Yakınlık Sensörleri: Makine çalışma alanında nesneleri veya takımları algılar.
- Basmalı Butonlar ve Seçici Anahtarlar: Belirli makine işlevlerini veya modlarını tetikler.
- Tarayıcılar: Özellikle cam veya altın CNC işlemleri gibi özel işlemlerde belirli özellikleri ölçer veya algılar.
Yapılandırma Süreci:
- Bağlantı: Donanım bileşenini (ör. bir anahtar veya sensör) kontrol cihazındaki ilgili giriş pinine fiziksel olarak bağlayın.
- Giriş Tanımı: Girişin görevini tanımlamak için kontrolör yazılımını kullanın (örneğin
HomePin
,LimitPin
veya belirli işlevler için özel bir giriş). - Kutupluluk Ayarları:
- Giriş türünü bağlı donanımın varsayılan durumuna göre Normalde Açık (NO) veya Normalde Kapalı (NC) olarak ayarlayın.
- Örneğin:
- NC acil durdurma butonu, basılana kadar aktif (kapalı) kalır.
- NO yakınlık sensörü yalnızca bir nesne algılandığında etkinleşir (kapanır).
2. Yazılım Tabanlı Girişler
Yazılım Tabanlı Girişler, rastgele bağlantıları yapılandırmak ve bunları ilgili fiziksel donanımla entegre etmek için basit mantıksal işlevsellik sağlar. Mikroprogramlama gerekmeden hızlı ve basit kurulum sağlarlar. Kullanıcılar, listeden seçenekler seçerek ve ayarları yapılandırarak verimliliği en üst düzeye çıkarabilir.
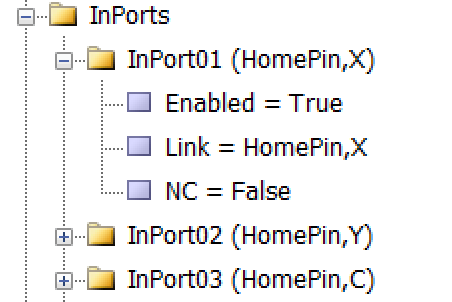
Şekilde gösterildiği gibi, her giriş aşağıda ayrıntılı olarak açıklanan üç alt dala ayrılmıştır:
- Enable: Bu alt dal iki değerden birine ayarlanabilir: True veya False.
- Link: Gerçekleştirilmesi veya kontrol edilmesi gereken görevi tanımlar. Bu, sensörler, butonlar ve anahtarlar gibi giriş görevi görebilecek herhangi bir cihazı kapsar.
- NC: Belirli girişin Normalde Açık (NO) mu yoksa Normalde Kapalı (NC) mı olduğunu belirler.
Yazılım Girişlerine Örnekler:
- Sanal Limit Switchler:
- Makine tezgah boyutuna göre eksen hareket sınırlarını yazılım parametreleriyle tanımlayın.
- Mantıksal Tetikleyiciler: Belirli işlemler için koşullu tetikleyiciler tanımlayın (örneğin, eksen limit switch'e ulaştığında).
- Simüle Edilmiş Girişler: Fiziksel bileşenlerin mevcut olmadığı test veya senaryolarda kullanılır.
Yapılandırma Süreci:
-
Yapılandırma Arayüzüne Erişim:
- Girişleri yönetmek için kontrol yazılımının ayarlarını açın.
-
Parametreleri Tanımla:
Limit Switch ayarlamak için örnek:
-
Ayar —→ Sistem —→ Girişler —→ Enabled= True
Linked = LimitPin,X
NC= True
-
Kilitlemeler veya simülasyonlar için ek mantıksal koşulları yapılandırın.
- Ayarları Doğrulama:
- CAM Pro TEST giriş yapılandırmalarını test ederek yazılımın düzgün çalıştığından ve güvenli olduğundan emin olun.
Çıkışlar
Bu bölümde, çıkışların yapılandırmasını inceleyeceğiz.
Çıkışları Ayarlama: Genel Bakış
Radonix sistemlerinde, Çıkışlar (Outports) röleler, aktüatörler, alarmlar ve diğer cihazları kontrol eden çıkış sinyallerini yöneten kritik bileşenlerdir. Çıkışlar, yapılandırma ve amaçlarına göre iki ana tipe ayrılabilir: Donanım Tabanlı Çıkışlar ve Yazılım Tabanlı Çıkışlar. Bu esneklik, sistemin çeşitli uygulamalara ve makine gereksinimlerine uyum sağlamasına olanak tanır.
1. Donanım Tabanlı Çıkışlar
Donanım çıkışları, kontrolörden harici cihazlara gönderilen fiziksel sinyalleri içerir ve makinenin çevresini doğrudan kontrol etmeyi sağlar. Bu çıkışlar, operasyonel güvenlik, makine etkinleştirme ve gerçek zamanlı komut yürütme açısından kritik olup CNC sisteminde verimli iş akışı ve koordinasyon sağlar.
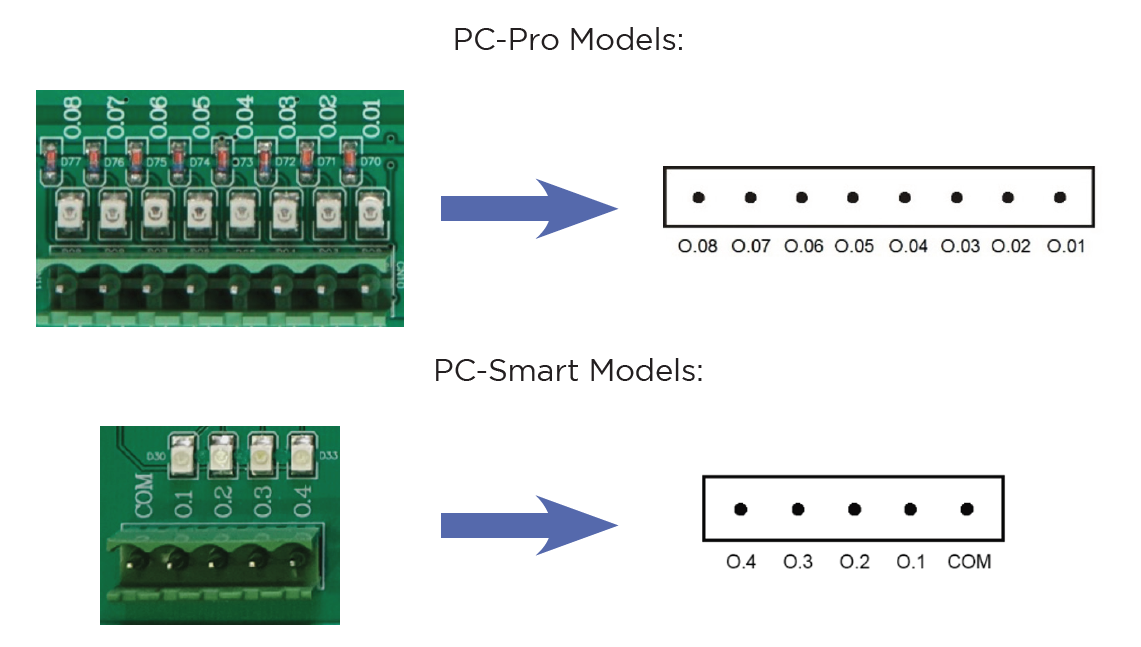
Radonix kontrolörlerinin dijital çıkışları O.[n] şeklinde adlandırılır, burada n sıfırdan büyük bir sayısal tanımlayıcıdır ve çıkış numarasını temsil eder.
Radonix kontrol cihazları, Çıkışlar için dayanıklılık, güvenlik ve güvenilirlik sağlamak üzere sağlam koruma mekanizmaları içerir. Bu mekanizmalar, özellikle PC-Pro ve PC-Smart kart modelleri arasında değişir ve her birinin kendine özgü koruma özellikleri ve hata yönetim süreçleri vardır.
PC-Pro LAN Modellerinde Çıkış Davranışı
-
PC-Pro LAN modeli çıkışları NPN modunda sabitlenmiştir.
-
Nasıl Çalışır:
- Bir çıkış AÇIK olduğunda, sinyali toprağa çekerek 0 volt sağlar.
- Bir çıkış KAPALI olduğunda, yüksek empedans durumundadır ve devreyi fiilen keser.
-
Kablolama Dikkatleri:
- Bağlı cihazlar, pozitif kaynaktan voltaj alan ve çıkış devreyi toprağa çektiğinde etkinleşen NPN mantığıyla uyumlu olmalıdır.
PC-Smart Modellerinde Çıkış Davranışı
-
PC-Smart modeli, çıkışların PNP modu veya NPN modu olarak çalışabileceği esnek bir yapılandırma sunar, bu yapı COM Pin bağlantısına bağlıdır.
-
Nasıl Çalışır:
- Çıkışların sağladığı voltaj, COM Pin'e neyin bağlı olduğuna bağlıdır:
- COM Pin 24V'a bağlıysa: Çıkışlar etkinleştirildiğinde 24 volt sağlar.
- COM Pin toprağa bağlıysa: Çıkışlar etkinleştirildiğinde 0 volt sağlar (NPN modu).
- Çıkışların sağladığı voltaj, COM Pin'e neyin bağlı olduğuna bağlıdır:
-
Esneklik:
- Bu tasarım, PC-Smart modellerinin farklı kablolama gereksinimlerine ve cihaz mantığı tercihine uyum sağlamasına olanak tanır.
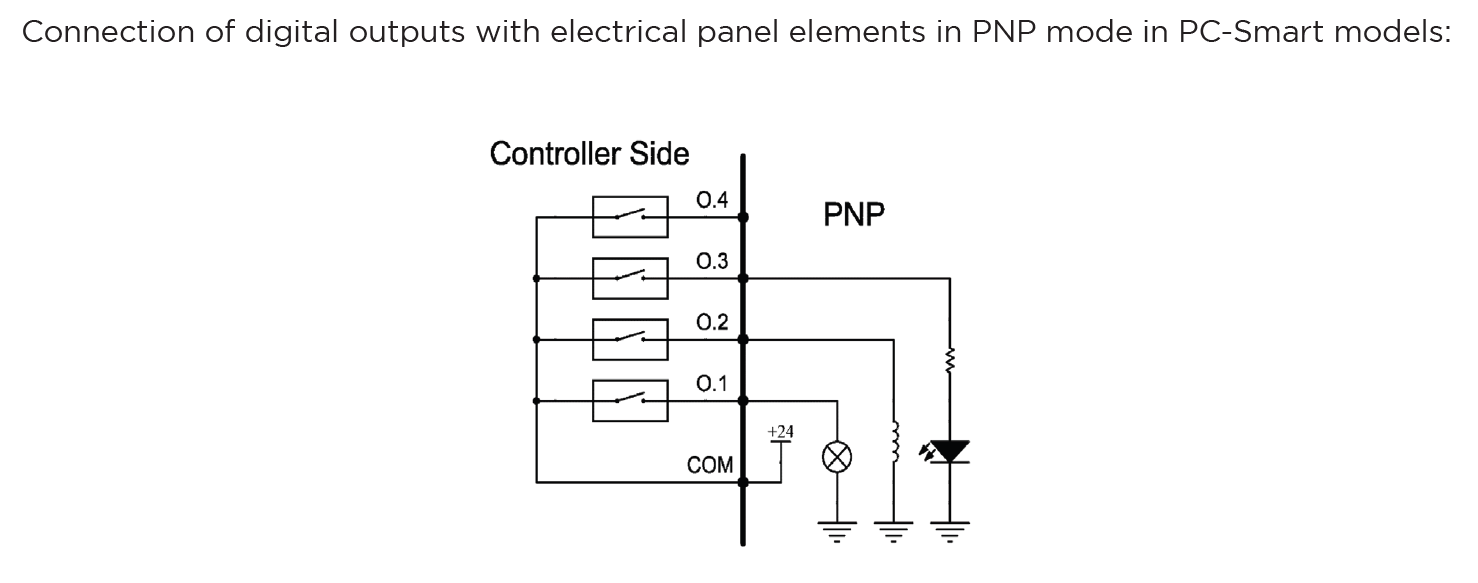
Çıkışlar için Yapılandırma Süreci:
- Bağlantı:
- Donanım bileşenini (ör. röle, elektrik valfi, fren, alarm) kontrol cihazındaki ilgili çıkış pinine fiziksel olarak bağlayın.
- Gerekli mantık (PNP veya NPN) ve voltaj uyumluluğuna göre uygun kablolamayı sağlayın.
- Çıkış Tanımı:
- Kontrol yazılımını kullanarak çıkışın görevini tanımlayın (ör.
C-CutPin
,Brake
veya belirli işlevler için özel bir çıkış). - Çıkışı, sistem ayarlarında hedeflenen cihaz veya işleve atayın.
- Kontrol yazılımını kullanarak çıkışın görevini tanımlayın (ör.
- Mantık Ayarları:
- Bağlı cihazın gereksinimlerine göre çıkış mantığını ayarlayın:
- Aktif Yüksek (PNP): Çıkış etkinleştirildiğinde voltaj (ör. 24V) gönderir.
- Aktif Düşük (NPN): Çıkış etkinleştirildiğinde sinyali toprağa (0V) çeker.
- Bağlı cihazın gereksinimlerine göre çıkış mantığını ayarlayın:
- Test ve Doğrulama:
- Yapılandırmadan sonra, çıkışın CAM Pro Test uygulamasında amaçlandığı gibi çalıştığından emin olun.
- Multimetre veya diğer tanı araçlarıyla çıkış voltajını ve davranışını doğrulayın.
2. Yazılım Tabanlı Çıkışlar
Yazılım Tabanlı Çıkışlar, basit mantıksal işlevsellik sağlayarak bunların ilgili fiziksel donanımla yapılandırılmasını ve entegre edilmesini sağlar. Bu özellikler, kontrol yeteneklerini artırmak için kritiktir. Mikroprogramlama gerektirmeden hızlı ve basit kurulum sağlarlar. Kullanıcılar, listeden seçenekler seçerek ve ayarları yapılandırarak verimliliği en üst düzeye çıkarabilir.
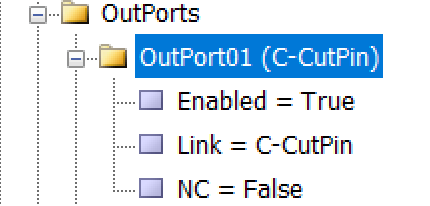
Şekilde gösterildiği gibi, her çıkış aşağıda ayrıntılı olarak açıklanan üç alt dala ayrılmıştır:
- Enable: Bu alt dal iki değerden birine ayarlanabilir: True veya False.
- Link: Gerçekleştirilmesi veya kontrol edilmesi gereken görevi tanımlar. Bu, aktüatörler, ışıklar ve alarmlar gibi çıkış görevi görebilecek herhangi bir cihazı kapsar.
- NC: Belirli çıkışın Normalde Açık (NO) mu yoksa Normalde Kapalı (NC) mı olduğunu belirler.
Yazılım Çıkışlarına Örnekler:
- Sanal Röleler:
- İşletme ihtiyaçlarına göre cihazlar için etkinleştirme sınırlarını yazılım parametreleriyle tanımlayın.
- Mantıksal Tetikleyiciler: Belirli çıkışları etkinleştirmek için koşullu tetikleyiciler tanımlayın (ör. belirli işlev için alarm veya röle).
- Simüle Edilmiş Çıkışlar: Fiziksel bileşenlerin mevcut olmadığı test veya senaryolarda bunları kullanın.
Yapılandırma Süreci:
- Yapılandırma Arayüzüne Erişim:
- Çıkışları yönetmek için kontrol yazılımının ayarlarına gidin.
- Parametreleri Tanımla:
-
Örneğin bir çıkışı VFD’yi ileri yönlendirmek için yapılandırmak adına parametreleri girin.
-
Ayar —→ Sistem —→ Çıkışlar —→ Enabled= True
Linked = C-CutPin
NC= True
-
- Ayarları Doğrulama:
- Yapılandırılmış yazılım çıkışlarının doğru ve güvenli çalıştığından emin olmak için test edin, gerçek uygulamalarda etkinliklerini doğrulayın.
Girişleri Ayarlama: Basit ve Sezgisel Yapılandırma
Radonix sisteminde, giriş veya çıkış yapılandırması kullanıcı dostu olacak şekilde tasarlanmıştır ve hiçbir mikroprogramlama veya ileri düzey teknik bilgi gerektirmez. Tek yapmanız gereken, kontrol arayüzündeki Girişler bölümüne gitmek, ayarlar panelini açmak ve yapılandırmak istediğiniz öğeyi seçmektir. Aynı süreç, Çıkışlar veya diğer tüm işlevsel alanlar için de geçerlidir.
Adım Adım Yapılandırma Süreci
- İstenilen Bölüme Erişim:
- Yapılandırmak istediğiniz bölüme gidin, örneğin Girişler veya Çıkışlar, kurmak istediğiniz işlevselliğe bağlı olarak.
- Ayar Panelini Açın:
- Seçilen bölümde, belirli giriş dalını veya alt bölümünü bulun.
- Ayar panelini göstermek için tıklayın veya genişletin.
- Gerekli Öğeyi Seçin:
- Yapılandırmak istediğiniz giriş türünü veya işlevi seçin (ör. limit switch, home sensörü, acil durdurma veya özel girişler).
- Girişin özel rolünü tanımlayın, örneğin
C-ZFreePin,1
- Parametreleri Kolayca Ayarlayın:
- Kutup (Normalde Açık veya Normalde Kapalı), gecikmeler veya mantıksal davranış gibi gerekli parametreleri doğrudan arayüzden ayarlayın.
- Kaydedin ve Test Edin:
- Ayarlarınızı kaydedin ve kontrol arayüzü aracılığıyla doğrulayarak her şeyin amaçlandığı gibi çalıştığından emin olun.
- Son olarak, tüm ayarları kalıcı hale getirmek için programı kapatmanız gerekir
Radonix CNC Kontrol Cihazı için Kurulum ve Yapılandırma Süreci
Radonix, bir Radonix CNC kontrol cihazının kurulumu ve yapılandırması için bu ayrıntılı adım adım kılavuzun izlenmesini önermektedir. Bu süreç, donanımın kablolamasından yazılımda parametrelerin ayarlanmasına kadar her şeyi kapsar. Bu yaklaşım, müşteriler için sorunsuz bir kurulum deneyimi sağlamayı ve tüm kritik bileşenleri ele almayı amaçlar.
Radonix CNC Kontrol Cihazı için Bileşen Kablolama
Doğru kablolama, güvenilir ve yüksek performanslı bir CNC makinesinin temelidir. Profesyonel bir kablolama yaklaşımı, Radonix kontrol cihazı, servo veya step motorlar, sensörler, VFD'ler (Değişken Frekans Sürücüleri) ve diğer çevre birimleri arasında sorunsuz iletişim sağlar. Bu kılavuz, uygun güç kaynaklarının seçilmesi, güvenliğin sağlanması ve en yüksek performansın elde edilmesi dahil olmak üzere tüm bileşenlerin kablolaması hakkında uzman tavsiyeleri sunar.
1. Ana Bileşenlere Genel Bakış
Tipik bir CNC sistemi aşağıdaki bileşenleri içerir ve tümü hassas ve güvenli kablolama gerektirir:
- Radonix CNC Kontrol Cihazı: Merkezi kontrol ünitesi.
- Servo veya Step Motorlar: Eksen hareketinden sorumludur.
- Değişken Frekans Sürücüsü (VFD): Mili kontrol eder.
- Sensörler:
- Eksen referanslaması için Home Sensörleri.
- Sınır kontrolü için Limit Switchler.
- Eksen referanslaması için Home Sensörleri.
- Sınır kontrolü için Limit Switchler.
- Acil Durdurma (E-Stop): Acil durumlarda anında kapanma sağlar.
- Güç Kaynakları: Farklı bileşenler için düzenlenmiş güç sağlar.
- Çevresel Çıkışlar: Röleler, soğutma pompaları ve alarmlar içerir.
2. Ana Güç Kaynağını Kablolama
Uygun Güç Kaynağının Seçilmesi
-
Kontrol Cihazı Güç Kaynağı:
Radonix kontrol cihazlarını beslemek için 24V anahtarlamalı güç kaynaklarının kullanılması önerilir. Güç kaynağı akımının hesaplanması: elektrik panosunda gereken güç kaynağı akımını belirlemek için, güç kaynağına bağlı her elemanın akım tüketimi hesaplanmalıdır. Örneğin, bir pano içerisinde 4 röle, 3 pnömatik solenoid valf ve bir kontrol cihazı varsa, akım tüketimi Ohm Yasası (V=I*R) kullanılarak belirlenebilir. Elektrik akımları hesaplanmalı ve güven katsayısı ile birlikte toplamı, güç kaynağı akımı olarak dikkate alınmalıdır. Örneğin, rölelerin akım tüketimi 0.1A ve solenoid valflerin 0.25A ise, toplam akım şöyle hesaplanabilir:
Toplam akım = kontrol cihazı akımı + röle akımı + solenoid valf akımı IT = 0.5 + 4 * 0.1 + 3 * 0.25 = 1.65A
3. CNC Kablolama için Parazit Önleme Önlemleri
Elektromanyetik girişim (EMI) veya elektriksel parazit, özellikle kontrol cihazları, servo sürücüler ve sensörler gibi hassas bileşenlerin kablolandığı CNC sistemlerinde yaygın bir sorundur. Parazit, sinyalleri bozabilir, makinenin düzensiz davranmasına neden olabilir ve zamanla bileşenlere zarar verebilir. Güvenilir ve hassas CNC makinesi çalışması için güçlü parazit önleyici önlemlerin uygulanması kritik önemdedir.
Elektriksel Parazit Kaynakları
- Yüksek Frekanslı Cihazlar:
- Değişken Frekans Sürücüleri (VFD'ler) - (İlgili Makinelerde)
- Anahtarlamalı güç kaynakları
- Yüksek Güçlü Bileşenler:
- Mil motorları - (İlgili Makinelerde)
- Servo ve step motorlar
- Uzun Kablolar:
- Daha uzun kablolar anten gibi davranarak EMI toplar.
- Güç Hatlarına Yakınlık:
- Yakın mesafede geçen sinyal ve güç kabloları parazite neden olabilir.
Temel Parazit Önleme Önlemleri
1. Korumalı Kablolar Kullanın
- Amaç: Korumalı kablolar, elektromanyetik girişimin hassas sinyaller üzerindeki etkisini azaltır.
- Uygulama:
- Pulse+, Pulse-, Direction+, Direction- ve sensör sinyalleri gibi sinyal hatları için bükümlü çift korumalı kablolar kullanın.
- Kalkanı yalnızca bir ucundan toprağa bağlayın, böylece toprak döngüleri önlenir.
2. Sinyal ve Güç Kablolarını Ayırın
- Amaç: Yüksek güçlü kabloların düşük güçlü sinyal kablolarında parazite neden olmasını önlemek.
- Uygulama:
- Sinyal kablolarını (örneğin sensör ve kontrol sinyalleri) güç kablolarından (örneğin motor gücü ve VFD çıkışı) ayrı şekilde yönlendirin.
- Bu kablo türleri arasında en az 10-15 cm mesafe bırakın.
- Güç ve sinyal hatları için farklı kablo kanalları veya boruları kullanın.
3. Uygun Topraklama
- Amaç: İyi tasarlanmış bir topraklama sistemi paraziti en aza indirir ve bileşenleri korur.
- Uygulama:
- Elektrik kutusunda merkezi bir topraklama noktası oluşturun, genellikle topraklama bara olarak adlandırılır.
- Tüm topraklama kablolarının (kontrolör, sürücüler, motorlar vb.) bu merkezi noktaya bağlı olduğundan emin olun.
- Toprak bağlantılarının zincirleme yapılmasından kaçının, bu durum parazite neden olabilir.
4. Ferrit Boncukları Takın
- Amaç: Ferrit boncuklar, sinyal ve güç kabloları üzerindeki yüksek frekanslı parazitleri filtreler.
- Uygulama:
- Ferrit boncukları, kontrol cihazı veya servo sürücülere yakın sinyal ve kontrol kablolarına takın.
- Özellikle gürültülü ortamlarda birden fazla boncuk kullanın.
5. Uygun VFD Kablolaması
- Amaç: VFD’ler önemli bir elektriksel parazit kaynağıdır ve özel dikkat gerektirir.
- Uygulama:
- VFD ile mil motoru arasında korumalı kablolar kullanın.
- Kablo kalkanını VFD tarafında toprağa bağlayın.
- VFD giriş ve çıkışlarına hat filtreleri veya bobinler takın.
6. Kablo Uzunluklarını Kısaltın
- Amaç: Daha uzun kablolar parazit toplamaya daha yatkındır.
- Uygulama:
- Kablo uzunluklarını esneklikten ödün vermeden mümkün olduğunca kısa tutun.
- Gereksiz boşluk veya kablo halkalarından kaçının.
7. İzole Güç Kaynakları Kullanın
- Amaç: Bir sistemdeki parazitin diğer sistemi etkilemesini önlemek.
- Uygulama:
- Sensörler, enkoderler ve kontrol cihazı gibi hassas bileşenler için ayrı, izole güç kaynakları kullanın.
- Güç kaynaklarının yeterli derecelendirmeye sahip olduğundan ve uygun şekilde topraklandığından emin olun.
8. Optik İzolasyon Kullanın
- Amaç: Kontrol cihazını harici bağlantılardaki parazitten korumak.
- Uygulama:
- Sensörler, röleler veya anahtarlar gibi harici cihazlara bağlantılar için optik izolatörler kullanın.
- Radonix kontrol cihazlarının çoğu, girişler ve çıkışlar için yerleşik optik izolasyona sahiptir.
9. Güvenli Bağlantılar
- Amaç: Gevşek bağlantılar parazit kaynağı olabilir.
- Uygulama:
- Tüm konnektörlerin sıkı ve güvenli olduğundan emin olun.
- Mümkünse kilitlemeli konnektörler kullanarak kazara bağlantı kesilmelerini önleyin.
10. Hat Filtreleri ve Aşırı Gerilim Koruyucular
- Amaç: Yüksek frekanslı parazitleri bastırmak ve voltaj dalgalanmalarına karşı korumak.
- Uygulama:
- AC ana güç kaynağına EMI hat filtreleri takın.
- Kontrol cihazı ve VFD’nin güç girişlerine aşırı gerilim koruyucular ekleyin.
Yazılım Yapılandırması: Sistemi Hayata Geçirme
Adım 1: Radonix Cam Pro'yu Kurun
- Yazılımı bilgisayarınıza indirin ve yükleyin.
- Kontrol cihazını açtığınızda LAN portundaki LED’leri gözlemleyin: biri sabit kalmalı, diğeri yanıp sönmelidir.
- Radonix kontrol cihazını bir LAN veya USB kablosu ile bilgisayara bağlayın.
Adım 2: Başlangıç Ayarları
- Yazılımı açın ve sistemi başlatın.
- Varsayılan ayarların uygulanmasını sağlamak için fabrika ayarlarına sıfırlama yapın.
Adım 3: Girişleri Yapılandırın
- Ayarlar > Sistem > Girişler yolunu izleyin.
- Her girişe görev atayın:
- Acil durdurma butonu için
EmergencyStop
. - Home sensörleri için
HomePin, X/Y/Z
. - Limit switchler için
LimitPin, X/-X
.
- Acil durdurma butonu için
- Her girişi fiziksel olarak etkinleştirerek ve yazılım tepkisini gözlemleyerek test edin.
Adım 4: Çıkışları Yapılandırın
- Ayarlar > Sistem > Çıkışlar yolunu izleyin.
- Her çıkışa görev atayın:
- Meşaleyi açmak için
C-CutPin
. - Z eksenini yukarı hareket ettirmek için röleyi etkinleştirmek üzere
C-ZfreePin,1
. - Z eksenini aşağı hareket ettirmek için röleyi etkinleştirmek üzere
C-ZfreePin,-1
.
- Meşaleyi açmak için
- Yazılımda çıkışları değiştirerek ve bağlı cihazları gözlemleyerek çıkışları test edin.
Adım 5: Eksen Kalibrasyonu
- Ayarlar > Sistem > Kalibrasyon yolunu izleyin.
- Her eksen için parametreleri girin:
- Birim Başına Adım (Steps per Unit): Kurşun vidası adımı, motor adımları ve enkoder çözünürlüğüne göre.
- Maksimum Hareket (Max Travel): Her eksenin maksimum hareket mesafesini tanımlayın.
- Hareket komutları vererek ve gerçek hareket mesafelerini ölçerek kalibrasyonu test edin.
Acil Durdurma (E-Stop)
Endüstriyel ortamlarda makineleri ve ekipmanları derhal durdurmak için kullanılan kritik bir tepki mekanizmasıdır. Yakın tehlikeye karşı koruma sağlamak için kullanılır. Bu eylem genellikle, etkinleştirildiğinde güç kaynağını kesen ve tüm işlemleri durduran bir acil durdurma düğmesi veya anahtarı aracılığıyla gerçekleştirilir; böylece kazaların, yaralanmaların veya makine ve personele zarar gelmesinin riski en aza indirilir.
Yapılandırılabilir Acil Durum Modu:
Kontrol sistemlerinde gelişmiş bir özellik olan bu mod, kullanıcıların sistem ayarları üzerinden özel acil durum tepkileri tanımlayıp yapılandırmasına olanak tanır. Bu mod, tespit edilen tehdidin doğasına ve ciddiyetine bağlı olarak farklı seviyelerde veya türlerde tepkilerin devreye alınmasını sağlayacak şekilde programlanabilir.
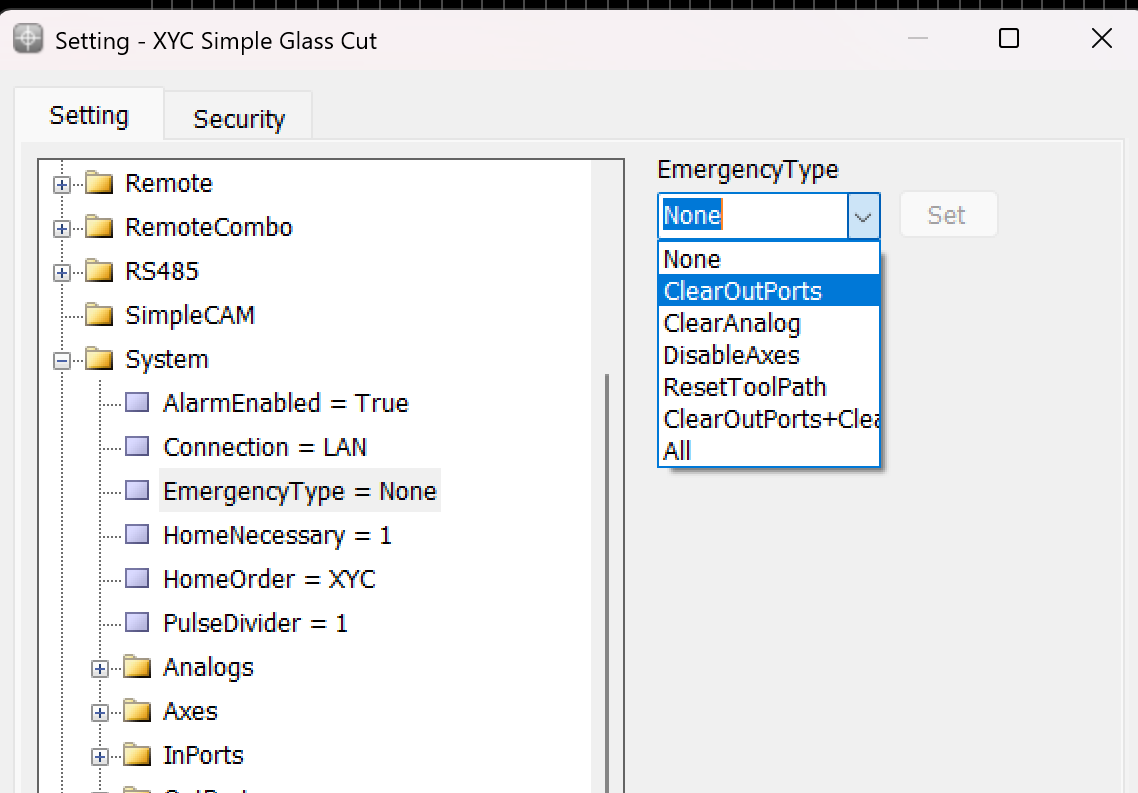
Bu değişken, Acil Durdurma düğmesine basıldığında gerçekleşecek işlemi belirlemek için kullanılır.
Acil Durum Türü
- None: Bu mod seçildiğinde, makine çalışması bir duraklamaya benzer şekilde olur. Cihaz tüm aktiviteleri durdurur fakat bu mod tetiklenirse aynı noktadan devam edemez.
- ClearOutPorts: Bu mod etkinleştirildiğinde eksenler durdurulur ve kontrol cihazının tüm dijital çıkış portları kapatılır. Bu, sıfırlanana kadar başka hiçbir komutun makineyi etkilememesini sağlar.
- ClearAnalog: Bu mod eksenleri durdurur ve tüm analog çıkışları kapatır. Bu, takım basıncı veya mil hızı gibi değişken çıkışlarla kontrol edilen unsurların devre dışı bırakılmasını sağlar.
- DisableAxes: Bu acil modda, makinenin eksenleri durdurulur ve pasif hale getirilir; bu, eksenleri hareket ettiren motorların devre dışı bırakılması anlamına gelir, böylece elle itilirse serbestçe hareket ederler ancak güce bağlı çalışmazlar.
- ResetToolPath: Bu mod, eksenleri durdurur ve takım yolunu programın başına sıfırlar. Bu, hasarı önlemek veya bir hatayı düzeltmek amacıyla sürecin baştan başlatılması gereken senaryolar için kullanışlıdır.
- ClearOutPorts+ClearAnalog: Bu kapsamlı acil durum modu, ClearOutPorts ve ClearAnalog etkilerini birleştirir; tüm dijital ve analog çıkışları durdurur, eksenleri devre dışı bırakır, motorları serbest bırakır ve takım yolunu ilk koordinata sıfırlar. Bu, sistemin çalışma durumunun tam bir sıfırlamasıdır.
- All: "All" seçildiğinde yukarıdaki tüm acil durum tepkileri etkinleştirilir ve sistemin maksimum düzeyde anında durması sağlanır. Tüm dijital ve analog çıkışlar kapanır; eksenler durdurulur ve serbest bırakılır; takım yolu sıfırlanır.
Home Sensörleri
Home sensörleri konumlar için çok önemlidir; bu sensörler sayesinde konumlar anlam kazanır. Tabla boyutunun tanımlanmasında etkilidirler. Sensörler makine sıfır noktası ya da makine orijinidir; eksenler sensörlere ulaştığında kontrol cihazı bunları algılar ve Siyah Izgara alanında kırmızı bir tabla oluşturur. Bu seçenek sayesinde bu alandaki her nokta kendi konumuna sahip olur, sensörler her eksende ayrı ayrı tanımlanır.
Gerçekte, home sensörleri CNC makinelerinin işlevselliği ve hassasiyeti açısından ayrılmaz parçalardır. Bu sensörlerin CNC kontrol cihazı ile nasıl etkileşime girdiğini ve makine çalışma alanını nasıl etkilediğini daha ayrıntılı inceleyelim:
Home Sensörlerinin Rolü ve İşlevselliği:
- Orijini Tanımlama: Home sensörleri makinenin sıfır noktası veya orijinini belirler. Bu nokta, makinenin çalışma alanındaki diğer tüm konumlar için referans görevi görür. Bu sayede makine tüm eksenler (genellikle X, Y ve Z) için başlangıç noktasını bilir.
- Tabla Boyutu ve Çalışma Alanı Tanımına Etkisi: Bu sensörler tarafından home pozisyonunun algılanması, doğrudan makinenin tabla boyutunun tanımlanmasını etkiler. Çünkü makine kontrol cihazı, çalışma alanının sınırlarını hesaplayıp tanımlamak için orijin noktasını kullanır. Makinenin hareketleri ve işlemleri bu hesaplanan sınırlar içinde kalır, bu da hassasiyeti sağlar ve makinenin kapasitesinin ötesine geçmesini önleyerek hasar veya hataları engeller.
- Kontrol Cihazı Arayüzünde Görselleştirme: Home sensörleri tetiklendiğinde, CNC kontrol cihazı bunu arayüzünde görsel olarak gösterebilir. Genellikle "siyah ızgara" üzerine serilmiş bir "kırmızı tablo" olarak gösterilir. Bu görsel sunum, operatörlerin makinenin aktif çalışma alanını görmesini ve anlamasını sağlar. Takımların nerede güvenle hareket edip çalışabileceğini gösterir ve çalışma alanının net bir şekilde sınırlarını belirler.
- Konumsal Hassasiyet: Bu tanımlı kırmızı tablo alanı içindeki her nokta, makinenin orijin noktasına göre özel bir konuma sahiptir ve bu, her eksendeki home sensörleri tarafından belirlenir. Bu düzenleme, makinenin hareketleri ve işlemleri üzerinde hassas kontrol sağlar. Makinenin gerçekleştirdiği her hareketin orijine göre tam olarak hesaplanmasını sağlayarak hem hassasiyeti hem de yapılan işin güvenilirliğini artırır.
- Operasyonel Güvenilirlik: Makinenin orijin noktasını düzenli olarak yeniden belirlemek için home sensörlerini kullanmak, operasyonel doğruluk ve güvenilirliği korumaya yardımcı olur. Bu özellikle hassasiyetin önemli olduğu uygulamalarda uzun vadeli tutarlılık için kritiktir.
Genel olarak, home sensörleri yalnızca makinenin çalışma sınırlarını tanımlayarak bir güvenlik mekanizması sağlamakla kalmaz, aynı zamanda tüm işleme görevleri için net ve güvenilir bir referans noktası oluşturarak operasyonel hassasiyeti artırır. Bu yapı, operasyon alanındaki her noktanın orijine göre doğru bir şekilde konumlandırılmasını garanti eder ve makinenin işlevselliğini hem öngörülebilir hem de hassas hale getirir.
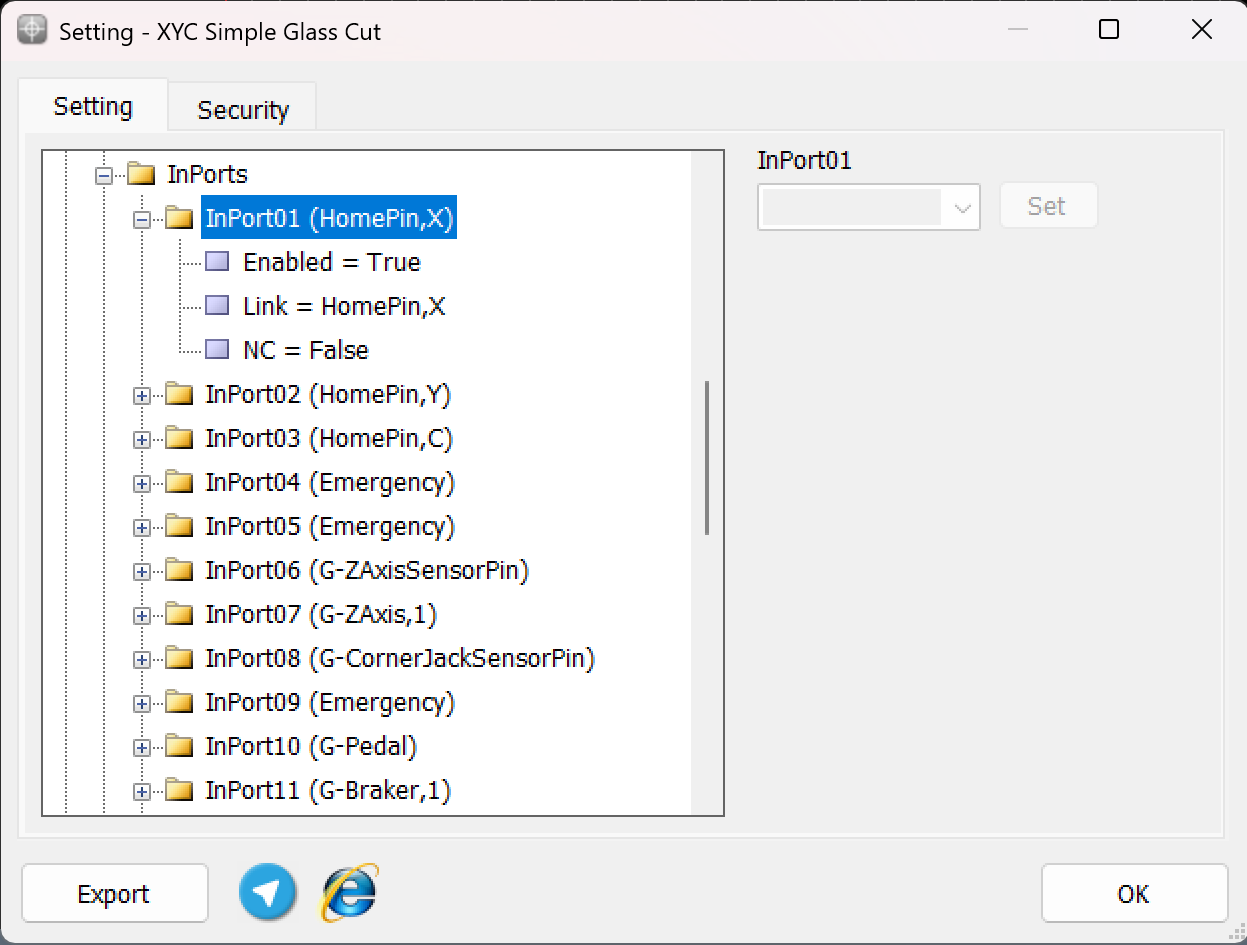
Home komutu verildikten sonra eksen hareketinin hassas bir şekilde durmasını sağlamak için, yukarıdaki açıklamada belirtildiği gibi uygun giriş bağlantılarının tanımlanması gerekir. Bu yapılandırma, makinenin her eksen için home konumunu doğru şekilde algılamasını sağlar.
Örneğin:
- HomePin,X giriş bağlantısı, X ekseni home konumunu algılamak için atanmıştır. Bu, X ekseninin sensörü, belirlenen home sensörünün önüne geldiğinde sistemin bunu home pozisyonu olarak tanımlayacağı anlamına gelir.
- Benzer şekilde, diğer eksenler olan Y, C, Z için HomePin,Y veya HomePin,C gibi uygun giriş bağlantılarının tanımlanması gerekir. Bu tanımlar, makinenin eksenleri ve sensör hizalamasına göre yapılmalıdır.
Bu yapısal kurulum, makinenin her eksen hareketini home pozisyonuna ulaştığında hassas şekilde durdurmasını sağlar ve home prosedürleri sırasında güvenli ve güvenilir çalışmayı garanti eder.
*Lütfen unutmayın: Genellikle, XY Cutter CNC makineleri eksen uzunlukları nedeniyle home sensörleri kullanmazlar.
Limit pin**
CNC makinelerinde, limit pinleri, makine eksenlerinin fiziksel sınırlarını aşmasını önlemek amacıyla hayati bir güvenlik özelliği olarak işlev görür. Bu pinler, tetiklendiğinde makineyi durduran mekanik veya sensör tabanlı cihazlar olan sert limit anahtarlarına bağlıdır.
Radonix kontrol cihazları, yazılım ayarları içinde yumuşak limitler de sunarken, sert limitler ek bir koruma katmanı sağlar ve beklenmedik durumlarda makinenin güvenli şekilde çalışmasını temin eder.
Limit Pinleri Hakkında Temel Noktalar:
-
Sert Limitler:
- Sert limitler, makineye monte edilmiş fiziksel limit anahtarlarına dayanır.
- Bir eksen limit anahtarına ulaştığında, karşılık gelen giriş bağlantısı (örneğin, G-LimitPin,X, G-LimitPin,Y veya G-LimitPin,Z) tetiklenir.
- Makine, mekanik bileşenlere zarar gelmesini önlemek için otomatik olarak durur.
-
Yumuşak Limitler:
- Yumuşak limitler, Radonix ayarları içinde tanımlanır.
- Operatör, her eksen için yazılım aracılığıyla izin verilen hareket aralığını belirler. Böylece eksen, bu tanımlı sınırların ötesine hareket edemez.
- Bu limitler dijital olarak izlenir ve fiziksel sert limitlere ulaşmadan önce bir önleme mekanizması olarak çalışır.
-
Çift Katmanlı Güvenlik Mekanizması:
- Sert limit pinleri ile yumuşak limitlerin birlikte kullanılması maksimum koruma sağlar:
- Yumuşak Limitler, yazılım tanımlı sınırlar içinde hareketleri durdurmak için ilk savunma hattı olarak çalışır.
- Sert Limitler, makine eksenlerinin kazara aşırı hareketini fiziksel olarak önleyen son güvenlik önlemidir.
- Sert limit pinleri ile yumuşak limitlerin birlikte kullanılması maksimum koruma sağlar:
Sert Limit Pinlerinin Yapılandırılması:
Radonix kontrol cihazlarında sert limitleri yapılandırmak için:
- Radonix yazılımında System > InPorts menüsüne gidin.
- İlgili limit anahtarları için giriş bağlantılarını atayın:
- X ekseni için G-LimitPin,X
- Y ekseni için G-LimitPin,Y
- Z ekseni için G-LimitPin,Z
- Enabled parametresinin True olarak ayarlandığından emin olun.
limitPin,X
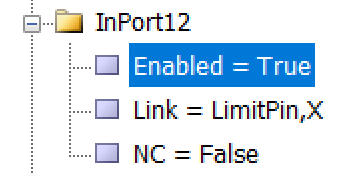
LimitPin,-X /// LimitPin,Y /// LimitPin,-Y /// LimitPin,Z /// LimitPin,-Z
Kurulum Sürecinde Gerekli Giriş ve Çıkışlar
XY Cutter makineleri, alev kesiciler ve plazma CNC makinelerini içeren belirli giriş ve çıkışlar, düzgün çalışmaları ve güvenliği için temel önemdedir. Bu bağlantılar, meşale, motorlar, sensörler ve güvenlik mekanizmaları gibi ana bileşenleri kontrol etmek için hayati önem taşır. Ayrıca, kritik olmayan ancak işlevselliği artıran ve kullanım kolaylığı sağlayan başka bağlantılar da vardır. Bunlar bu bölümde daha ayrıntılı açıklanacaktır.
Fonksiyonlar
Fonksiyonlar, çeşitli yollarla çağrılabilen ve yürütülebilen komutlardır (dijital giriş tanımı, yazılım ekranı buton tanımı, M-Kodu tanımı, uzaktan kumanda veya klavye tuşu tanımı vb.). Her fonksiyon, gerçekleştirdiği işlemin türünü belirleyen birkaç argüman içerir. Cutter arayüzünün fonksiyonları şunlardır:
Cut-C: C-CutPin çıkışını etkinleştirmek veya devre dışı bırakmak için kullanılır ve aşağıdaki argümanları içerir:
➢ C-Cut,0: Bu fonksiyon çağrıldığında C-CutPin çıkışı devre dışı bırakılır.
➢ C-Cut,1: Bu fonksiyon çağrıldığında C-CutPin çıkışı etkinleştirilir.
➢ C-Cut,2: Bu fonksiyon her çağrıldığında, C-CutPin çıkışının durumu açık-kapalı arasında değiştirilir (anahtar gibi çalışır).,
ManualCut-C: Cutter arayüzlerinde, operatörler yüklü tasarımı kesme çıkışı etkinleştirilmeden ve yüksek hızda Demo modunda bir kez çalıştırabilirler (bu modun hızı Setting→System→ToolPath→TraverseVelocity bölümünden ayarlanabilir). Bu, operatörlerin tasarımın doğru çalıştırıldığından ve tüm kesim yolunun ham malzeme ile düzgün hizalandığından emin olmasını sağlar. Bu modu etkinleştirmek için aşağıdaki argümanları içeren C-ManualCut fonksiyonu kullanılır:
➢ C-ManualCut,0: Bu fonksiyon çağrıldığında Demo modu devre dışı bırakılır.
➢ C-ManualCut,1: Bu fonksiyon çağrıldığında Demo modu etkinleştirilir.
➢ C-ManualCut,2: Bu fonksiyon her çağrıldığında, Demo modunu aktif/pasif arasında değiştirir (anahtar gibi çalışır).
Girişler
C-Cutsensorpin : Bu giriş tanımlıysa, C-CutPin çıkışı etkinleştirildikten sonra cihaz duraklar ve bu girişin etkinleşmesini bekler. Bu giriş etkinleştiğinde cihaz kesme işlemine devam eder. Bu girişin adında ‘sensor’ kelimesi geçmesi, illa ki bir sensör olduğu anlamına gelmez. Bu, operatörün basabileceği bir buton da olabilir.
C-PreCutSensorPin : Bu giriş tanımlıysa, C-CutPinPre çıkışı etkinleştirildikten sonra cihaz duraklar ve bu girişin etkinleşmesini bekler. Bu giriş etkinleştiğinde cihaz kesme işlemine devam eder. Yukarıda açıklandığı gibi, adında ‘sensor’ kelimesi geçse de bu giriş illa ki bir sensör olmak zorunda değildir; bu, operatörün basabileceği bir buton da olabilir.
FreeSensorPin-C: Eğer cihazın Z ekseni standart bir DC veya AC motorla donatılmışsa ve yukarı/aşağı hareketi iki ayrı röle ile kontrol ediliyorsa, bu giriş, yukarı ve aşağı hareketi sınırlayan bir mikro anahtar veya sensör varlığında kullanılabilir. Sonuç olarak, yukarı hareketi sınırlayan mikro anahtar veya sensör için C-ZFreeSensorPin,1 bağlantılı giriş kullanılmalı ve aşağı hareketi sınırlayan için C-ZFreeSensorPin,-1 bağlantısı kullanılmalıdır.
Çıkışlar
C-PreCutPin: Bu, cihaz kesme noktasına ulaştıktan sonra etkinleşen ilk veya ön kesim çıkışıdır. Girişler bölümünde C-PreCutSensorPin tanımlanmışsa, bu giriş etkinleşene kadar çıkış aktif kalır ve C-PreCutSensorPin etkinleştikten sonra devre dışı kalır. C-PreCutSensorPin tanımlı değilse, bu çıkış PreCutTime parametresiyle belirlenen süre boyunca aktif kalır ve sonraki aşamaya geçilir. Bu durumda, operatör C-Cut fonksiyonunu çağırarak (Cut butonuna basarak) ön kesim süresini atlayabilir ve doğrudan kesim aşamasına geçebilir.
C-CutPin : Bu, ikinci aşama veya kesim çıkışıdır ve ilk aşamanın tamamlanmasının ardından etkinleşir, ancak cihaz hareket etmez. Bu çıkış etkinleştirildikten sonra, eğer girişlerde C-CutSensorPin tanımlıysa, bu giriş etkinleştiğinde cihaz hareket etmeye başlar ve kesim işlemini gerçekleştirir. C-CutSensorPin tanımlı değilse, cihaz C-CutTime parametresiyle belirlenen sürenin ardından hareket etmeye ve kesim işlemine başlamaya başlar. Bu durumda, operatör Run fonksiyonunu çağırarak (Play veya Start butonuna basarak) kesim yolunda hareket etmeye başlayabilir.
C-PreCutPin+CutPin: CutPin-C veya PreCutPin-C çıkışlarından herhangi biri aktif olduğunda bu çıkış aktiftir. Her iki çıkış da devre dışı bırakıldığında bu çıkış da devre dışı kalır.
PreCutPin+CutPin+PostCutPin-C: CutPin-C, C-PreCutPin veya C-PostCutPin çıkışlarından herhangi biri aktif olduğunda bu çıkış aktiftir. Tüm bu çıkışlar devre dışıysa, bu çıkış da devre dışı olur.
C-PostCutPin: Bu çıkış, kesim işlemi tamamlandıktan ve CutPin-C çıkışı devre dışı bırakıldıktan hemen sonra etkinleştirilir. Cihaz o noktada durur. C-PostCutTime parametresiyle belirlenen sürenin ardından cihaz yeniden hareket eder ve kesim yapmak üzere bir sonraki noktaya geçer.
FreePin-C: Z ekseni standart bir DC veya AC motorla donatılmışsa ve yukarı/aşağı hareketi iki ayrı röle ile kontrol ediliyorsa, bu ekseni yazılım veya uzaktan kontrol etmek amacıyla iki ayrı çıkış tanımlanabilir. Bu amaçla, yukarı hareket rölesi için C-ZFreePin,1 bağlantılı çıkış ve aşağı hareket rölesi için C-ZFreePin,-1 bağlantılı çıkış tanımlanır.
Parametreler
AutoCut: Eğer CutSensorPin-C ve PreCutSensorPin-C girişleri tanımlı değilse ve bu parametrenin değeri True olarak ayarlanmışsa, cihaz her parçanın kesim başlangıç noktasına ulaştığında C-PreCutPin çıkışı etkinleştirilir. PreCutTime süresi geçtikten sonra C-CutPin çıkışı otomatik olarak etkinleştirilir ve CutTime süresi geçtikten sonra cihaz otomatik olarak kesime başlar. Ancak bu parametre False olarak ayarlanmışsa, cihaz her parçanın kesim başlangıç noktasına ulaştığında C-PreCutPin çıkışı etkinleştirilir ve operatör C-CutPin çıkışını etkinleştirene kadar bekler. C-CutPin etkinleştirildikten sonra, operatörün parçayı kesmeye başlamak için başlat düğmesine basması gerekir.
CutTime: Eğer CutSensorPin-C girişi tanımlı değilse ve TrueAutoCut= parametresi true olarak ayarlanmışsa, C-CutPin çıkışı etkinleştirildikten sonra cihaz bu parametrede belirtilen süre kadar bekler ve ardından parçayı kesmeye başlar. Bu parametrenin birimi TimeUnit parametresi ile belirlenir.
CutVelocity: Operatörün bir parçanın belirli bir kısmını manuel olarak kesmesi gerekiyorsa, bu, C-CutPin çıkışını etkinleştirerek ve manuel hareket tuşları (JOG) kullanılarak yapılabilir. Bu koşullar altında cihazın hareket hızı bu parametre ile belirlenir ve mm/s (milimetre/saniye) cinsindendir.
JogDisplaceReferenceEnable: Bu parametrenin değeri True olarak ayarlanmışsa, cihazın manuel hareketi için Sürekli (Continuous) moduna ek olarak Adım (Step) ile belirlenen üçüncü bir mod daha eklenir. Bu modda, iş parçasının referans konumu ya da sıfır noktası, cihazın hareketi kadar kayar. Bu parametre False olarak ayarlanırsa bu mod artık görüntülenmez. Diğer arayüzlerin aksine, bu butonun Type parametresinin Toggle değil Button türünde olduğunu belirtmek gerekir.
JogMode: JogDisplaceReference modunun bulunduğu arayüzlerde, manuel hareket modunun yani JogMode’un kaydedilmesini ve yazılımın sonraki çalıştırmalarında varsayılan ayar (Continuous mode) olarak geri dönmemesini sağlamak için ayarlarda bir parametre bulunmaktadır. Bu nedenle bu parametre özel bir yapılandırma gerektirmez.
PostCutTime: Bu parametre, kesim işlemi tamamlandıktan ve C-CutPin çıkışı devre dışı bırakıldıktan sonra cihazın durma süresini ve ardından bir sonraki kesilecek parçanın başlangıç noktasına hareket süresini belirler. Bu parametrenin birimi TimeUnit parametresiyle belirlenir.
PreCutTime: Eğer CutSensorPinPre-C girişi tanımlı değilse ve TrueAutoCut= parametresi true olarak ayarlanmışsa, C-PreCutPin çıkışı etkinleştirildikten sonra cihaz bu parametrede belirtilen süre boyunca bekler ve ardından C-CutPin çıkışını etkinleştirir. Bu parametrenin birimi TimeUnit parametresiyle belirlenir.
SheetAlignBaseAxis: Bu parametre, Sheet Align ile ilgili hesaplamalarda temel alınacak ekseni belirler. Bu parametre hakkında daha fazla bilgi Sheet Align bölümünde verilecektir.
TimeUnit: Bu parametre, zamanla ilgili parametrelerin birimini belirtir. ‘ms’ milisaniyeyi, ‘s’ ise saniyeyi temsil eder.
Sheet Align
Makinenin kesim tablasına iş parçası yerleştirilirken, parçanın hareket eksenleriyle hizalanmasını engelleyen durumlar olabilir (iş parçası eğri yerleştirilmiş olabilir ya da teknik tabirle kare olmamış olabilir).
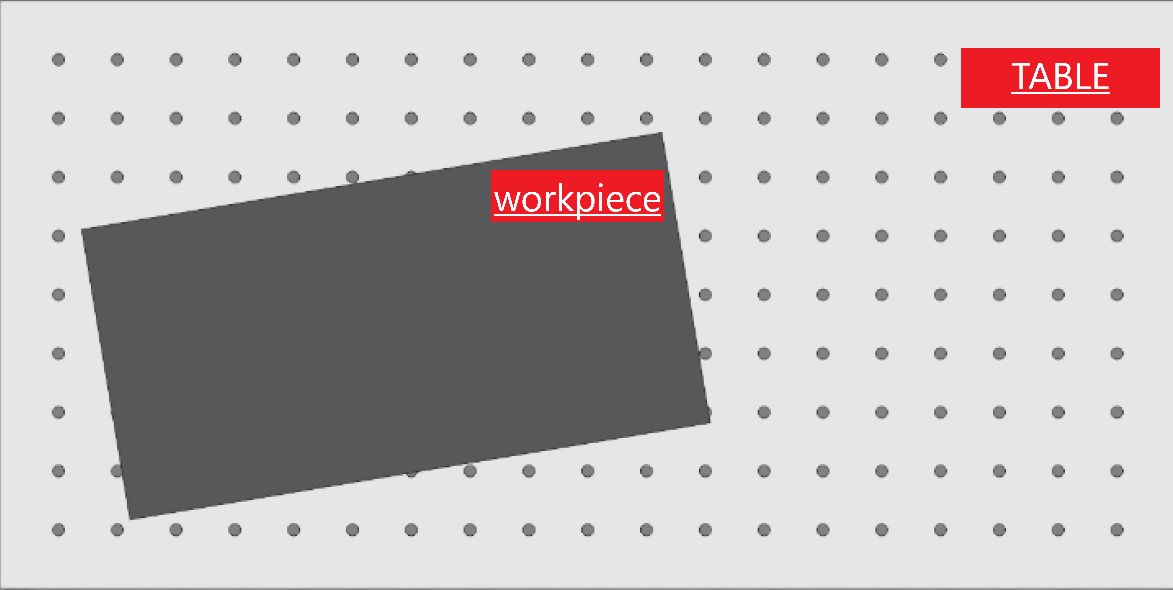
Bu koşullarda, yüklü tasarımın sıfır noktası etrafında, iş parçasının tabla ile yaptığı eğiklik açısına göre döndürülmesi gerekir ki tasarım iş parçası ile hizalansın. Tasarımın ne kadar döndürülmesi gerektiğini hesaplayabilmek için, iş parçası üzerinde iki nokta yazılıma tanıtılmalıdır. Aşağıda gösterildiği gibi, yazılım bu iki noktayı kullanarak dönme açısını hesaplayabilir.
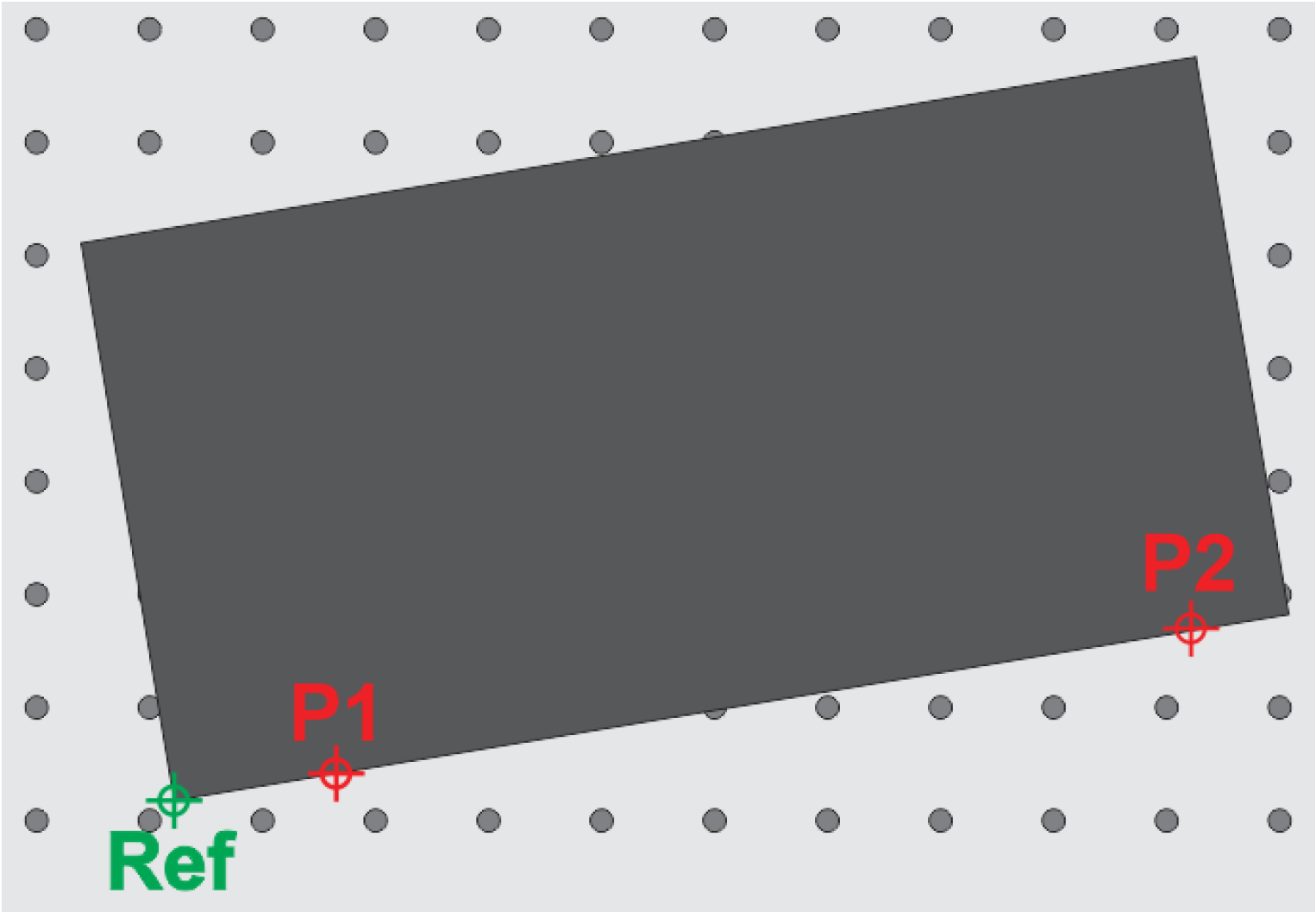
Bu işlem için, istenen tasarım yüklendikten sonra, kesici nozül ucu sacın kenarına teğet bir noktaya getirilmelidir. İlk noktada P1 butonuna, ikinci noktada P2 butonuna basılarak bu iki nokta yazılıma tanıtılır. Böylece, bu iki nokta arasında mavi bir çizgi çizilir ve bu çizgi iş parçasının kenarına tam teğet olur.
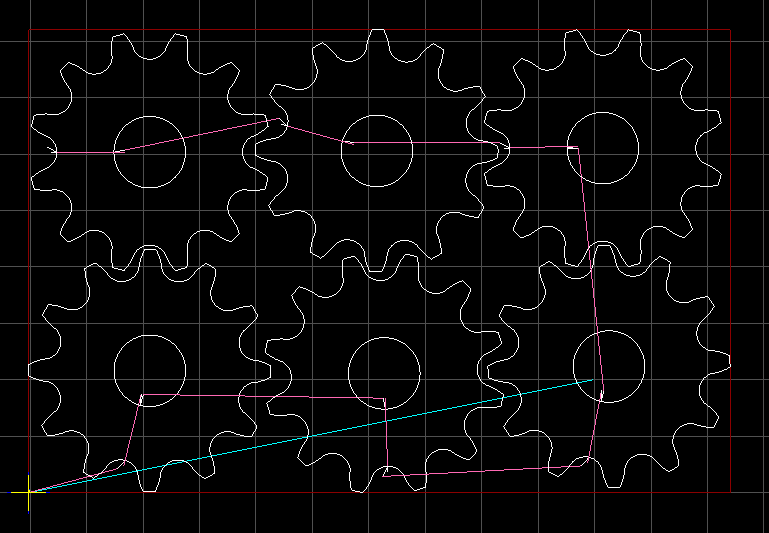
Bundan sonra, Sheet Align butonuna basıldığında, tasarım mavi çizgiye teğet olur ve iş parçası üzerine tamamen oturur.
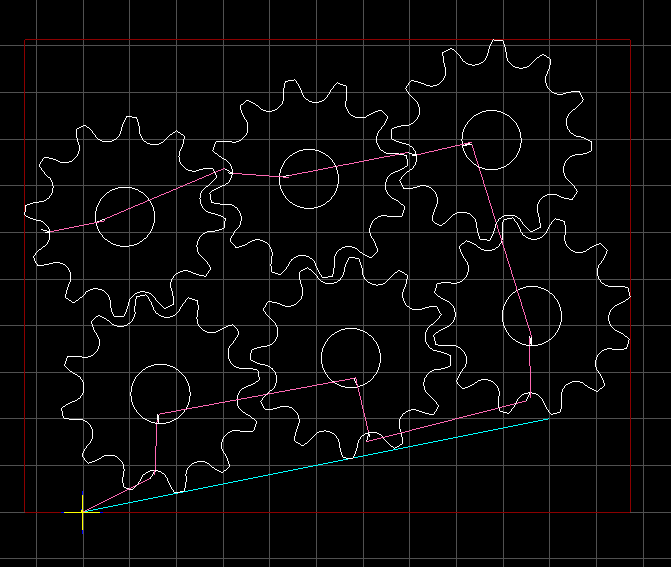
İki nokta (P1 ve P2) arasındaki mesafe ne kadar büyük olursa, bu işlemin o kadar hassas yapılacağı unutulmamalıdır. Şimdi aşağıdaki iki senaryodan biri ortaya çıkar:
SheetAlignBaseAxis=X: Bu senaryoda, noktalar X ekseni boyunca seçilmiştir ve yüklenen tasarım P1 ve P2 noktalarını birleştiren çizgi ile hizalanır (aşağıda gösterildiği gibi):
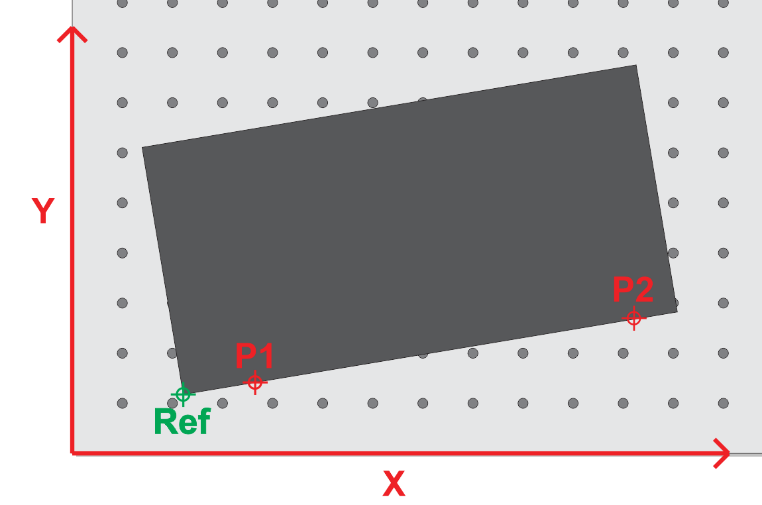
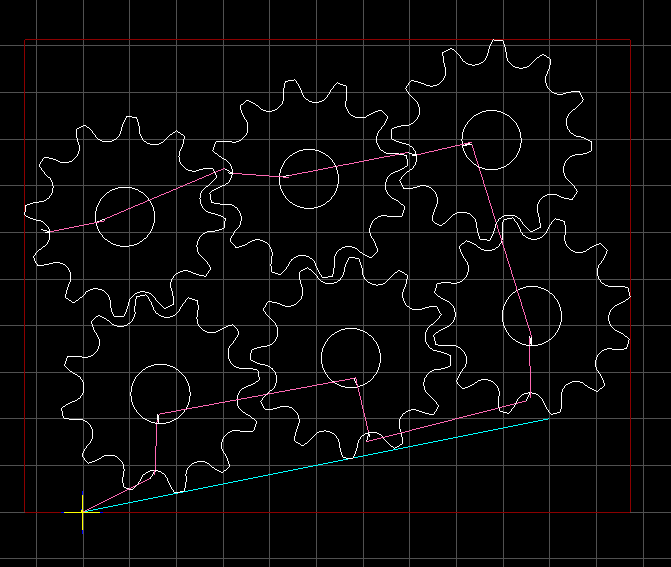
SheetAlignBaseAxis=Y: Bu senaryoda, noktalar Y ekseni boyunca seçilmiştir ve yüklenen tasarım P1 ve P2 noktalarını birleştiren çizgi ile hizalanır (aşağıda gösterildiği gibi):
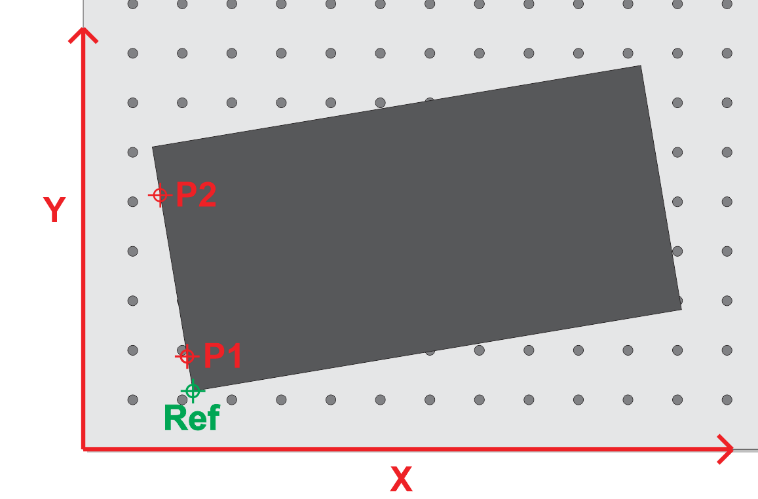
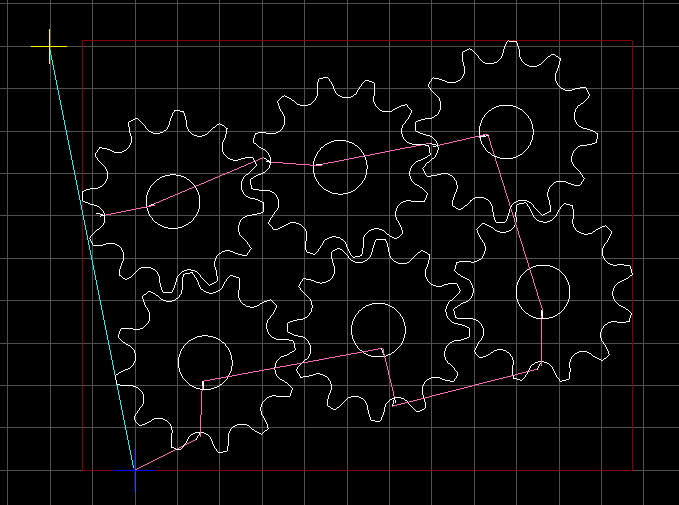
Kalibrasyon
Kalibrasyon Tanımı
Kalibrasyon, bir eksenin hareket değerinin standart bir birim veya belirli bir değer ile hizalanması sürecini ifade eder. Endüstriyel cihazlarda yaygın birimler genellikle milimetre, santimetre, metre, inç, feet, derece vb. olup ihtiyaç doğrultusunda kullanılabilir. Bu nedenle, milimetre birimi için kalibrasyon kavramı, istenen eksenin hareket değerinin milimetre birimi ile eşleştirilmesi olarak ifade edilebilir. Yani, ölçüm aletleri ile ölçüm yapıldığında, eksenin hareketinin sayısal değeri milimetre cinsinden ölçülen değere uygun olmalıdır.***
Kalibrasyondaki Motor Tipleri
Radonix kontrol cihazlarında, her eksenin kalibrasyon prosedürü motor tipine göre belirlenir. Çeşitli motor tipleriyle uyumluluğu sağlamak için temel gereklilik, seçilen motorun hem pulse hem de yön sinyallerini desteklemesidir.
Servo motorlar
Servo motor, açısal veya lineer konum, hız ve ivme üzerinde hassas kontrol sağlayan döner veya lineer aktuatör türüdür. Genellikle konum geri bildirimi için sensörlü bir motordan oluşur. Servo motorlar, robotik, CNC makineleri ve otomatik üretim gibi hassas konumlama gerektiren uygulamalarda vazgeçilmezdir. Hata algılayıcı geri bildirim sinyallerini kullanarak hareket parametrelerini ayarlar ve servo mekanizmalar aracılığıyla performansı düzeltir.
Elektronik Dişli Kutusu:
Elektronik Dişli Kutusu, modern servo sistemlerinde, özellikle otomasyon ve robotikte kullanılan servo motorları içeren uygulamalarda önemli bir bileşendir. Bu teknoloji, fiziksel dişli değişiklikleri yerine motorun hız ve tork değerini elektronik olarak ayarlayan sanal bir dişli kutusu gibi çalışır. Motorun giriş sinyallerinin frekans ve genliğini manipüle ederek, fiziksel dişli değişimine gerek kalmadan motor çıkış karakteristiklerini belirli görevler için optimize eder.
Bir sonraki adım için kritik konu: Kod Çözünürlüğü
Kod Çözünürlüğü (Encoder Resolution), servo motorların temel bir özelliğidir ve bir motor şaftının tam devri başına sensörün ürettiği pulse sayısını belirtir. Devrim başına pulse (PPR) cinsinden ifade edilen bu özellik, motorun konum, hız ve ivme kontrol hassasiyetini tanımlamak için kritiktir.
Örneğin, Delta servo motorunun B2 modeli, 160.000 PPR çözünürlüğüne sahiptir. Bu, motor şaftı her tam dönüş yaptığında enkoderin 160.000 ayrı sinyal ürettiği anlamına gelir. Aynı markanın A2 modeli ise 1.280.000 PPR gibi çok daha yüksek bir çözünürlük sunar. Bu yüksek çözünürlük, daha ince ayar ve daha hassas kontrol imkanı sağlar, bu da titizlik gerektiren konumlama ve detaylı hareket kontrolü gereken uygulamalarda hayati önemdedir.
Yüksek çözünürlüklü enkoderler, robotik, CNC makineleri ve otomatik montaj hatları gibi kesin hareketlerin kritik olduğu alanlarda özellikle faydalıdır. Enkoder çözünürlüğü ne kadar yüksekse, tespit edilip kontrol edilebilecek hareket adımı o kadar küçülür, böylece sistemin doğruluğu ve çıktı kalitesi artar. Bu yetenek, yüksek hassasiyet gerektiren görevlerin performansını optimize etmek, her bileşenin sıkı toleranslar içinde çalışmasını ve sıkı kalite standartlarına uyum sağlamasını güvence altına almak için kritik öneme sahiptir.
Enkoder çözünürlüğünü uygun şekilde anlamak ve ayarlamak, otomatik sistemlerin kalibrasyonunda kritik bir ilk adımdır. Bu, makinenin sorunsuz çalışmasını ve üretilen her parçanın hassas spesifikasyonlara uygun olmasını sağlar; böylece hatalar azalır ve üretim süreçlerinin genel verimliliği artar. Motor hareketleri üzerindeki bu ayrıntılı kontrol, modern otomatik sistemlerin yüksek güvenilirlik ve doğrulukla karmaşık görevleri yerine getirmesini mümkün kılar.
Servo Sürücülerde Elektronik Dişli Oranının (E.G.) Ayarlanmasına Genel Rehber
Genel Bakış
Servo sürücüler için Elektronik Dişli Oranını (E.G.) yapılandırmak, hassas hareket kontrolü gerektiren uygulamalarda performanslarını optimize etmek için kritik öneme sahiptir. Bu rehber, E.G.’yi genel olarak nasıl ayarlayacağınıza dair adımları sunar; Delta B2 servo sürücüyü örnek olarak kullanarak süreci açıklar.
Gereksinimler
- Entegre enkoderli servo sürücü
- Pulse sinyalleri üretebilen kontrol cihazı (ör. CNC kontrol cihazı)
- Hem servo sürücü hem de kontrol cihazı teknik özellikleri
Adım Adım Yapılandırma
Adım 1: Enkoder Çözünürlüğünü Anlayın
- Amaç: Servo motor şaftının bir tam dönüşü için gereken pulse sayısını yani enkoder çözünürlüğünü tanımlayın.
- Genel Bilgi: Enkoder çözünürlüğü, devrim başına pulse (PPR) cinsinden belirtilir. Bu, servo sürücünün motor pozisyonunu ne kadar hassas kontrol edebileceğini belirler.
Adım 2: Motor Hızını Saniyedeki Devir (RPS) Olarak Hesaplayın
- Amaç: İstenen motor hızını RPM (dakika başına devir) cinsinden RPS (saniye başına devir) cinsine çevirerek kontrol cihazının çıkış frekansıyla eşleştirmek.
- Prosedür:
Formül: RPS = RPM / 60 Bu hesaplama, zaman temelini dakikadan saniyeye dönüştürerek pulse çıkışıyla senkronizasyonu kolaylaştırır.
Adım 3: Gereken Pulse Saniye Başına Sayısını Belirleyin
- Amaç: RPS ve enkoder çözünürlüğüne dayalı olarak saniye başına gereken toplam pulse sayısını hesaplamak.
- Prosedür:
RPS’i enkoder çözünürlüğü ile çarparak saniye başına gereken pulse sayısını bulun. Örnek Formül: Pulse saniyede = RPS × Enkoder Çözünürlüğü Pulse saniyede = RPS × Enkoder Çözünürlüğü
Adım 4: Elektronik Dişli Oranını (E.G.) Ayarlayın
-
Amaç: Kontrol cihazının çıkışını servo motorun pulse gereksinimlerini karşılayacak şekilde ayarlamak.
-
Prosedür:
E.G. = Gereken Pulse / Kontrolcünün Pulse Kapabilitesi
Hesaplanan E.G. oranına göre kontrolcünün ayarlarını yapın.
Örnek: Delta B2 Servo Sürücü
-
Motor Hızı: 3000 RPM
-
Enkoder Çözünürlüğü: 160.000 PPR
-
Kontrolcünün Pulse Kapabilitesi: 500.000 pulse/saniye
-
Hesaplama:
RPM’den RPS’e: 3000 / 60 = 50 Gereken Pulse: 50 × 160.000 = 8.000.0008.000.000 pulse/saniye = 50 × 160.000
E.G.: E.G. = 8.000.000 / 500.000 = 16
E.G. Oranı Ayarı: 16:1
Test ve Doğrulama
Amaç: Yeni ayarlar altında servo sistemin doğru çalıştığından emin olmak.
Prosedür:
Test çalıştırması yaparak servo sürücünün doğruluğunu ve tepki hızını kontrol edin.
Hareketi gözlemleyerek beklenen parametrelerle uyumlu olduğunu onaylayın.
Ek Notlar
Detaylı spesifikasyon ve gelişmiş ayarlar için ilgili servo sürücü kılavuzlarına başvurun.
Optimal performansı sürdürebilmek için düzenli bakım kontrolleri ve yeniden kalibrasyon önerilir.
Bu kapsamlı yaklaşım, otomasyon ve robotik gibi yüksek hassasiyet gerektiren sistemlerde çeşitli servo sürücü tiplerinin etkin şekilde entegre edilip kullanılmasını sağlar.
Step motorlar
Step motor, elektriksel pulse’ları ayrı mekanik hareketlere dönüştüren elektromekanik bir cihazdır. Elektromanyetizma prensibine dayanarak, sabit adım artışlarıyla döner ve hassas hareket ve konumlama sağlar. Bu özellik, step motorları 3D yazıcılar, CNC makineleri ve robotik gibi yüksek doğruluklu ve kontrollü hareket gerektiren uygulamalar için ideal kılar. Açık döngü (open-loop) kontrol ile kısa mesafe veya sınırlı açı uygulamalarında basit fakat hassas kontrol sunar.
Step motor sürücüleri genellikle motor çalışma ayarlarını yapılandırmaya yarayan DIP (Dual In-line Package) anahtarlar içerir. Bu anahtarlar, uygulamanın gereksinimlerine göre step motor performansını ayarlamak için kritik öneme sahiptir. İşte step motor sürücülerindeki DIP anahtarlarla kontrol edilebilen yaygın ayarların özeti:
Step Motor Sürücülerinde Yaygın DIP Anahtar Ayarları:
Mikroadımlama:
Mikroadımlama, step motorları küçük adımlarla hareket ettirerek daha pürüzsüz hareket ve yüksek çözünürlüklü konumlama sağlar. DIP anahtarlar, tam adım, yarım adım, çeyrek adım vb. mikroadımlama konfigürasyonlarını ayarlamaya olanak tanır.
Akım Ayarı:
Performans ve verimliliği optimize etmek için, step motorun aldığı akım DIP anahtarlarla ayarlanabilir. Bu, motorun özelliklerine uygun akım sağlayarak düşük performans veya aşırı ısınmayı önler.
Decay Modu:
Decay modu ayarları, motor akımının kesildiği döngüde ne kadar hızlı azalacağını kontrol eder. Uygun decay modu ayarları, özellikle yüksek hız veya değişken yük altında motor performansı ve tepki süresini iyileştirir.
Tork Ayarları:
Some sürücüler, motorun tork çıkışını DIP anahtarlarla ayarlamaya olanak verir. Bu ayar, işlem sırasında motora farklı yük veya basınç beklendiğinde kritiktir.
DIP Anahtarları Nasıl Kullanılır:
Kılavuza Danışın: Her DIP anahtarın neyi kontrol ettiğine dair talimatlar için step motor sürücüsünün kılavuzunu mutlaka kontrol edin. Bu kılavuz, anahtarları doğru şekilde ayarlamanız için gereklidir.
Güç Varken Ayarlamayın: Motor veya sürücünün zarar görmesini önlemek için DIP anahtarları enerji kesikken ayarlamak önemlidir.
Test ve Ayar: DIP anahtarları ayarladıktan sonra, motorun yük altında beklendiği gibi çalıştığından emin olmak için testler yapın. Gerekirse performansı elde etmek için ayarları yeniden düzenleyin.
Gerçekten de, step motor sürücüsünde mevcut en yüksek mikroadımlama değerine ayarlamak çoğu uzman tarafından en pürüzsüz hareketi elde etmek için önerilir. Bu uygulama, yüksek hassasiyet gerektiren uygulamalarda, örneğin yüksek hassasiyetli işleme, robotik veya tıbbi ekipmanlarda yaygındır. İşte bu önerinin neden yaygın olduğuna ve nasıl etkili şekilde uygulanacağına dair daha ayrıntılı açıklama:
Neden En Yüksek Mikroadımlama Değerine Ayarlanmalı?
- Artan Çözünürlük ve Pürüzsüzlük:
- Daha yüksek mikroadımlama değerleri, motorun tam bir devri tamamlarken kullandığı adım sayısını artırır. Bu, adım aralığını küçülterek hareketi yumuşatır, daha düşük mikroadımlama ayarlarında daha belirgin olan titreşim ve rezonansı azaltır.
- Azalan Mekanik Gürültü:
- Küçük adım artışları, daha sessiz çalışma sağlar. Adımlar arasındaki daha yumuşak geçiş, step motorların ani hareketlerinden kaynaklanan gürültüyü minimize eder; bu, gürültü duyarlı ortamlarda avantajlıdır.
- Artan Konumsal Doğruluk:
- Mikroadımlama çözünürlüğü artırsa da, zamanla biriken adım hataları nedeniyle mutlak konumsal doğruluğu doğrudan artırmaz. Ancak pratik uygulamalarda, ince adımlar motor konumlama üzerinde daha hassas kontrol sağlar; bu, hassas operasyonlar için kritik olabilir.
Kalibrasyon Yöntemleri
Radonix kontrol cihazında her eksen ayrı ayrı kalibre edilebilir; hatta eksenler farklı birimlerde kalibre edilebilir. Bu kontroldeki kalibrasyon faktörünü temsil eden değişken, Step değişkenidir. Buna erişmek için Radonix yazılımını açtıktan sonra Ayarlar penceresinden System dalına, ardından 1 ile 6 arasındaki eksen numarasını belirten Axis alt dalına gidilmelidir.
Şimdi bu E.G kalibrasyon süreci iki şekilde uygulanabilir
1. Radonix CAM Kalibratörü ve Ölçüm
Bu kalibrasyon yönteminde temel, ölçüm araçları ve ekipmanları ile yapılan ölçümlerdir. Dolayısıyla ölçüm aletinin hassasiyeti, ölçüm doğruluğu ve cihazın mekanik hataları kalibrasyon kalitesini doğrudan etkiler. Kimi zaman motor, dişli kutusu, kasnak ve dişli çark bilgileri mevcut olmadığından bu yöntem hesaplamalı yöntemler kadar hassas olmasa da yaygın olarak kullanılır. Yöntemin temeli, belirli bir pulse sayısı için yer değiştirme değeri ölçmektir. Ölçüm yöntemini kolaylaştırmak, doğruluğu artırmak ve kalibrasyonu hızlandırmak için Radonix, ana Radonix yazılımıyla otomatik kurulan ücretsiz CAM-Pro Calibrator yazılımını sağlar. Eksende fiziksel yer değiştirme ölçümü ve bu yer değiştirme için gereken pulse sayısına dayanarak yazılım adım (step) değerini hesaplar.
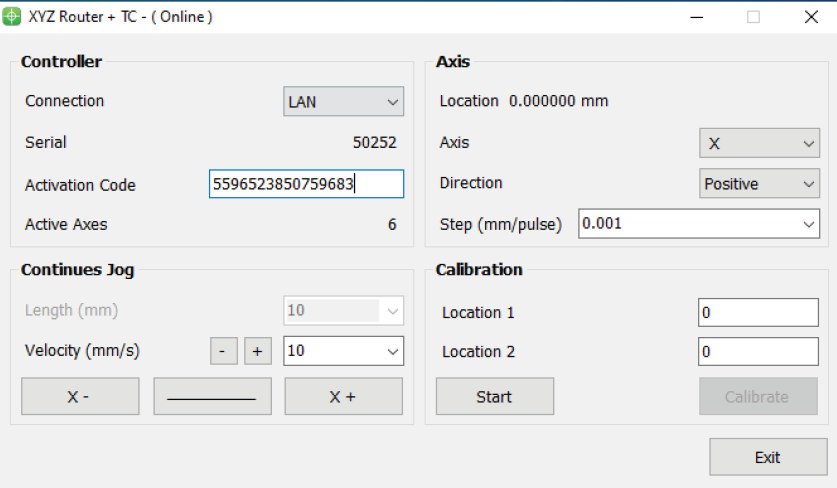
Bu yöntemde pulse sayımı kontrol cihazının sorumluluğunda olduğundan pulse ölçüm hatası yoktur. Dolayısıyla ölçüm doğruluğu fiziksel ölçüm doğruluğuna bağlıdır. Ayrıca ölçülen iki nokta arasındaki mesafe ne kadar büyükse pay artar, sabit hata payına göre hesaplanan step değeri o kadar hassas olur. Bu nedenle iki nokta bazlı kalibrasyon daha doğru sonuç verir.
CAM-Pro Calibrator’a Giriş
Önceki bölümde açıklandığı gibi CAM-Pro Calibrator yazılımı, CAM-Pro yazılımı ile birlikte kurulur. Kurulumdan sonra Calibrator’ı bulmanın iki yolu vardır. Birinci yönteme göre, Windows’ta varsayılan olarak C sürücüsüne gidin, Program Files (x86) klasörünü açın, Radonix klasörüne girin; buradaki CAMProCalibrator çalıştırılır. İkinci yönteme göre Başlat menüsünden Radonix CAM-Pro Calibrator aratılır.
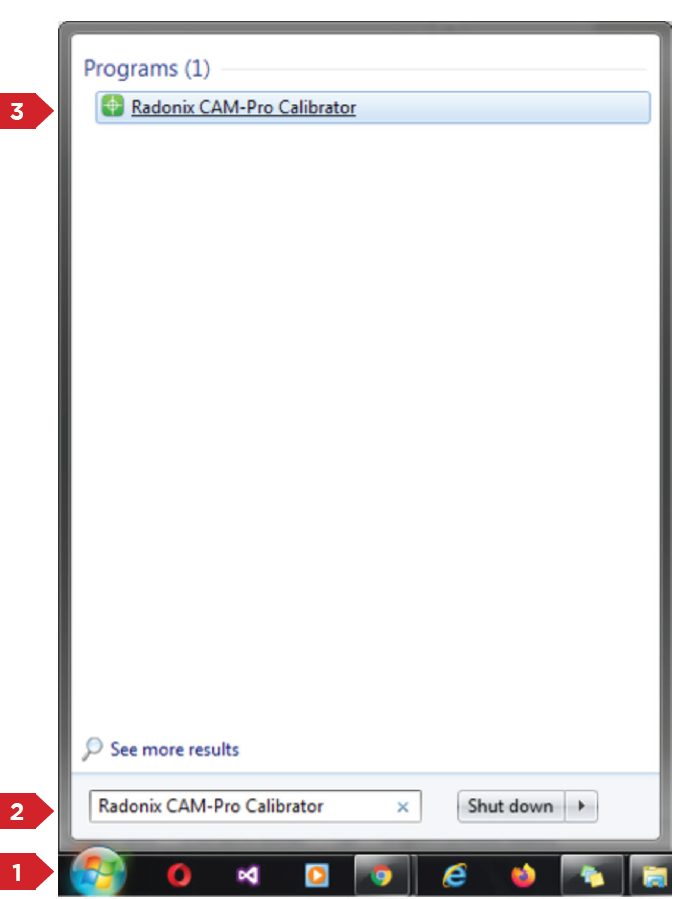
Bu program iki pencereden oluşur. Birinci pencere, bilgisayarda birden fazla aktif arayüz varsa görünür (Şekil 3). Buradan istenen arayüz seçilip “Ok” tuşuna basılarak başlatılır. Yalnızca bir arayüz aktifse bu pencere atlanır ve ana pencere doğrudan açılır.
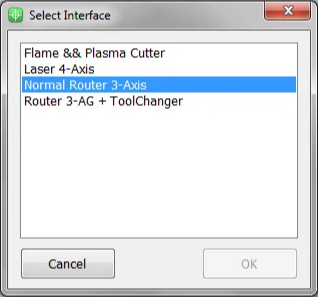
CAM-Pro Calibrator açıldığında Şekil 4’teki bileşenler görünür:
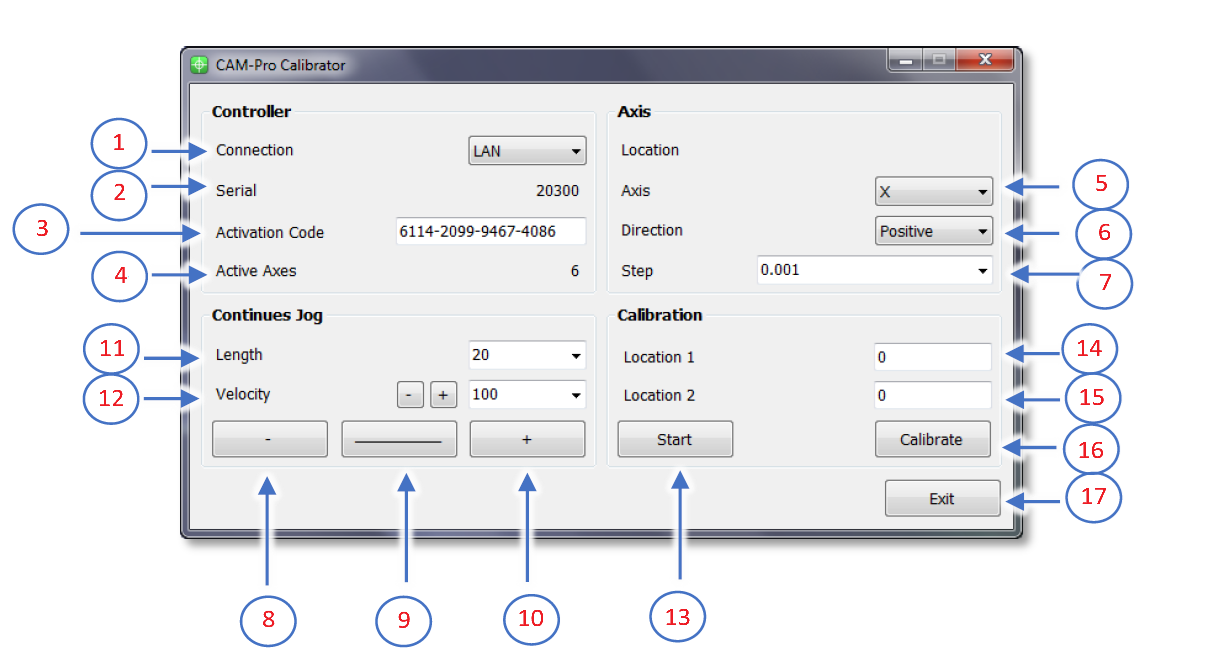
- Connection:
- ProLan kontrolörler LAN mode’a ayarlanmalı.
- ProUSB kontrolörler USB mode’a ayarlanmalı.
- Serial: Kontrol cihazının seri numarasını gösterir.
- Activation Code: Eksenleri aktive etmek için kullanılan 16 haneli kodu gösterir.
- Active Axes: Aktivasyon kodu ile aktif hale gelen eksen sayısını gösterir.
Axis Bölümü
- Axis: Kalibrasyon için istenen ekseni seçmeye yarar. 6. Direction: Standart eksen için uygun hareket yönünü seçer:
- Negative: Negatif yönde hareket.
- Positive: Pozitif yönde hareket.
- Step: Kalibrasyon veya çıkış pulse adımını ayarlar. Kalibrasyon tamamlanınca step değeri ayarlarda otomatik kaydedilir.
Continuous Jog Bölümü
- Negative Jog: Negatif eksen yönünde manuel hareketi etkinleştirir. 9. Jog Mode: Jog hareket tipini seçer:
- Continuous: Kesintisiz, akıcı hareket.
- Incremental: Tanımlı adımlarla hareket.
- Positive Jog: Pozitif eksen yönünde manuel hareketi etkinleştirir.
- Length: Incremental moddayken adım mesafesini tanımlar.
Velocity Bölümü
- Velocity: Manuel hareketlerin hızını ayarlamak için.
- Hız seçeneklerinin yanındaki + ve – butonları, manuel hareket hızını artırır veya azaltır.
Calibration Bölümü
- Start: Kalibrasyon sürecini başlatır. 14. Location 1: Kalibrasyon için ilk konumu ayarlar. Bu konum, ölçülen eksende sabit bir noktaya göre belirlenmelidir. 15. Location 2: Kalibrasyon için ikinci (son) konumu ayarlar. Bu da sabit noktaya göre olmalıdır. 16. Calibrate: Kalibrasyon işlemini tamamlayıp kalibrasyon faktörünü hesaplar. 17. Exit: Kalibrasyon programından çıkar.
Kalibrasyon yazılımı için özet adımlar:
- Axis bölümünden kalibre edilecek ekseni seçin.
- Düşük bir hız seçin ve ekseni hareket ettirerek yönün doğru olduğundan emin olun. Yanlışsa Direction bölümünden düzeltin.
- Ekseni travel aralığının bir ucuna götürün (başlangıç yönü önemli değil).
- Sabit noktaya göre ölçüm yaparak bu konumu Location 1’e kaydedin ve Start tuşuna basın.
- Diğer uca gidin; mümkünse daha uzun mesafeler ölçüm doğruluğunu artırır. İkinci ölçümü Location 2’ye kaydedin.
- Calibrate tuşuna basın; yazılım step değerini hesaplayıp arayüze kaydeder.
- Her eksen için gerektiği kadar tekrarlayın.
- Activation code girilmemişse CAM-Pro Calibrator açıldığında hata mesajı gösterilir.
2) Matematiksel Hesaplama
Hesaplamalı Yöntem
Eksen hareketini istenen birime uyarlamak için “Step” kalibrasyon katsayısı kullanılır. Buna erişmek için yazılımı açıp Ayarlar > System > Axis (1–6 arası eksen) alt dalına gidin. Her eksenin kendine ait Step değişkeni bulunur.
Hareket birimi milimetre ise bu değişkenin birimi pulse başına milimetre, santimetre, inç vb. ise ilgili birim/pulse olur. Bu, her pulse için eksen motor sürücüsüne iletilen hareket miktarını gösterir. Dolayısıyla bu değişkeni hesaplamak için, sürücüye gönderilen pulse başına motor şaftının hareket miktarı ile dişli kutusu, kasnak ve diğer iletim oranlarını bilmek gerekir. Örneklerle açıklayalım:
Örnek 1: Ölçüm birimi milimetre olan bir lineer eksende, 10:1 dişli kutulu Panasonic A5 motor ve efektif çapı 66 mm olan bir pinyon kullanıldığını düşünün. Bu eksenin Step değerini hesaplayın.
Motorun 500.000 pulse/saniye ile 3000 rpm hıza ulaştığını bilerek:
- Adım: Motor hızı saniye başına devir = 3000 rpm / 60 = 50 r/s
- Adım: Motor her turda 66 mm × π / 10 = 20,7339 mm hareket eder
- Adım: 1 pulse başına hareket = (20,7339 mm × 50 r/s) / 500.000 pulse/s = 0,00207339 mm/pulse
Step(mm/pulse) = 50 (r/s) × 20.7339 (mm) / 500000 (pulse/s) = 0.00207339

Bu denklemden Step değeri bulunur; motor her pulse’da 0,0207339 mm hareket eder. Bu yöntem lineer eksen kalibrasyonu içindir.
Örnek 2: Ölçüm birimi derece olan bir döner eksende, 25:1 dişli kutulu Panasonic A5 motor ve 12 dişli kasnaktan 44 dişli kasnağa kayış bağlantısı olduğunu düşünün. Bu eksenin Step değerini hesaplayın.
Motor hızı saniye başı devir = 3000 rpm / 60 = 50 r/s
Step = 50 (r/s) × (1/25) × (12/44) × 360° / 500000 (pulse/s) = 0.000392727272
Denklem:
Step(unit/pulse) = Motor r/s × efektif oran × 360 / pulse/s
Not: Hem lineer hem döner eksenlerinde daha fazla anlamlı basamak kullanmak hesaplama doğruluğunu artırır.
Not: Step motor pulse bölmeleri bu hesaplamaları etkiler; önce pulse başına devir hesaplanıp ardından formüle dahil edilebilir. Not: Maksimum motor hızına ulaşmak için gereken pulse sayısı kontrol cihazının ürettiğinden fazla ise elektronik dişli oranını artırmak gerekebilir (ör. 4 M pulse/s için 500 k pulse/s sağlayan Radonix’te E.G. = 8).
DXF dosyası açıldığında DXF Reader penceresi otomatik açılır ve dosyadaki bileşenleri gösterir.
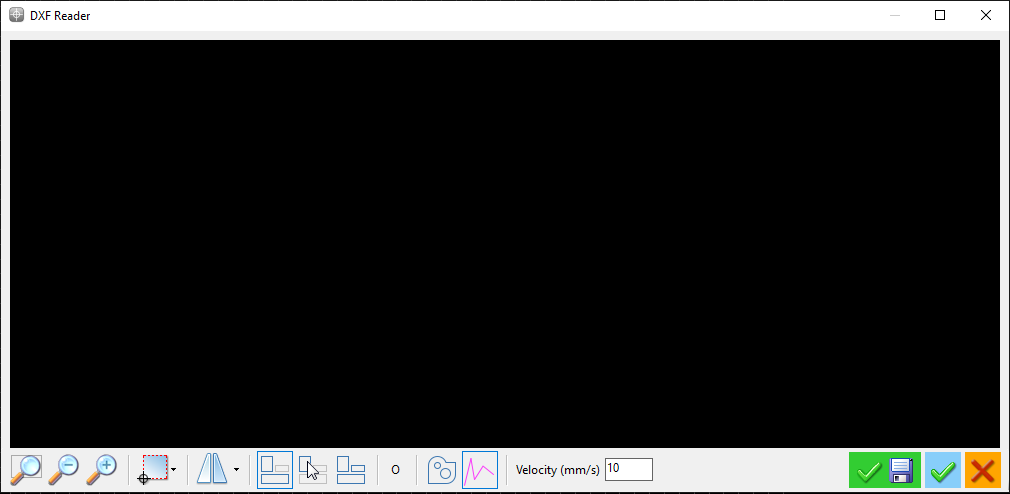
Bu pencerenin altındaki araç çubuğunda:

- Zoom Fit: Açılan tasarımı DXF Reader penceresinde tam görüntüler.

- Zoom Out: Tasarım ölçeğini bir adım küçültür; fare tekerleği yukarı kaydırılarak da yapılabilir.

- Zoom In: Tasarımı bir adım büyütür; fare tekerleği aşağı kaydırılarak da yapılabilir.

- Reference Point (Sıfır) Belirleme: Açılan tasarımda iş parçasının sıfır noktasını belirler; seçenekler:

- Alt sağ köşe (X pozitif sonu, Y negatif sonu).
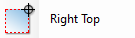
- Üst sağ köşe (X pozitif, Y pozitif).
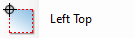
- Üst sol köşe (X negatif, Y pozitif).
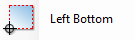
- İlk parça başlangıç noktası.
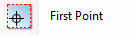
- Rotate/Flip: Tasarıma döndürme veya aynalama uygular:

- 90° saat yönünde döndür.
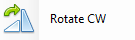
- 90° saat yönünün tersine.
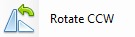
- X ekseninde aynala.
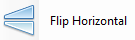
- Y ekseninde aynala.
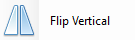
Varsayılan olarak DXF dosyasında parçalar çizim sırasına göre kesilir; çizim yazılımındaki çizgi yönüne göre başlangıç ve bitiş noktaları seçilir. Ancak DXF Reader bölümünde parça kesim sırası ve yönü istenildiği gibi değiştirilebilir. DXF açıldığında tüm parçalar varsayılan olarak çalıştırma için aktiftir ve kesim yönü belirtilir.

Nesneleri Düzenle’ seçeneğine tıklayarak tüm parçalar devre dışı bırakılır. Herhangi bir parçaya sol tıklayınca kesime uygun hale gelir, tekrar tıklayınca devre dışı kalır. Ayrıca parçalara sağ tıklayarak kesim yönünü tersine çevirebilirsiniz. Yürütme sırası önemli olan parçaları seçtiysek, yürütme sırası önemli olmayan geri kalan parçaları ‘Nesneleri Seç’ seçeneğinden seçebiliriz.


‘Varsayılan Düzen’ seçeneği, tasarım yazılımının belirlediği varsayılan sırayla tasarımın yürütülmesini sağlar.
‘Optimize’ seçeneği, dosyanın yürütme süresini en aza indirecek şekilde parça kesim sırasını seçer (kesim sırası, bir parçanın kesimi bittiğinde önceki parçanın bitiş noktasına en yakın başlangıç noktasının seçileceği biçimde düzenlenir).

Bu seçeneğe tıklamak, yalnızca Polilin biçimindeki parçaları kesim için seçer ve bu özelliğe sahip olmayan parçaları devre dışı bırakır.

Şekilde görülen pembe çizgiler, kesim yapmayan veya travers çizgileridir; bu çizgiler, makinenin iki farklı parça arasındaki geçişi sırasında izlediği yolu gösterir. Bu seçeneğe tıklayarak bu çizgilerin görüntülenmesini etkinleştirebilir veya devre dışı bırakabilirsiniz.
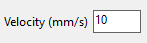
Bu bölüm, parçaların kesim hızını belirler ve birimi milimetre/saniye olarak ayarlanır. Bu hızın yalnızca kesim sırasında makinenin hareket hızını tanımladığını ve tasarım içindeki iki farklı parça arasındaki geçiş hızını etkilemediğini unutmayın.

Yüklü dosya üzerinde yapılan değişiklikleri tamamladıktan sonra, bu seçeneğe tıklayarak orijinal dosyayı koruyarak değişikliklerinizi dosyayı çalıştırmadan önce kaydedebilirsiniz ve gelecekte tasarımı yeniden düzenleme ihtiyacını ortadan kaldırırsınız. Dosyanın .CNC uzantısıyla G-Kod dosyası olarak kaydedildiğini ve sonraki çalıştırmalarda düzenlenemeyeceğini unutmayın.

Bu seçeneğe tıklayarak değişiklikleri kaydetmeden DXF Reader penceresi kapanır ve tasarım yüklenip çalıştırmaya hazır hale gelir.

Bu seçeneğe tıklayarak DXF Reader penceresi tasarımı yüklemeden kapanır.
Farklı kesim makinelerinin ayarlarına dair ipuçları:
CNC Oksijen-Yakıt Kesim Makinesi: Otomatik ateşleme sistemli oksijen-yakıt kesim makinelerinde, gaz çıkışı, ön ısıtmalı hava ve kesim oksijeni için ayrı solenoid vanalar bulunur. Çıkışlar şu şekilde tanımlanır:
➢ C-PreCutPin: Otomatik ateşleme
➢ C-PreCutPin+CutPin: Gaz çıkışı solenoid vanası ve ön ısıtmalı hava vanası
➢ C-CutPin: Kesim oksijeni veya jet solenoid vanası
PreCutTime parametresi, eritilmiş havuz oluşum süresini kontrol etmek için kullanılabilir.
CutTime parametresi, iş parçasını delme süresini kontrol etmek için kullanılabilir.
Kontrol kartı çıkışları tüketiciye maksimum 200 mA akım sağlar; bu miktarın üzerinde akım çekmek çıkışı zarar verebilir. Bu nedenle, 24 V solenoid vana kullanılsaydı bile vanayı doğrudan karta bağlamayın, mutlaka röle kullanın.
Solenoid vanalar ile kesici meme arasındaki mesafe ve ara hortum uzunluğu fazla ise, kesim sonu parçasına zarar gelmemesi için PostCutTime parametresini kullanın. Bu, hortumlardaki gaz tamamen boşalana kadar makinenin duraklamasını sağlar ve iş parçasını korur.
CNC oksijen-yakıt kesim makinelerinde kesim kalitesinin önemli bir kısmı, operatörün alev ayarı ve kesici memenin iş parçasına olan uzaklığını iyi ayarlamasına bağlıdır.
Yardıma mı ihtiyacınız var veya geri bildirim mi iletmek istiyorsunuz?
Radonix’i tercih ettiğiniz için teşekkür ederiz. Memnuniyetiniz önceliğimizdir; ürün ve hizmetlerimizle ilgili her türlü soru, ek bilgi veya geri bildirim için hizmetinizdeyiz. Aşağıdaki iletişim bilgileri üzerinden bize ulaşabilirsiniz:
📍 Adres: HALİL RIFAT PAŞA MAH. YÜZER HAVUZ SK. PERPA TİC MER B BLOK NO: 1 /1İÇ KAPI NO: 1689, ŞİŞLİ/İSTANBUL, TÜRKİYE
📞 Telefon: +90 212 222 9522 +90 553 920 5500
📧 E-posta: İngilizce Destek: [email protected] Türkçe Destek: [email protected]
🌐 Web: radonix.com | radonix.com.tr
Geri bildirimlerinizi bekliyoruz, size yardımcı olmaktan memnuniyet duyarız!
Updated 4 months ago