Uygulamalı Kılavuz
Radonix CNC Kontrol Cihazı için Kurulum ve Ayarlama Süreci
Radonix, bir Radonix CNC kontrol cihazının kurulumu ve yapılandırılması için bu ayrıntılı adım adım kılavuzu takip etmenizi önermektedir. Bu süreç, donanımın kablolanmasından yazılımdaki parametrelerin ayarlanmasına kadar her şeyi kapsar. Bu yaklaşım, müşterilere sorunsuz bir kurulum deneyimi sağlamayı ve tüm kritik bileşenleri ele almayı amaçlar.
Radonix CNC Kontrol Cihazı için Bileşenlerin Kablolanması
Doğru kablolama, güvenilir ve yüksek performanslı bir CNC makinesinin temelidir. Kablolamaya profesyonel bir yaklaşım, Radonix kontrol cihazı, servo veya step motorlar, sensörler, VFD’ler (Değişken Frekanslı Sürücüler) ve diğer çevre birimleri arasında sorunsuz iletişimi sağlar. Bu kılavuz, uygun güç kaynaklarının seçilmesi, güvenliğin sağlanması ve en iyi performansın elde edilmesi dahil olmak üzere tüm bileşenlerin kablolaması hakkında uzman tavsiyesi sunar.
1. Ana Bileşenlere Genel Bakış
Tipik bir CNC sistemi aşağıdaki bileşenleri içerir ve bunların tümü hassas ve güvenli bir şekilde kablolanmalıdır:
- Radonix CNC Kontrol Cihazı: Merkezi kontrol birimi.
- Servo veya Step Motorlar: Eksen hareketlerinden sorumludur.
- Değişken Frekanslı Sürücü (VFD): İş mili motorunu kontrol eder.
- Sensörler:
- Eksen referanslaması için Referans Sensörleri
- Sınır kontrolü için Limit Anahtarları
- Eksen referanslaması için Referans Sensörleri
- Sınır kontrolü için Limit Anahtarları
- Acil Durdurma (E-Stop): Acil durumlarda anında durdurma sağlar.
- Güç Kaynakları: Farklı bileşenlere düzenlenmiş güç sağlar.
- Çevresel Çıkışlar: Röleler, soğutma pompaları ve alarmlar içerir.
2. Ana Güç Kaynağının Kablolanması
Uygun Güç Kaynağını Seçmek
-
Kontrol Cihazı Güç Kaynağı:
Radonix kontrol cihazlarını beslemek için 24V anahtarlamalı güç kaynaklarının kullanılması önerilir. Elektrik panosundaki gerekli güç kaynağı akımını belirlemek için, güç kaynağına bağlı her bir elemanın akım tüketimi hesaplanmalıdır. Örneğin, bir panoda 4 röle, 3 pnömatik solenoid valf ve bir kontrol cihazı varsa, akım tüketimi Ohm Yasası (V=I*R) kullanılarak belirlenebilir. Elektrik akımları hesaplanmalı ve toplamı, birkaç yüzdelik güven faktörüyle birlikte güç kaynağı akımı olarak dikkate alınmalıdır. Örneğin, rölelerin akım tüketimi 0.1A ve solenoid valflerin 0.25A ise, toplam akım şu şekilde hesaplanabilir: Toplam akım = kontrol cihazı akımı + röle akımı + solenoid valf akımı IT = 0.5 + 4 * 0.1 + 3 * 0.25 = 1.65A
3. CNC Kablolama için Parazit Önlemleri
Elektromanyetik girişim (EMI) veya elektriksel parazit, özellikle kontrol cihazları, servo sürücüler ve sensörler gibi hassas bileşenlerin kablolanmasında CNC sistemlerinde yaygın bir sorundur. Parazit sinyalleri bozabilir, makine davranışında düzensizliklere neden olabilir ve zamanla bileşenlere zarar verebilir. Güçlü parazit önleme önlemleri uygulamak, CNC makinenizin güvenilir ve hassas çalışması için kritik öneme sahiptir.
Elektriksel Parazit Kaynakları
- Yüksek Frekanslı Cihazlar:
- Değişken Frekanslı Sürücüler (VFD’ler) - (İlgili Makinelerde)
- Anahtarlamalı güç kaynakları
- Yüksek Güçlü Bileşenler:
- İş mili motorları - (İlgili Makinelerde)
- Servo ve step motorlar
- Uzun Kablolar:
- Daha uzun kablolar anten görevi görerek EMI toplar.
- Güç Hatlarına Yakınlık:
- Sinyal ve güç kablolarının yakın geçmesi parazite neden olabilir.
Temel Parazit Önleme Önlemleri
1. Korumalı Kablolar Kullanın
- Amacı: Korumalı kablolar, hassas sinyaller üzerindeki elektromanyetik girişimin etkisini azaltır.
- Uygulama:
- Pulse+, Pulse-, Direction+, Direction- gibi sinyal hatları ve sensör sinyalleri için bükümlü çift korumalı kablolar kullanın.
- Kalkanı yalnızca bir uçta toprağa bağlayın; bu, toprak döngülerini önler.
2. Sinyal ve Güç Kablolarını Ayırın
- Amacı: Yüksek güçlü kabloların düşük güçlü sinyal kablolarına parazit yaymasını önleyin.
- Uygulama:
- Sinyal kablolarını (örneğin, sensör ve kontrol sinyalleri) güç kablolarından (örneğin, motor gücü ve VFD çıkışı) ayrı güzergahlarla döşeyin.
- Bu kablo türleri arasında en az 10-15 cm mesafe bırakın.
- Güç ve sinyal hatları için farklı kablo kanalları veya borular kullanın.
3. Uygun Topraklama
- Amacı: İyi tasarlanmış bir topraklama sistemi paraziti en aza indirir ve bileşenleri korur.
- Uygulama:
- Elektrik kutusunda merkezi bir topraklama noktası oluşturun, bu genellikle topraklama bara noktası olarak adlandırılır.
- Tüm topraklama kablolarının (kontrol cihazı, sürücüler, motorlar vb.) bu merkezi noktaya bağlandığından emin olun.
- Toprak bağlantılarını zincirleme yapmaktan kaçının, bu parazit oluşturabilir.
4. Ferrit Boncuklar Takın
- Amacı: Ferrit boncuklar sinyal ve güç kabloları üzerindeki yüksek frekanslı paraziti filtreler.
- Uygulama:
- Ferrit boncukları kontrol cihazı veya servo sürücüye yakın sinyal ve kontrol kablolarına takın.
- Özellikle gürültülü ortamlarda birden fazla boncuk kullanın.
5. VFD Kablolamasını Doğru Yapın
- Amacı: VFD’ler önemli bir elektrik paraziti kaynağıdır ve özel dikkat gerektirir.
- Uygulama:
- VFD ile iş mili motoru arasında korumalı kablolar kullanın.
- Kablo kalkanını VFD ucunda toprağa bağlayın.
- VFD giriş ve çıkışına hat filtreleri veya bobinler yerleştirerek paraziti bastırın.
6. Kablo Uzunluklarını Kısaltın
- Amacı: Uzun kablolar daha fazla parazit toplar.
- Uygulama:
- Kablo uzunluklarını mümkün olduğunca kısa tutun.
- Gereksiz gevşeklik veya kablo halkalarından kaçının.
7. İzole Güç Kaynakları Kullanın
- Amacı: Bir sistemdeki parazitin diğerine etki etmesini önleyin.
- Uygulama:
- Sensörler, enkoderler ve kontrol cihazı gibi hassas bileşenler için ayrı ve izole güç kaynakları kullanın.
- Güç kaynaklarının yeterince güçlü ve düzgün şekilde topraklandığından emin olun.
8. Optik İzolasyon Kullanın
- Amacı: Kontrol cihazını dış bağlantılardaki parazitlerden koruyun.
- Uygulama:
- Sensör, röle veya anahtar gibi harici cihazlarla bağlantı için opto-izolatörler kullanın.
- Birçok Radonix kontrol cihazı, giriş ve çıkışlar için dahili optik izolasyona sahiptir.
9. Bağlantıları Güvenceye Alın
- Amacı: Gevşek bağlantılar parazit kaynakları olabilir.
- Uygulama:
- Tüm konnektörlerin sıkı ve güvenli olduğundan emin olun.
- Mümkünse kilitli konnektörler kullanarak kazara bağlantı kopmalarını önleyin.
10. Hat Filtreleri ve Gerilim Koruyucular
- Amacı: Yüksek frekanslı paraziti bastırır ve gerilim dalgalanmalarına karşı koruma sağlar.
- Uygulama:
- AC şebeke beslemesine EMI hat filtreleri takın.
- Kontrol cihazı ve VFD’nin güç girişlerine gerilim koruyucular yerleştirin.
Yazılım Yapılandırması: Sistemi Hayata Geçirme
Adım 1: Radonix Cam Pro’yu Kurun
- Yazılımı bilgisayarınıza indirin ve kurun.
- Kontrol cihazı açıldığında, LAN portundaki LED’leri gözlemleyin: biri sabit yanarken, diğeri yanıp sönmelidir.
- Radonix kontrol cihazını bir LAN veya USB kablosu ile bilgisayara bağlayın.
Adım 2: İlk Ayarlama
- Yazılımı açın ve sistemi başlatın.
- Fabrika ayarlarına sıfırlama yaparak varsayılan ayarların uygulandığından emin olun.
Adım 3: Girişleri Yapılandırın
- Ayarlar > Sistem > Girişler menüsüne gidin.
- Her bir giriş için görev atayın:
EmergencyStop
– Acil Durdurma butonu içinHomePin, X/Y/Z
– Referans sensörleri içinLimitPin, X/-X
– Limit anahtarları için
- Her bir girişi fiziksel olarak etkinleştirip yazılım tepkisini gözlemleyerek test edin.
Adım 4: Çıkışları Yapılandırın
- Ayarlar > Sistem > Çıkışlar menüsüne gidin.
- Her bir çıkış için görev atayın:
C-CutPin
– Kesme başlığını açmaC-ZfreePin,1
– Z eksenini yukarı hareket ettirmek için röleyi aktive etC-ZfreePin,-1
– Z eksenini aşağı hareket ettirmek için röleyi aktive et
- Yazılımda çıkışları tetikleyip bağlı cihazlardaki tepkiyi gözlemleyerek test edin.
Adım 5: Eksen Kalibrasyonu
- Ayarlar > Sistem > Kalibrasyon menüsüne gidin.
- Her eksen için parametreleri girin:
- Adım Başına Birim: Vidalı mil dişi, motor adımları ve enkoder çözünürlüğüne göre belirlenir.
- Maksimum Seyahat: Her eksen için maksimum hareket mesafesini tanımlar.
- Hareket komutu verip gerçek seyahat mesafesini ölçerek kalibrasyonu test edin.
Giriş
Burada, Radonix CNC kontrol cihazlarıyla ilgili olan bir arayüzümüz var. Bu yazılım uygulamasında, giriş ve çıkış bağlantılarıyla ilgili bazı farklı bağlantılar bulunuyor. Bu bölümde, bu giriş ve çıkışlar arasındaki ilişkiyi açıklayan bir metin ve görsel sağlıyorum; bu, uygulamayı daha kolay kurmak ve çalıştırmak için bir akış diyagramı ve algoritma oluşturmada yardımcı olur.
Bu arayüzün adı XYC Simple Glass Cut’tur ve CAM türü olarak SimpleCAM veya S-CAM olarak adlandırılır.
Fotoğrafta adı belirtilmiş ve işaretlenmiş arayüzün farklı bölümlerini inceleyin; bu, düğmeler, ekran, çubuklar, hacim, değerler gibi tüm öğelere aşina olmanız gerektiği anlamına gelir – yani arayüzde erişiminiz olan her şeye.
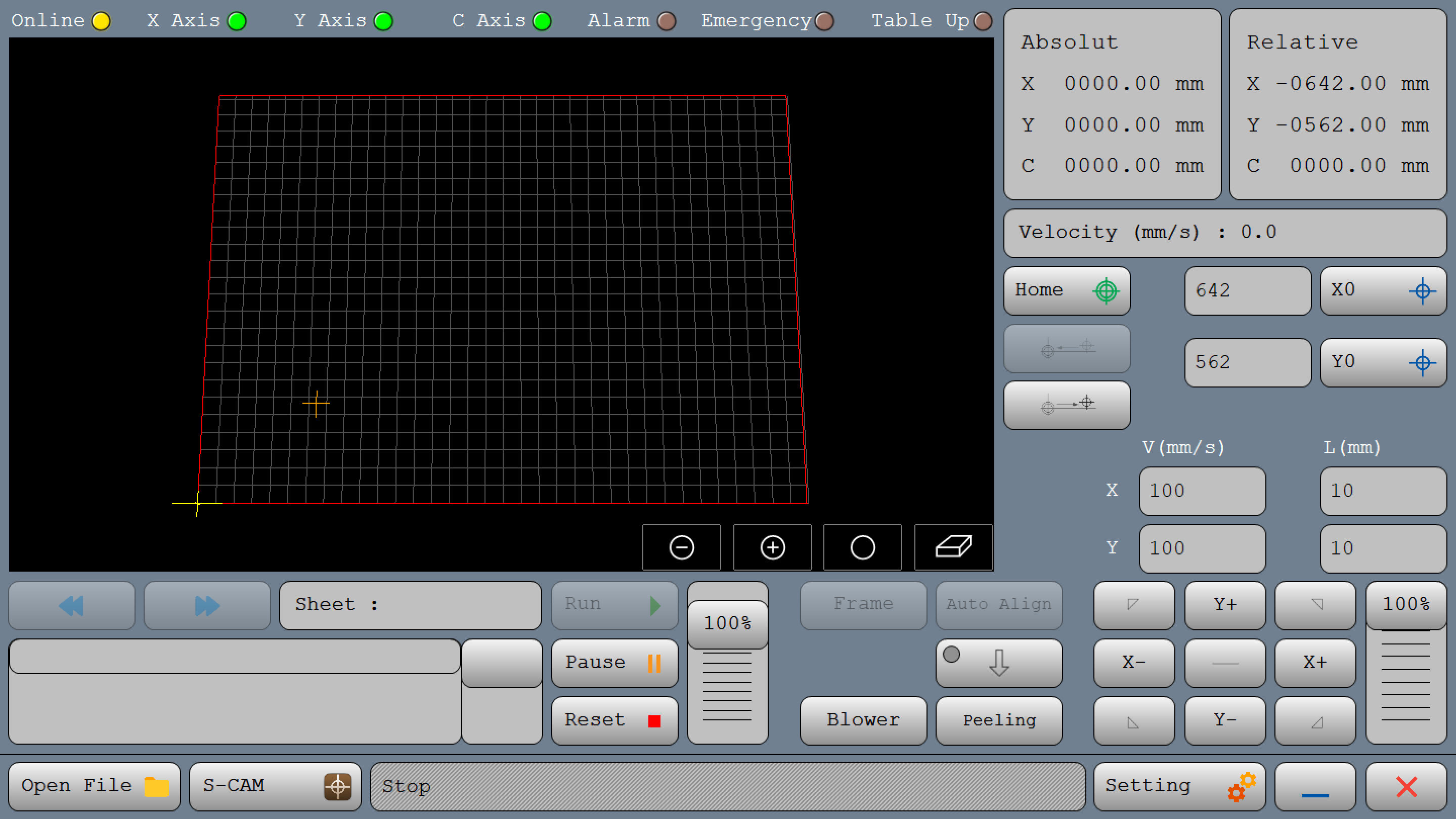
XYC Simple Glass Cut
İlk kurulumun başlatılması için takip edilmesi gereken bazı adımlar vardır ve bunlar başarılı bir kurulum için gereklidir.
Başlangıç
Çalışma Alanı Açıklamaları
İşte bu CNC kontrol arayüzündeki her bölüm ve düğmenin ayrıntılı açıklaması
Üst Durum Çubuğu

- Çevrimiçi (Sarı Işık): Makinenin bağlantı durumunu gösterir. Sarı, bekleme modu veya tamamen çevrimiçi olmadığını gösterebilir.
- X Ekseni, Y Ekseni, C Ekseni (Yeşil Işıklar): Bu ışıklar her eksenin çalışma durumunu gösterir. Yeşil genellikle eksenin aktif veya hazır olduğu anlamına gelir.
- Alarm, Acil Durum, Tabla Yukarı (Kahverengi Işıklar): Kritik güvenlik durumları için göstergelerdir. Etkinleştirildiğinde renk değiştirebilirler (örneğin kırmızı) ve bu bir alarmı, acil durdurmayı veya tabla konumlandırma sorununu gösterir.
Pozisyon ve Hız Göstergeleri (Sağ Panel)
- Mutlak Konum (Sağ Üst Kutucuk):
Mutlak: Eksenlerin koordinatlarını sıfır (home) noktasına göre gösterir.
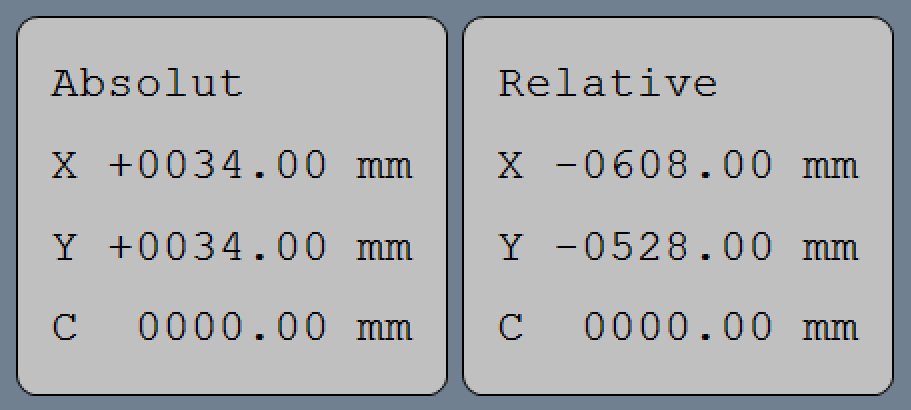
- Göreceli Konum (Mutlak Konumun Yanı):
Göreceli: Eksenlerin koordinatlarını referans noktasına göre gösterir.
- Hız (Göreceli Konumun Altında): Anlık çalışma hızını mm/s olarak gösterir; gerçek zamanlı kesim veya hareket hızlarını izlemek için kullanışlıdır.

Pozisyon Kontrolleri (Orta Sağ Panel)
-
Home (Hedef İkonu): Makineyi başlangıç veya sıfır konumuna götürür.
-
X0 ve Y0 (Nişangah İkonları): Bu düğmeler iş miliyi X ve Y koordinatlarında sıfır noktasına götürür veya aracı eksenin sıfır noktasına taşır.
-
Referans noktalarını kaydetmek için iki seçeneğiniz vardır. İlk seçenek, aracı manuel olarak jog tuşları ile hareket ettirip istenilen noktaya ulaştığınızda ilgili düğmeye basarak bu konumu eksen için kaydetmektir. İkinci seçenek ise her düğmenin önündeki giriş kutusuna kesin konum değerini doğrudan girmektir.
Manuel Jog Kontrolleri
- Oklar (X+, X-, Y+, Y-): Bu düğmeler aracı X ve Y eksenlerinde manuel olarak hareket ettirir, alet kafasının hassas konumlandırması için kademeli hareket sağlar.
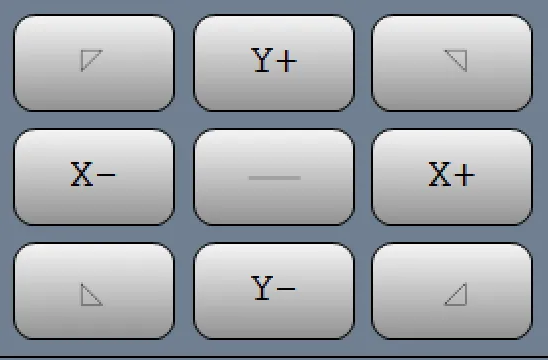
- Jog modunu bu düğmeye basarak şekildeki 01-05’e göre değiştirebilirsiniz ve bu, 01-06 şekline geçerek sürekli hareketten kademeli harekete dönüşür. Bu, kırmızı alanla gösterilen şekilde 01-07’ye göre bu bölümde bir değer tanımlayabileceğiniz anlamına gelir ve eksen jog düğmesine bastığınızda, eksen girdiğiniz miktar kadar hareket eder.
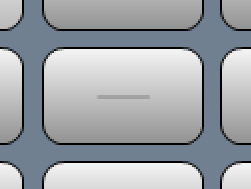
Şekil 01-05
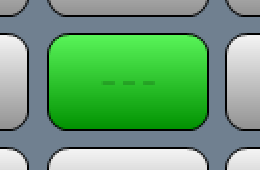
Şekil 01-06
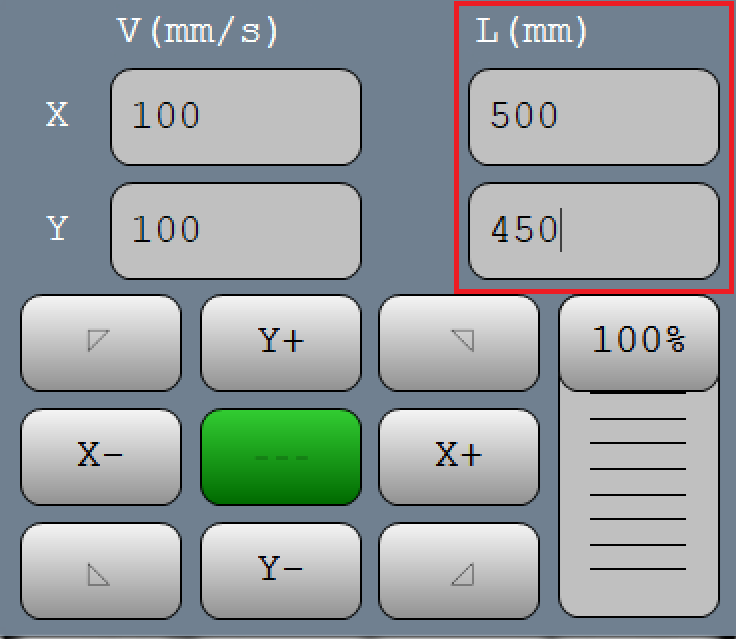
Şekil 01-07
İlerleme Hızı ve Takım Parametreleri (Alt Sağ Panel)
-
V (mm/s) ve L (mm): Her eksende ilerleme hızı ve hareket sınırlarını ayarlamak için giriş alanlarıdır. "V", mm/s cinsinden hızı kontrol ederken, "L" her manuel jog adımı için adım büyüklüğünü tanımlar.
-
Kaydırma Çubuğu (Alt Sağdaki Dikey Sürgü): Şekil 01-08’de kırmızı alanla işaretlenmiş şekilde, ilerleme hızı veya hızı yüzde olarak gerçek zamanlı ayarlamayı sağlar. Bu kontrol, program değerlerini doğrudan değiştirmeden hızı hızlıca ayarlamanıza olanak tanır.
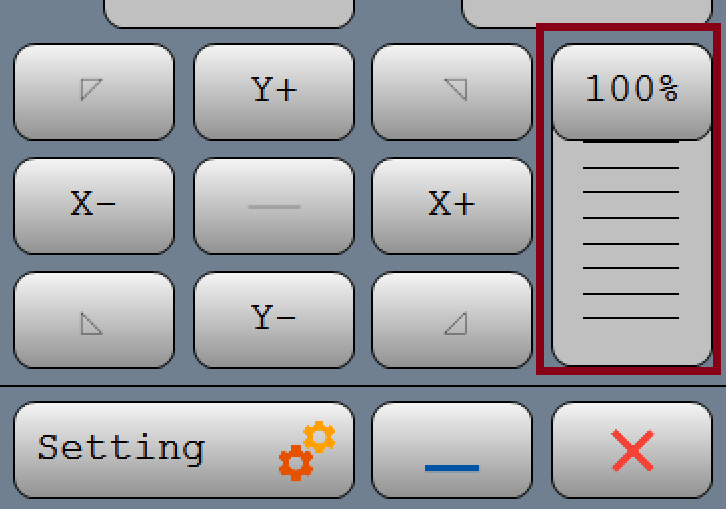
Ana Program Kontrolleri
- Ayarlar (Dişli İkonu): CNC makinesi için ayrıntılı ayarların yapılandırılabildiği ayar menüsünü açar.

- Çıkış ikonu programı kapatmanızı sağlar.
- Eksi simgesi, programı küçültmenizi sağlar.
Arayüz özellikleri:

Bu arayüz bölümü, sistemin mevcut durumunu ve özelliklerini gösterir. Ayrıca her saniye alarmlar ve işlemleri günceller. Ayrıntılı bir rapor için bu bölüme çift tıklayın.
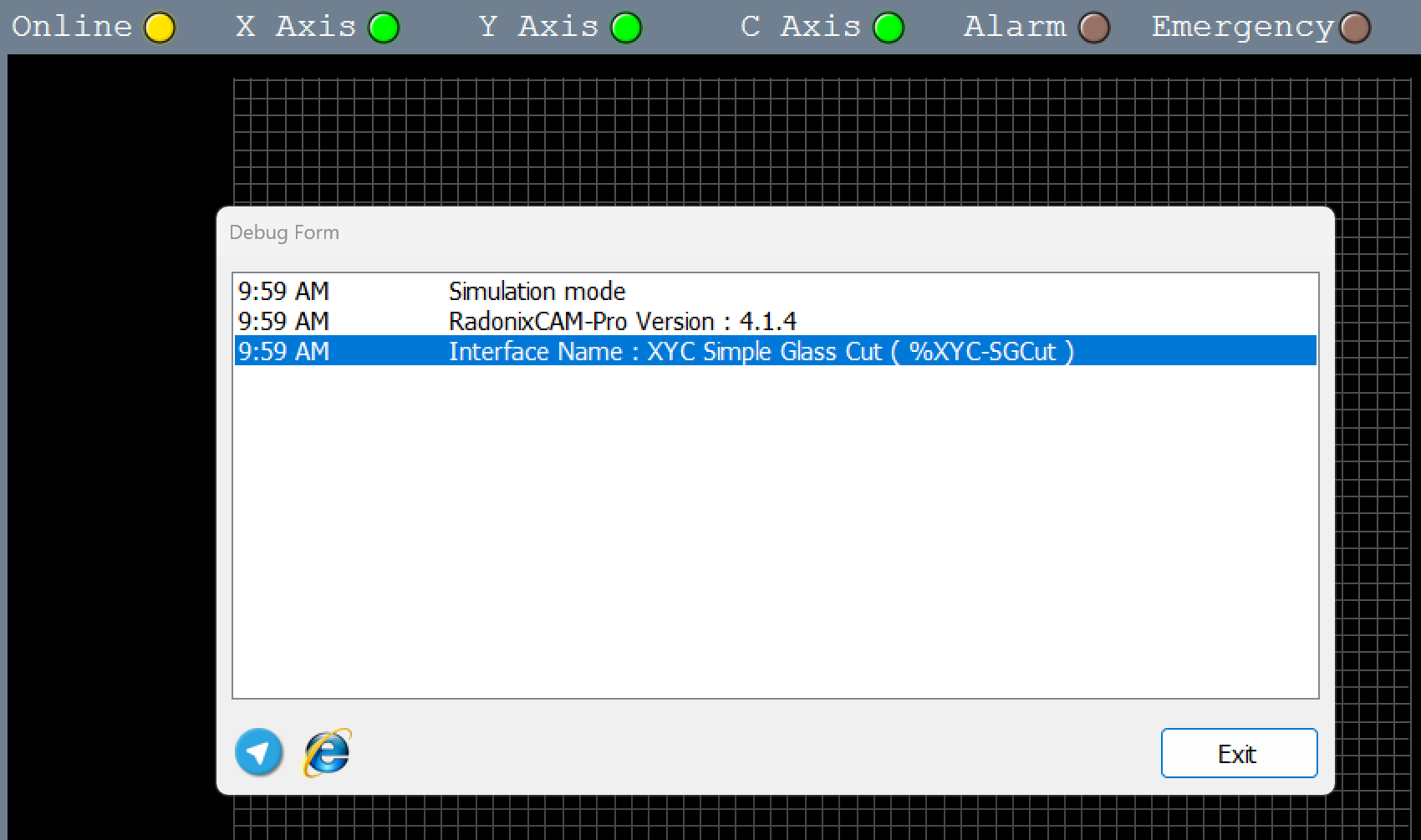
Bu görüntüde arayüz @simülasyon modunda gösterilmiştir
Ana Program Kontrolleri (Alt Merkez)
- Dosya Aç (Klasör İkonu): CAM (Bilgisayar Destekli İmalat) dosyasını yüklemek için bir dosya penceresi açar, genellikle G-code veya DXF programı.
- S-CAM: Belirli bir CAM yazılım arayüzünü açabilir veya işleme işini yapılandırmak için ilgili seçenekleri gösterebilir.
Özel Fonksiyonlar (Alt Sağ Düğmeler)
- Çerçeve (Gri, Muhtemelen Devre Dışı): Kesim alanını çerçeveler veya gösterir, aracın izleyeceği yolu çizer.
- Otomatik Hizalama (Gri, Muhtemelen Devre Dışı): Cam levhayı tasarımınıza göre otomatik olarak hizalayabilir.
- Hava Üfleyici: Cam levhaların hareketini kolaylaştırmak için hava üfleyiciyi etkinleştirir.
- Soyma: İşlem öncesi malzeme yüzeyindeki koruyucu kaplamayı (örneğin kâğıt) çıkarmak için soyma işlevini etkinleştirebilir.
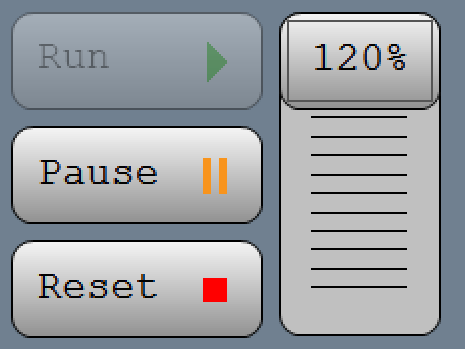
Bu bölüm G-Code yürütmesini kontrol etmeye adanmıştır:
- Çalıştır: Bu düğme G-Code işlemini başlatır.
- Duraklat: Bu düğme takım yolunu duraklatır.
- Sıfırla: Bu düğme takım yolunu sıfırlar.
Ekran ve Yakınlaştırma Kontrolleri (Ana Ekranın Ortası)
- Izgara Görünümü (Izgaralı Siyah Alan): Çalışma alanını ve takım yolu görselleştirmesini gösterir. Izgara, takım ve iş parçasının göreli konumunu görselleştirmeye yardımcı olur.
- Yakınlaştırma ve Kaydırma Kontrolleri:
- + ve - Düğmeleri: Görüntüye yakınlaştırma ve uzaklaştırma yapar.
- El İkonu: Izgara üzerinde gezinmeyi sağlar.
- Diğer Simgeler (Izgaranın Sağ Altı): Tam ekran veya farklı yakınlaştırma ön ayarları gibi ek görüntüleme veya ekran ayarlarını kontrol edebilir.
Cam Dalı
Yükleyici Aşağı Gecikmeleri
Bu parametre, cam levhaların bir yüzeye veya yeni bir konuma tekrar bırakılması sırasında nasıl yerleştirileceğini yönetmek açısından kritik öneme sahiptir. "Yükleyici Aşağı Gecikmesi", camın indirilme veya yerleştirme aşamasında benzer bir amaçla kullanılır.
Yükleyici Aşağı Gecikmesini Anlamak
1. Yükleyici Aşağı Gecikmesinin Amacı:
- Kontrollü İniş: Bu gecikme, camın nazik ve hassas bir şekilde yerleştirilmesini sağlamak için indirme hızını ve zamanlamasını düzenler. Camın aniden düşmesini önler ve kırılmasını engeller.
- Stabilizasyon: Makine ve camın son yerleştirme öncesi stabilize olmasına olanak tanır, böylece cam, operasyonel gerekliliklere uygun olarak mükemmel şekilde hizalanır.
2. Uygulama ve Faydalar:
- Gelişmiş Güvenlik: İnişi kontrol ederek hem camın hem de makinenin zarar görme riskini azaltır, operasyonel güvenliği artırır.
- Geliştirilmiş Hassasiyet: Kritik anlarda yavaşlama, konumlandırma doğruluğunu artırır; bu özellikle karmaşık montajlar veya hassas cam türleri için önemlidir.
- Operasyonel Verimlilik: Gecikme ilk bakışta süreci yavaşlatıyor gibi görünse de, hataların ve cam değişimi gereksinimlerinin azaltılması sayesinde genel verimliliği artırır.
Yükleyici Yukarı Gecikmeleri
Cam Levha Taşımada Yükleyici Yukarı Gecikmeleri
"Yükleyici Yukarı Gecikmeleri" terimi, CNC makinelerinin kesim veya işlem için kullanıldığı ortamlarda cam levhaları taşımak üzere kullanılan mekanik yükleyicilerin zamanlı hareketlerini ifade eder. Bu yükleyiciler hidrolik veya pnömatik olabilir ve her biri kendine özgü özelliklere ve operasyonel gereksinimlere sahiptir.
Hidrolik Yükleyiciler:
- İşlevsellik: Hidrolik sistemler, ağır cam levhaları kaldırmak ve taşımak için sıvı basıncını kullanır. Pürüzsüz ve güçlü çalışmaları ile bilinirler.
- Gecikme Önemi: Hidrolik sistemlerdeki gecikmeler, sıvı basıncının gerekli seviyeye ulaşması sürecinde ortaya çıkar. Bu gecikmeler, hareketin yumuşak başlamasını ve camın ani sarsıntılarla zarar görmeden taşınmasını sağlamak açısından kritiktir.
Pnömatik Yükleyiciler:
- İşlevsellik: Pnömatik yükleyiciler hava basıncı ile çalışır. Genellikle hidrolik sistemlerden daha hızlıdırlar ancak aynı kuvvet seviyesini sağlayamayabilirler.
- Gecikme Önemi: Pnömatik sistemlerde, hava basıncının hızlı yükselişine tepkiyi kontrol etmek için gecikmeler kullanılabilir. Bu, cam levhaların ani sarsıntılardan zarar görmesini önler.
Operasyonel Dikkat Edilmesi Gerekenler:
- Güvenlik: Gecikmeler, hareket başlamadan önce yükün güvenli bir şekilde tutulmasını sağlamak için programlanır, böylece kayma veya yanlış hizalanma önlenir.
- Verimlilik: Doğru zamanlanmış gecikmeler, yükleme/boşaltma işleminin verimliliğine katkı sağlar, geçişlerin sorunsuz olmasını ve cam hasarlarının veya mekanik arızaların azaltılmasını sağlar.
Modeller Arası Uyarlanabilirlik:
- Farklı yükleyici modelleri – ister hidrolik, ister pnömatik ya da başka türler – bu gecikmeler için makine tasarımı, cam levha ağırlığı ve operasyonel gerekliliklere bağlı olarak değişen ayarlara sahip olabilir.
Hassasiyetin ve güvenliğin ön planda olduğu endüstriyel ortamlarda, bu "Yükleyici Yukarı Gecikmeleri"nin doğru şekilde anlaşılması ve ayarlanması kritik öneme sahiptir. Bu gecikmeler, makinelerin güvenli sınırlar içinde çalışmasını, verimliliğin korunmasını ve taşınan malzemenin korunmasını sağlar. Gecikme sürelerinin dikkatli bir şekilde dengelenmesi, genel iş akışını optimize eder ve hem mekanik yükleyicilerin hem de taşınan cam malzemenin ömrünü uzatır.
Yoğun hareket içeren yükleyicilerle cam taşınmasında, "Yükleyici Yukarı Gecikmeleri" için çift parametreye sahip olmak özellikle önemlidir. Bu parametreler, yükleyicinin hızlı ve güçlü hareketlerinin neden olduğu riskleri yönetmek ve azaltmak üzere özel olarak tasarlanmıştır ve operasyon sırasında hem güvenliği hem de hassasiyeti sağlar.
Yoğun Hareketlerin Yönetilmesinin Önemi
1. Mekanik Gerilimi Azaltmak:
- Gerekçe: Yoğun hareketler, hem cam hem de makine üzerinde ciddi mekanik gerilim oluşturabilir. Stratejik gecikmeler uygulayarak bu gerilimler kontrol altına alınabilir ve mekanik arıza veya cam hasarı riski azaltılabilir.
- Uygulama: İlk gecikme cam kaldırıldığında başlangıç darbesini azaltmak için kullanılabilirken, ikinci gecikme cam işleme noktasına yerleştirilmeden hemen önce kritik olabilir.
2. Hassasiyet ve Güvenliği Artırmak:
- Hassasiyet: Gecikmeler, camın yerleştirilmesinde ince ayar yapılmasına yardımcı olur, bu da özellikle kesim veya gravür gibi işlemlerde ürün kalitesini doğrudan etkiler.
- Güvenlik: Kritik anlarda yükleyici hareketlerinin yavaşlatılması, camın çok ani taşınmasından kaynaklanan kazaları önler, böylece hem operatörleri hem de malzemeyi korur.
3. Operasyonel Verimliliği Korumak:
- Verimlilik: İlk bakışta ters gibi görünse de, bu gecikmelerin entegrasyonu, hatalar veya hasarlar nedeniyle oluşabilecek duraklamaları azaltarak genel işlem hızını artırabilir.
CNC Cam Kesme Masası için Belirli Giriş ve Çıkışlarla Kriko Hareket Algoritması
Amaç: Vakum başlıklı krikoların cam levhayı kesim için güvenli bir şekilde konumlandırmasını otomatikleştirmek.
Sistem Girişleri:
GlassDimensions
: Camın uzunluk ve genişliği.DesiredPosition
: CNC tablası üzerindeki hedef konum koordinatları.
Kontrol Pinleri ve Sensör Girişleri:
-
Girişler:
G-LoaderDownSensor1Pin
veG-LoaderDownSensor2Pin
– Krikoların en alt konumunu algılayan sensörler.G-LoaderUpSensorPin
– Krikoların en üst konumunu algılayan sensör.
-
Çıkışlar:
G-LoaderUp1Pin
veG-LoaderUp2Pin
– Krikoları yukarı kaldırmak için etkinleştirilir.G-LoaderDown1Pin
veG-LoaderDown2Pin
– Krikoları aşağı indirmek için etkinleştirilir.
Algoritma Adımları:
-
Başlangıç Durumunu Kontrol Et:
G-LoaderUpSensorPin
,G-LoaderDownSensor1Pin
veG-LoaderDownSensor2Pin
pinlerinden başlangıç durumu okunarak krikoların doğru başlangıç konumunda olduğundan emin olun.
-
Vakumu Aktifleştir ve Krikoları Kaldır:
G-LoaderUp1Pin
veG-LoaderUp2Pin
pinlerine sinyal gönderilerek krikoların yukarı kaldırılması başlatılır.- Krikoların üst konuma ulaştığını doğrulamak için
G-LoaderUpSensorPin
izlenir.
-
Camı Konumlandır:
- Krikolar kaldırıldıktan sonra, kontrol sistemiyle
DesiredPosition
konumuna hareket ettirilir. GlassDimensions
kesim alanı ile doğru hizalandığından emin olun.
- Krikolar kaldırıldıktan sonra, kontrol sistemiyle
-
Camı Yerleştirmek için Krikoları İndir:
G-LoaderDown1Pin
veG-LoaderDown2Pin
etkinleştirilerek krikolar aşağı indirilir.G-LoaderDownSensor1Pin
veG-LoaderDownSensor2Pin
sürekli izlenerek kontrollü ve güvenli bir iniş sağlanır.
-
Yerleşimi Doğrula ve Vakumu Bırak:
- Konumlandırma tamamlandığında vakum başlıkları devre dışı bırakılır ve sensörlerle yerleştirme doğrulanır.
- Tüm krikoların tamamen indiğinden ve camın güvenli şekilde yerleştirildiğinden emin olun.
-
Ayarlamalar için Geri Besleme Döngüsü:
- Sensörler yanlış hizalama veya yerleştirme algılarsa, krikolar ayarlanır.
- Mükemmel hizalama sağlanana kadar kaldırma veya indirme işlemi tekrarlanır.
-
Son Güvenlik Kontrolü:
- Camın kesime hazır olduğundan emin olmak için tüm sensörlerle son kontrol yapılır.
- Yerleştirme güvenlik parametreleri dışında ise işlem durumu ve uyarılar kaydedilir.
Hata Yönetimi:
G-LoaderDownSensor1Pin
veG-LoaderDownSensor2Pin
'den gelen geri bildirimlere dayalı hata tepkileri uygulayın.- Bir arıza durumunda, alanı güvenli bir şekilde boşaltmak için
G-LoaderUp1Pin
veG-LoaderUp2Pin
kullanarak krikoları kaldırın.
Bu senaryo, her bir pin ve sensörün bir CNC kesim tablası üzerindeki camın hassas ve güvenli şekilde taşınmasına nasıl katkıda bulunduğunu ayrıntılı olarak gösterir. Krikoların fiziksel hareketlerinin belirli kontrol ve sensör pinlerine bağlanması sayesinde operatörler, yüksek düzeyde otomasyon ve güvenliği sağlayabilir, kesim sürecini optimize eder ve cam hasarı riskini en aza indirir.
Analog Değer
CNC cam kesme makinelerinde, cam yüzeyine uygulanan basıncın kontrolü, çatlakların veya kırıkların önlenmesi ve hassas kesimlerin sağlanması açısından kritik öneme sahiptir. 'Analog Max Value' ve 'Analog Min Value' parametreleri bu sürecin ayrılmaz bir parçasıdır:
- Analog Max Value:
- Bu ayar, CNC makinesinin cam yüzeyine uygulayabileceği maksimum basınç sınırını tanımlar. Malzemeye zarar verebilecek aşırı kuvveti önlemek için bir güvenlik eşiği olarak işlev görür.
- Analog Min Value:
- Buna karşılık, bu parametre etkili bir kesim gerçekleştirmek için gerekli olan minimum basınç seviyesini belirler. Aletin camla yeterli temas kurmasını sağlar ve temiz, kontrollü bir kesim hareketine olanak tanır.
S-CAM’in Basınç Ayarı Özelliği ile Gelişmiş Operasyonel Kontrol ve Güvenlik
S-CAM, operatörlerin istedikleri basınç ayarlarını doğrudan sisteme girmelerine olanak tanıyan yenilikçi bir özelliğe sahiptir. Bu giriş daha sonra makinenin operasyonel parametrelerine entegre edilir ve malzeme taşıma ile takım temasında özelleştirilmiş bir yaklaşım sağlar:
- Operatör Girişi ile Basınç Ayarları:
- Operatörler, kontrol arayüzü aracılığıyla istedikleri basınç seviyelerini doğrudan ayarlayabilir. Bu giriş, işlenen malzemenin özel ihtiyaçlarına göre makine performansını uyarlamak için kritiktir.
- Levha Ayarlarına Entegrasyon:
- Bu basınç değerleri girildiğinde, makinenin levha ayarlarına entegre edilir. Bu entegrasyon, kesim veya işleme döngüsü boyunca makinenin tutarlı ve optimal basınç uygulamasını sağlar, operasyonun hassasiyetini ve nihai ürünün kalitesini artırır.
- Güvenlik ve Kolaylık:
- Operatörlerin basınç ayarlarını belirlemesine olanak tanıyarak S-CAM, manuel hata ve malzeme zararları riskini en aza indirir. Bu özellik yalnızca işlemi daha pratik hale getirmekle kalmaz, aynı zamanda uygunsuz basınç seviyelerinden kaynaklanan kazaların olasılığını azaltarak güvenliği önemli ölçüde artırır.
Bu parametre ayar yeteneği, malzeme özelliklerinin geniş ölçüde değişiklik gösterdiği ortamlarda özellikle etkilidir ve optimal işleme sağlamak için makine ayarlarında sık sık ayarlamalar yapılmasını gerektirir. Operatör girişine göre basınç ayarlarının hızlı ve doğru bir şekilde değiştirilebilmesi, yüksek operasyonel standartları ve uyarlanabilirliği korumaya yardımcı olur.
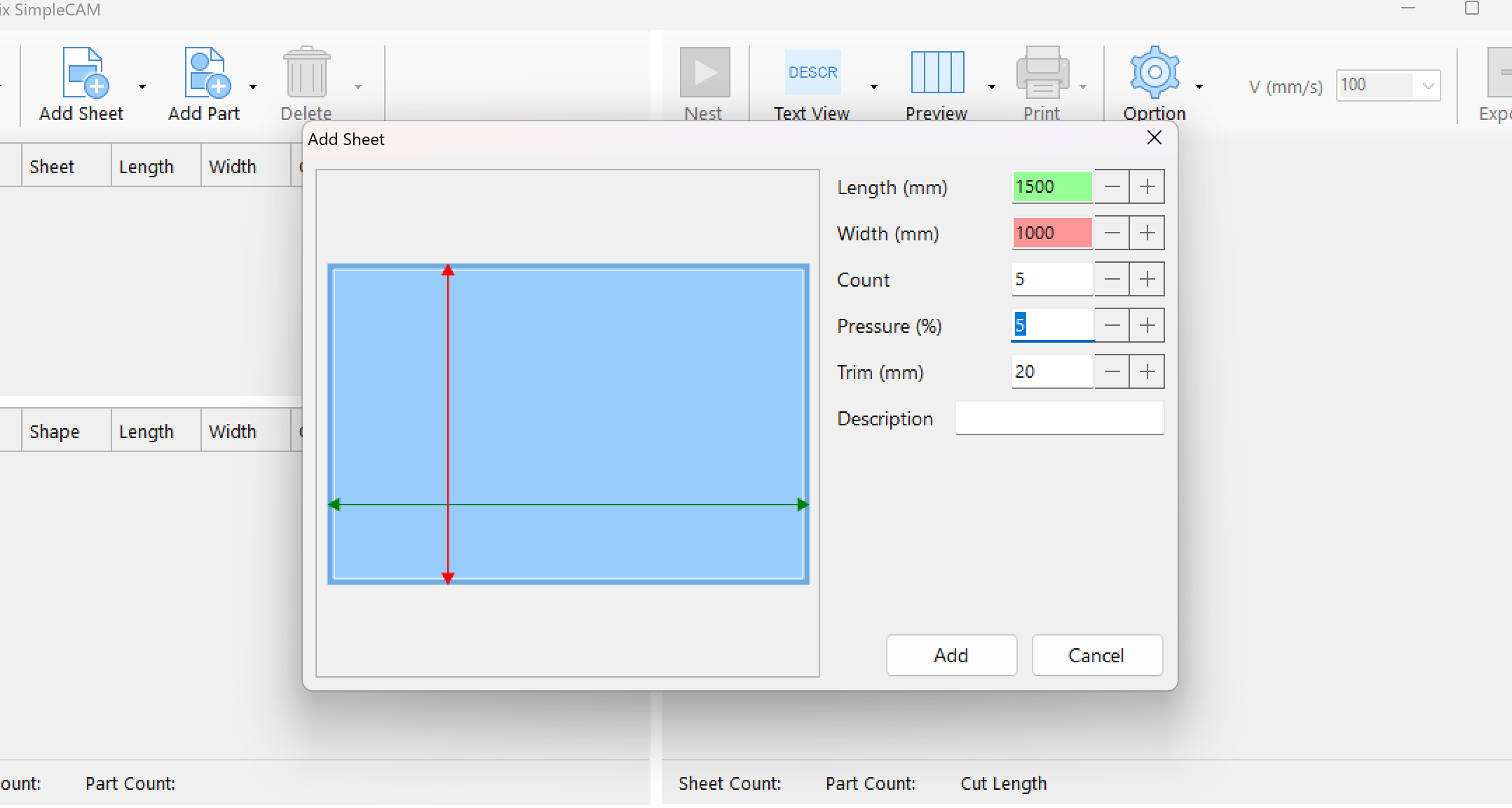
Bu ayarlar, değişken basınç yetenekleriyle donatılmış makinelerde özellikle önemlidir ve operatörlerin kesim sürecini işlenen camın kalınlığına veya türüne göre ince ayarlamalar yapmasına olanak tanır. Bu değerleri ayarlayarak, CNC kontrol cihazı kesim kalitesini ve verimliliğini optimize etmek için kesim basıncını gerçek zamanlı olarak dinamik biçimde değiştirebilirken camın bütünlüğünü de korur.
One Stage Aligned Enabled
Kare ve Lazer Sensörü ile One Stage Align Parametresi Kullanılarak CNC Hizalama
Amaç:
- Bir kenar için fiziksel bir kare ve diğer kenar için lazer sensörü kullanarak CNC tablası üzerinde nesnelerin hassas hizalamasını sağlamak.
Süreç Genel Görünümü:
- İlk Kurulum:
- Nesneyi (örneğin cam levha) CNC tablası üzerine yerleştirin.
- Nesnenin bir kenarını, tabloya sabitlenmiş bir kare veya düz kenarla manuel olarak hizalayın. Bu kenar, güvenilir ve tutarlı bir referans noktası olarak hizmet eder.
- Lazer Sensör Hizalaması:
- Nesnenin karşı tarafını hizalamak için lazer sensör kullanın. Sensör, bu kenarın makinenin koordinatlarına göre tam konumunu algılar.
- Lazer hizalamasını algılanan konuma göre ayarlamak için CNC kontrollerini kullanın. Bu, nesnenin tamamen paralel ve doğru şekilde hizalanmasını sağlar.
- One Stage Align Parametresinin Etkinleştirilmesi:
- Manuel ve lazer hizalamaları ayarlandıktan sonra, One Stage Align Parametresini etkinleştirin. Bu parametre, kareden gelen sabit hizalamayı ve lazer sensöründen gelen hassas konumlandırmayı dikkate alır.
- Bu hibrit yaklaşım, hizalama hatalarını en aza indirir ve nesnenin işlenmesinin hem doğru hem de verimli olmasını sağlar.
- İşleme Başlangıcı:
- Nesne sabitlendikten ve düzgün hizalandıktan sonra CNC makinesi kesme veya kazıma işlemine başlayabilir. Manuel ve lazer destekli hizalamanın birleşimi, işlemin en yüksek doğruluk seviyesinde yürütülmesini sağlar.
Pedal
CNC tablası üzerinde cam levhaların otomatik veya manuel yöntemlerle hizalanması sürecini ve sapmalara göre ayarlamaları açıklığa kavuşturmak için, otomatik hizalama özelliği, köşe krikoları veya sabit kareler ve hizalama pedalı gibi farklı hizalama mekanizmalarının nasıl çalıştığına dair yapılandırılmış bir genel bakış aşağıda sunulmuştur:
CNC Tablasında Cam Levha Hizalama Süreci
İlk Kurulum:
- Levha Yerleştirme: Cam levha CNC tablasına otomatik veya manuel olarak yerleştirilebilir. Bu ilk yerleştirme bazı sapmalara sahip olabilir.
- Sapma Ayarı: Levhanın konumunda bir sapma varsa, kesim işlemine başlamadan önce onu doğru şekilde ayarlamak ve hizalamak için bazı mekanizmalar mevcuttur.
Hizalama Modları:
- Tam Otomatik Lazer ile:
- Lazer sistemi, cam levhayı tarayarak tam konumunu ve yönünü algılar.
- Camın konumunu otomatik olarak ayarlayarak kesim için hassas hizalama sağlar.
- Köşe Krikosu veya Sabit Kare Modu:
- Tablanın altından çıkabilen köşe krikoları veya sabit kareler gibi mekanik hizalama bileşenlerini kullanır.
- Hizalama pedalı, bu mekanik hizalama elemanlarının kontrolünde kritik bir rol oynar.
Hizalama Pedalı İşlevleri:
- Birinci Basış: Köşe krikosunu veya sabit kareyi etkinleştirir. Bu, mekanik hizalayıcının levhayı önceden tanımlanmış bir nokta veya kenara doğru ayarlamak için yükseldiği ilk adımdır.
- İkinci Basış (Tanımlanabilir Zaman Gecikmesi ile): Üfleyiciyi açar. Üfleyici, cam levhanın hareketini kolaylaştırır, böylece operatörlerin levhayı elle uygun konuma ayarlaması daha rahat hale gelir.
- Üçüncü Basış: Cam istenen konuma ulaştıktan sonra, üçüncü pedal basışı köşe krikosunun geri çekilmesini sağlar ve üfleyici kapanır, böylece cam işleme için sabitlenmiş olur.
İşlem Sıralaması:
- Aktivasyon: Operatörler hizalama işlemini pedal ile başlatır, basış sayısına ve her basışa atanan işleve göre ayarlamalar yapılır.
- Ayarlama ve Sonlandırma: Pedalın sıralı kullanımı, köşe krikoları veya sabit kareler ve üfleyici ile birlikte, cam levhanın hassas şekilde konumlandırılmasına yardımcı olur. Hizalama tamamlandıktan sonra, kesim işlemleri cam güvenli ve doğru konumda olacak şekilde devam edebilir.
Bu sistem, hizalama kaynaklı hataların olasılığını azaltarak yüksek doğruluk ve kullanım kolaylığı sağlar ve CNC tablalarında cam kesim işlemlerinin genel verimliliğini artırır. Mekanik ve otomatik hizalama özelliklerinin entegrasyonu, farklı operasyonel ihtiyaçlara ve cam levha özelliklerine uyum sağlamak için esneklik sunar.
ZAxis Delay
CNC Cam Kesme Makinelerinde Z Ekseni İçin Zaman Tabanlı Kontrolün Uygulanması
CNC cam kesme makinelerinin çalışmasında, kesici takımın dikey hareketini yöneten Z ekseninin hassas kontrolü kritik öneme sahiptir. Z ekseni hareketi için zaman tabanlı bir kontrol sistemi, cam kalınlıklarındaki değişkenliğe karşı makinenin uyum yeteneğini artırmak amacıyla geliştirilmiştir.
CNC cam kesme makinelerinde ZAxisDelay
parametresi, Z ekseni krikosunun cam levhanın yüzeyine inmesi ve ulaşması için gereken süreyi yönetmek açısından çok önemlidir. Bu parametre, özellikle camın hassas doğası göz önünde bulundurularak, kesim işleminin doğruluğunu sağlamak için gereklidir.
Arama Hızı (Search Velocity)
Otomatik Hizalamada Lazer Arama Hızı
Genel Bakış: CNC cam kesme işlemlerinde, özellikle otomatik hizalama aşamasında, lazerin cam üzerinde hizalama noktalarını arama hızı kritik öneme sahiptir. Bu parametre — ZAxisDelay
'den farklı olarak — lazer tarama mekanizmasının hızını kontrol etmek için özel olarak tasarlanmıştır.
İşlevsellik:
- Amacı: Bu hız kontrol parametresinin temel amacı, lazerin arama aşamasındaki hızını optimize etmektir. Bu, lazerin cam levhanın tüm yüzeyini veya kenarlarını verimli ve doğru şekilde taramasını sağlayarak kesim için en uygun başlangıç noktasını belirlemesine olanak tanır.
Arama Hassasiyeti (Search Precision)
CNC cam kesme makinelerinde otomatik hizalama sürecinde lazerin hız parametresinin ayarlanması, işlemin doğruluğunu ve verimliliğini sağlamak için kritik bir faktördür. Bu parametrenin arama sürecini nasıl etkilediğini ve neden bu kadar önemli olduğunu inceleyelim.
Otomatik Hizalamada Lazer Arama Hızının Önemi
Amaç ve Etkisi:
- Hassasiyet Artışı: Lazerin cam yüzeyi üzerinde hareket etme hızı, kenarların ve kilit noktaların ne kadar hassas algılandığını belirler. Kontrollü bir hız, lazerin yüzeyin tüm detaylarını algılayacak yeterli zamanı bulmasını sağlar; bu, özellikle karmaşık veya detaylı kesim görevleri için hayati öneme sahiptir.
- Verimlilik Dengesi: Daha yavaş bir hız, lazerin yakaladığı detayları artırabilirken, aynı zamanda tarama süresini uzatır. Bu nedenle, detay algılama ile operasyonel verimlilik arasında bir denge sağlayacak optimal hızın bulunması gereklidir.
Cam Arayüzündeki Süreç
Soyma (Peeling)
CNC cam kesme uygulamalarında, özel makinelerde çeşitli kaplamaları işlemek için otomatik süreçler içeren arayüzler bulunur. Örneğin, bazı cam parçaları, kesimden önce çıkarılması gereken koruyucu kağıt katmanıyla kaplı olabilir; CNC makineleri bu adımı kolaylaştırmak için otomatik soyma işlevini entegre edebilir. Öte yandan, kaplama plastikse, genellikle kesim sürecini engellemediği için yerinde bırakılır.
Gelişmiş cam CNC makineleri, özellikle çok işlevli modeller, büyük ölçekli veya karmaşık işler için verimlilik amacıyla tasarlanmıştır. Bu makineler, tek bir operasyonel akış içinde kesme, etiketleme ve belirli kaplamaları (örneğin kağıt) çıkarma işlemlerini gerçekleştirebilir, böylece duruş süresini ve manuel müdahaleyi azaltır. Bu, özellikle hassasiyetin ve tekrarlanabilirliğin kritik olduğu optik üretim ve karmaşık bileşen oluşturma gibi endüstrilerde faydalıdır.
Radonix Kontrol Cihazlarında Kaplamalı Camlar için Soyma Süreci
Kaplamalı camlar, genellikle elmas kesici takımların etkinliğini engelleyebilecek bir koruyucu tabaka ile kaplıdır ve bu durum hassas kesim için özel bir yaklaşım gerektirir. Radonix kontrol cihazları bu zorluğu aşağıda ayrıntılı olarak açıklanan sistematik bir soyma süreci ile yönetir:
-
Fırça Hareketi:
- Hazırlık: Tasarım kontrol cihazına yüklendikten sonra, fırça aracı elmas takımın sonunda keseceği yolları izlemek için etkinleştirilir. Bu adım, koruyucu kaplamayı yalnızca bu özel hatlar boyunca kaldırarak, gerçek kesim aşamasında herhangi bir engel oluşmasını önlemek açısından kritik öneme sahiptir.
-
Takım ve Ofset Yapılandırması:
- Takım Yerleşimi: Lazer sensörünün yerleştirilmesine benzer şekilde, hem soyma aracı hem de elmas takım hassas ofsetlerle hizalanır. Bu kurulum, her bir takımın çarpışmadan veya yanlış örtüşmeden çalışmasını sağlar; bu da camın bütünlüğünü korumak ve kesimin doğruluğunu sağlamak için hayati önem taşır.
- Ofset Dikkate Alımı: Soyma aracı ile elmas uç arasındaki mesafe, yani ofset, işlemin başarısı için kritik öneme sahiptir. Doğru ofset ayarları, soyma aracının gerekli soyma alanının dışına taşmamasını ve koruyucu kaplamanın gereksiz şekilde kaldırılmamasını sağlar.
-
Soyma Ofsetinin Ayarlanması:
- Yapılandırma: Radonix sistemindeki her araç, soyma aracı da dahil olmak üzere, elmas kesim yoluyla hizalanması için doğru yapılandırılması gereken kendine özgü bir ofset değerine sahiptir. Bu ofset değerleri dikkatlice hesaplanır ve kontrol cihazının ayarlarında ‘glass’ (cam) kategorisi altında, ‘X’ parametresi içinde ‘Peeling Offset’ olarak etiketlenmiş şekilde saklanır.
- Hassasiyet: Bu ofset değerleri, soyma aracının hassas çalışması için hayati öneme sahiptir; değerler, elmas ucun referans alındığı noktaya göre ölçülür ve her iki eksen için de ayarlanarak soyma işleminin yalnızca gerekli kesim yollarını ortaya çıkarmasını sağlar, böylece çevredeki alanlar zarar görmez.
Bu ayrıntılı ayarların Radonix kontrol cihazlarına entegre edilmesi, makinenin koruyucu kaplamaya sahip camlarla verimli bir şekilde çalışmasına olanak tanır. Elmas takım için gerekli kesim yollarının soyma işlemleri ile hassas şekilde temizlenmesini sağlayarak sistem, kesim işleminin işlevselliğini en üst düzeye çıkarır ve nihai ürünün kalitesini artırır.
Otomatik Hizalama
Bahsettiğiniz "Otomatik Hizalama" özelliği, CNC cam kesme makinelerinde kullanılan gelişmiş bir otomasyon sürecidir. Özellikle ağır veya zor hizalanan cam levhalar için nasıl çalıştığını detaylandıran açıklama aşağıdadır:
“Bir cam levhanın CNC makinesinin tablasına yerleştirildiği ve ağırlığı veya boyutu nedeniyle doğru hizalamanın zor olduğu senaryolarda, 'Otomatik Hizalama' özelliği hayati önem kazanır. Bu işlev, cam levhanın fiziksel sınırlarını ve yönünü otomatik olarak algılamak için lazer algılama teknolojisinden yararlanır. Başlatma sırasında sistem önce camın sol kenarını tespit eder, ardından alt kenar boyunca iki referans noktası daha belirler. Bu üç nokta birlikte, CNC kontrol cihazının cam levhanın referans konumunu ve döndürme açısını hesaplamasını sağlar. Sonuç olarak, tasarım veya kesim yolu camın algılanan yönüne uyacak şekilde otomatik olarak ayarlanır; böylece hizalama noktalarının manuel olarak girilmesine gerek kalmadan tasarımın hassas bir şekilde uygulanması sağlanır. Hava-gaz plazma kesim gibi referans noktalarının manuel olarak ayarlanmasını gerektirebilecek işlemlerden farklı olarak, bu özellik cam levhanın boyutlarına ve yönüne dayalı ayarlamaları otomatikleştirerek işlemleri kolaylaştırır, verimliliği artırır ve kurulum süresini azaltır.”
Lazer Sensörü Kurulumu
Cam kesimi için CNC makineleri kurulurken, özellikle lazer sensörü elmas kesim ucu ile birlikte kullanılıyorsa, lazer sensörünün ofsetini doğru şekilde kalibre etmek son derece önemlidir. İşte bu işlemin nasıl yapılacağı:
Ofseti Tanımlama:
Lazer sensörünün elmas ucuna göre ofset değerleri, doğru hizalama ve kesim için gereklidir. Bu değerler makinenin kontrol sistemine, genellikle 'Elmas ucuna göre X veya Y lazer sensör ofseti' şeklinde etiketlenmiş cam kesme özel ayarları altında girilmelidir.
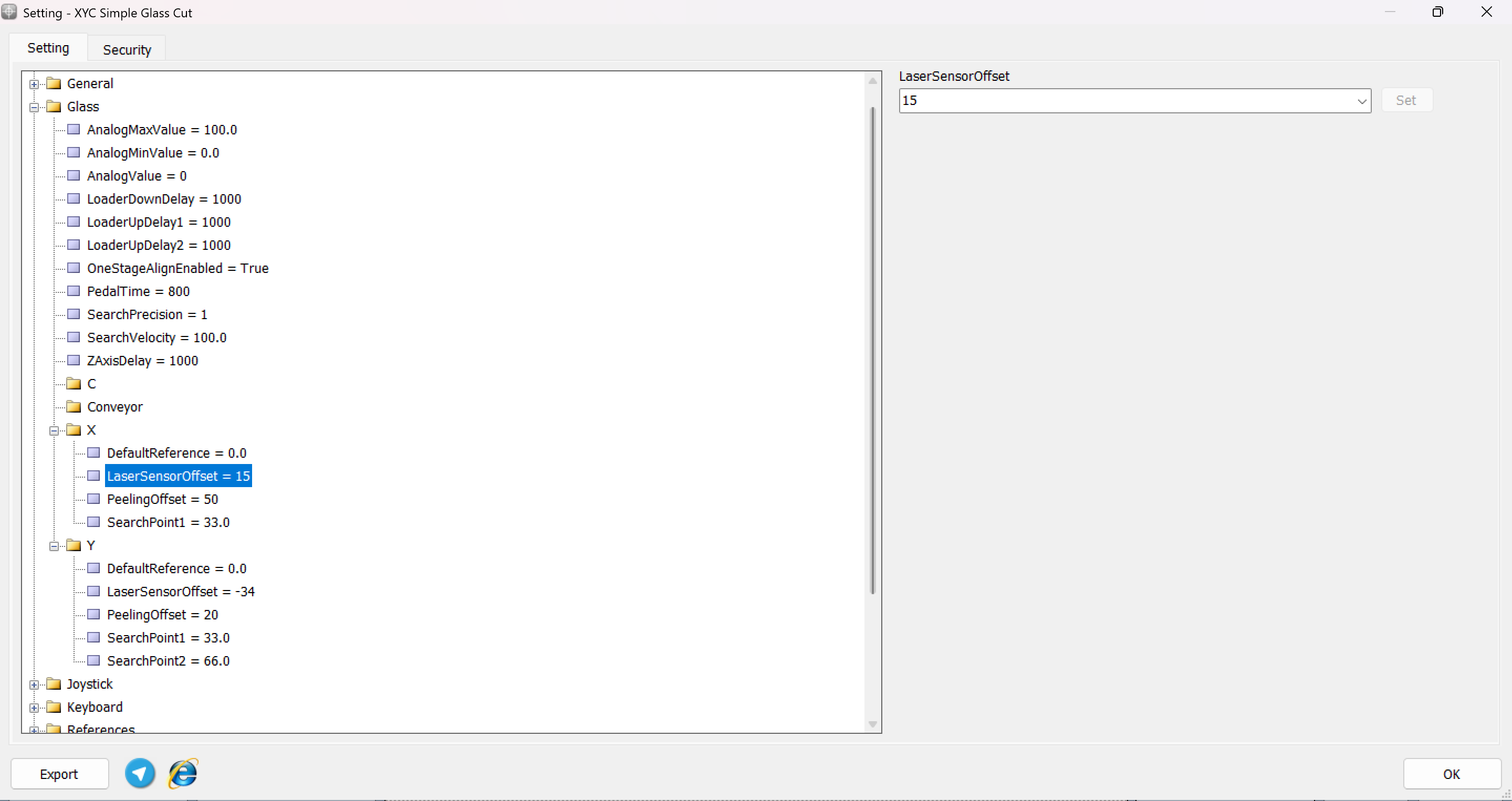
- Sıfır Referans Noktası: Elmas ucun konumu sıfır referans noktası olarak kabul edilir. Bu, lazer sensörün ofsetinin ölçüldüğü temel noktadır.
- Değer Girişi: Eğer lazer sensörü elmas ucundan kesim yönüne doğru ileriye yerleştirilmişse, bu değer pozitif olarak girilmelidir. Tersine, geriye konumlandırılmışsa değer negatif olmalıdır.
Bu kurulum, lazer sensörünün cam levhanın kenarlarını ve yüzeyini doğru şekilde algılamasını sağlar ve elmas ucu ile fiziksel ayrılığı telafi eder. Bu kalibrasyon, hizalama ve kesim kalitesini doğrudan etkilediği için tasarımın hassas bir şekilde uygulanması açısından kritik öneme sahiptir. Bu ayarların titizlikle yapılması, doğruluğu artırır ve kesim işlemi sırasında hata veya malzeme israfı olasılığını azaltır.
Arama Noktası
Radonix kontrol cihazlarıyla desteklenen CNC makine kurulumlarında lazer algılama sürecini optimize etmek için her eksen için uygun arama noktalarının ayarlanması çok önemlidir. Bu parametre, lazerin malzeme kenarlarını bulmak için tarayacağı alanın kapsamını tanımlar, ayarlanabilir bir değerdir ve eksene bağlı olarak değişkenlik gösterir:
-
X Ekseni - Tek Değer Ayarı:
- X ekseni için genellikle yalnızca bir değer gereklidir. Bu değer, X yönündeki arama aralığını belirler. Toplam eksen uzunluğunun yüzdesi olarak ifade edilir ve sistemin eksen genişliği boyunca tanımlanmış bir oranda etkili bir şekilde arama yapmasına olanak tanır.
-
Y Ekseni - Çift Değer Ayarı:
- Buna karşılık, Y ekseni için iki değer gerekir. Bunlar, Y ekseninin başlangıç ve bitiş noktalarındaki arama aralıklarını tanımlar ve işlenecek malzemenin tam derinliğini kapsar. Bu çift noktalı ayar, malzemenin dikey boyutunun tamamen taranmasını sağlar ve kesime başlamadan önce tüm alanın hesaba katıldığından emin olur.
Bu ayarlar, lazer konumlandırma sisteminin özellikle karmaşık veya düzensiz şekilli parçalar için malzemenin sınırlarını doğru şekilde belirlemesini sağlamak açısından kritiktir. Bu parametrelerin ayarlanması, sistemin hassas kesim işlemleri için verimli ve etkili şekilde hazırlanmasına olanak tanır, hata ve malzeme israfı riskini azaltır.
Radonix Kontrol Cihazlarında 'Autoalign' Komutunun Kullanımı için Ayrıntılı Süreç
‘Autoalign’ Komutunun Etkinleştirilmesi:
‘Autoalign’ komutu etkinleştirildiğinde, cihaz yüklenen tasarım parametrelerine dayalı olarak hassas hizalama sağlamak amacıyla tasarlanmış bir diziyi başlatır.
Arama Noktasının Ayarlanması:
- Başlatma: Cihaz, kullanıcı tarafından tasarım gereksinimlerine göre ayarlanan 'Arama Noktası' parametresinde belirtilen genişliğe hareket eder.
- Kenar Algılama Süreci: Cihaz hareket ettikçe camın kenarını tarar. Kenar algılandığında, daha hassas kesim işlemi için başlangıç konumuna geri döner.
- Hassasiyet Artırımı: Makine, tespit edilen kenara daha düşük hızda tekrar yaklaşır ve kenarın tam konumunu daha doğru algılar. Bu adım güvenilirliği sağlamak için iki kez tekrarlanır.
Y Ekseni için Tekrar: Kapsamlı Tarama
- Y Ekseni Tarama: X eksenine benzer şekilde, cihaz Y ekseninde de kenar algılama gerçekleştirir. Bu tarama eksen uzunluğunun %33 ve %66 noktalarında iki kez yapılır ve Y ekseni boyunca kenarın haritalanmasını sağlar.
- Doğruluk Onayı: Bu tekrarlanan taramalar, hem X hem de Y eksenlerinde kenar algılamanın doğru ve tutarlı olmasını garanti eder.
Son Ayarlamalar ve Kesime Başlama
- Hizalama Ayarlamaları: Kenar algılamalarından elde edilen verilere dayanarak, tasarım makine tablası üzerindeki camın gerçek konumu ve yönü ile mükemmel şekilde hizalanacak şekilde hassas biçimde ayarlanır.
- Kesime Başlama: Tüm parametreler ayarlanıp doğrulandıktan sonra, cihaz kesim işlemine başlar ve Y ekseninin %33 noktasından itibaren kesime başlanır.
Bu süreç, Radonix CNC makinesinin camı doğru şekilde hizalamasını ve kesmesini sağlayarak hataları en aza indirir ve nihai ürünün kalitesini maksimize eder. 'Autoalign' özelliği, özellikle malzeme maliyetlerinin ve kesim hassasiyetinin çok önemli olduğu endüstrilerde yüksek hassasiyet gerektiren işlemler için kritik bir özelliktir.
Çerçeve (Frame)
Çerçeve Süreci, gerçek kesim işlemine başlamadan önce doğruluk ve hizalamayı sağlamak amacıyla CNC işleme operasyonlarında uygulanan temel bir güvenlik protokolüdür. Bu prosedür, kesici takımın tasarımın varsayımsal sınırları boyunca malzeme ile temas etmeden hareket ettirilmesini içerir; böylece doğru konumlandırma ve operasyonel parametreler doğrulanır. Bu kesimsiz test çalışması, olası kurulum hataları veya programlama tutarsızlıklarını belirleyerek malzeme israfını ve takım zararını önlemeye yardımcı olur. Bu önleyici önlem, operasyonel güvenlik ve verimliliğin korunması, hem makineyi hem de iş parçasını güvence altına almak açısından kritiktir.
Çerçeve Süreci, takımı tasarımın sınırları boyunca hızlı bir şekilde hareket ettirerek operatörlerin sınırları kesim olmadan hızla tanımlamasını sağlar. Bu hızlı geçiş, kurulumun programlanmış boyutlar ve tasarım düzeniyle doğru şekilde hizalandığını doğrulamaya yardımcı olur ve gerçek işleme süreci başlamadan önce doğruluğu sağlar.
Aslında Çerçeve Süreci, tasarımın işleme alanı içindeki konumunu gösterim hareketi yoluyla tanımlamanıza olanak tanır. Bu işlem, takımın tasarımın projeksiyon sınırları boyunca gerçek kesim yapmadan hareket etmesini sağlar ve tasarımın makine tablasındaki yerleşimi ve hizalamasının görsel ve pratik doğrulamasını sağlar. Bu yöntem, işlemenin istenilen alanda gerçekleşmesini garanti etmek ve kesim başlamadan önce hataları ve malzeme israfını önlemek açısından kritik öneme sahiptir.
Dikkat edilmelidir ki, bu özellik yalnızca tasarım dosyası açıldıktan sonra kullanılabilir hale gelir.
S-CAM
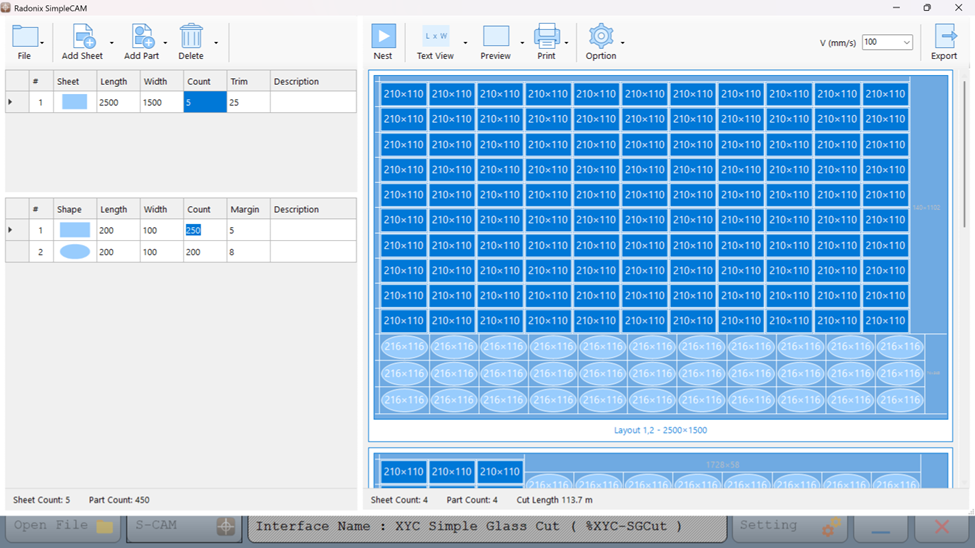
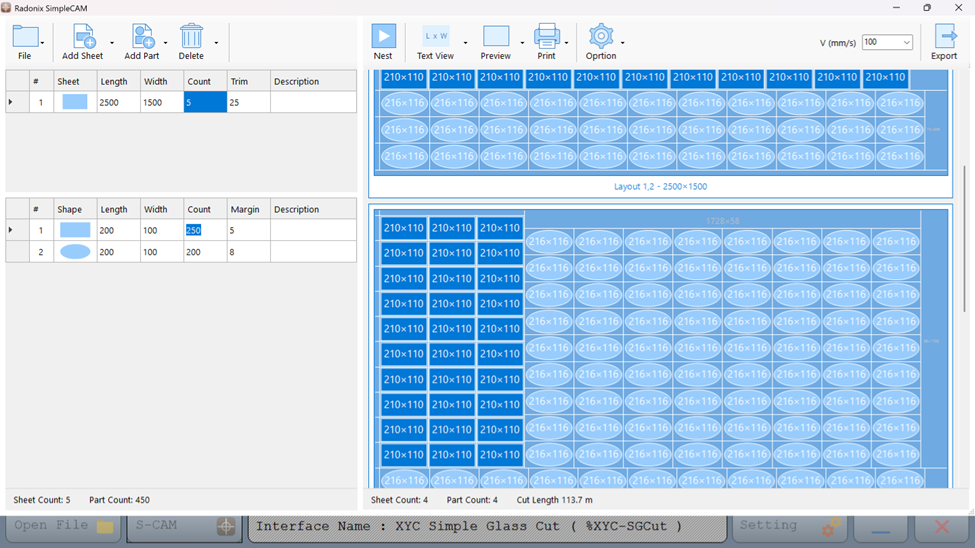
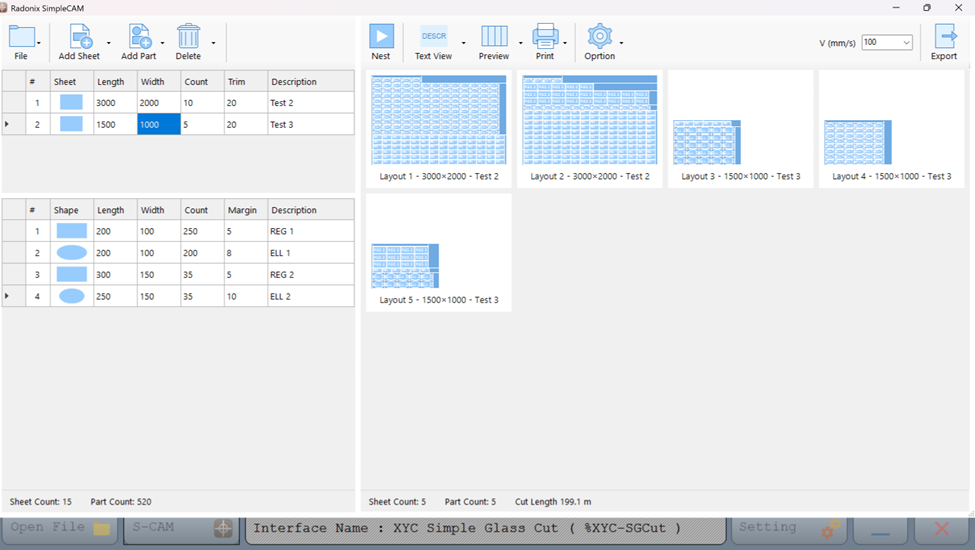
Radonix SimpleCAM’in Kapsamlı Özellikleri
-
Sorunsuz Entegrasyon ve Kullanıcı Dostu Arayüz
- Uyumluluk: Radonix SimpleCAM, Radonix CNC kontrol cihazlarıyla sorunsuz bir şekilde entegre olacak şekilde özel olarak tasarlanmıştır ve yazılım ile donanım arasında hatasız çalışma ve iletişim sağlar.
- Sezgisel Tasarım: Arayüz basittir; operatörlerin yazılımı hızlıca öğrenmesini ve ustalaşmasını kolaylaştırır, böylece eğitim süresini azaltır ve yeni kullanıcılar için sorunsuz geçişler sağlar.
-
Gelişmiş Yerleştirme (Nesting) Yetenekleri
- Verimli Malzeme Kullanımı: Her bir levha üzerinde parça yerleşimini optimize etmek için sofistike bir algoritma kullanır, malzeme kullanımını maksimize eder ve israfı azaltır — bu, maliyet etkin cam üretimi için kritik öneme sahiptir.
- Çeşitli Şekilleri Destekler: Dikdörtgen, elips ve çokgen gibi birçok geometrik şekli destekleyerek çeşitli tasarım gereksinimleri için esneklik sağlar.
-
Hassasiyet ve Kalite Kontrolü
- Kesim Payı ve Marj Ayarları: Bu ayarlar, kesim süreci üzerinde hassas kontrol sağlar; her parçanın, son işleme süreçleri için yeterli alana sahip olmasını sağlar ve son ürünün boyut veya bütünlüğünü etkilemez.
- Hız Ayarları: Operatörler kesim hızını kontrol edebilir; bu, kesim kalitesini artırır ve kesici takımların ömrünü uzatır.
-
Verimlilik Artırıcı Özellikler
- Toplu İşleme ve Çoklu Görev Yürütme: Yazılım, aynı anda birden fazla cam levhayı işleyebilir ve büyük siparişlerin daha kısa sürede tamamlanmasını sağlar. Bu çoklu görev yeteneği, toplam üretim süresini azaltarak verimliliği önemli ölçüde artırır.
- Önizleme ve Yazdırma Seçenekleri: Yerleşim düzenini gerçek kesimden önce önizleme imkânı sağlayarak yerleşimi doğrulamaya ve hataları önlemeye yardımcı olur. Yazdırma yetenekleri, atölye sahası genelinde kolay belge paylaşımı ve iletişim sağlar.
-
Özelleştirme ve Esneklik
- DXF Dosya Aktarımı: Operatörlerin tasarımları doğrudan DXF dosyaları aracılığıyla aktarmasına olanak tanır; bu format yaygın olarak kullanılır ve diğer CAD programlarıyla sorunsuz entegrasyonu destekler.
- Ayarlanabilir Yerleşim Düzeni: Yerleşim düzeninde manuel ayarlamalar yapılabilir; bu, operatörlere özel ihtiyaçlara veya beklenmedik sorunlara göre son dakika değişiklikleri yapma özgürlüğü sağlar.
-
Maliyet Verimliliği
- Azaltılmış Malzeme İsrafı: Malzeme kullanımını optimize ederek, yazılım malzeme israfına bağlı maliyetleri önemli ölçüde azaltır.
- Verimli Üretim: Tasarımdan kesime kadar tüm üretim sürecini sadeleştirerek çevrim sürelerini kısaltır ve genel çıktı kapasitesini artırır.
-
Adanmış Destek ve Sürekli Güncellemeler
- Teknik Destek: Radonix, sağlam müşteri desteği ve en son teknolojilerle ve üretim uygulamalarıyla uyumluluğu sağlamak için düzenli yazılım güncellemeleri sunar.
- Çalıştır (Yeşil Oynat İkonu): İşleme programını başlatır.
- Duraklat (Turuncu Duraklat İkonu): Mevcut programı geçici olarak duraklatır.
- Sıfırla (Kırmızı Kare İkonu): Mevcut programı durdurur ve sıfırlar; operatörün gerekirse baştan başlamasına olanak tanır.
Girişler ve Çıkışlar Arasındaki İlişkiler
Bu bölümde, Girişler ve Çıkışlar arasındaki ilişkileri inceleyebiliriz.
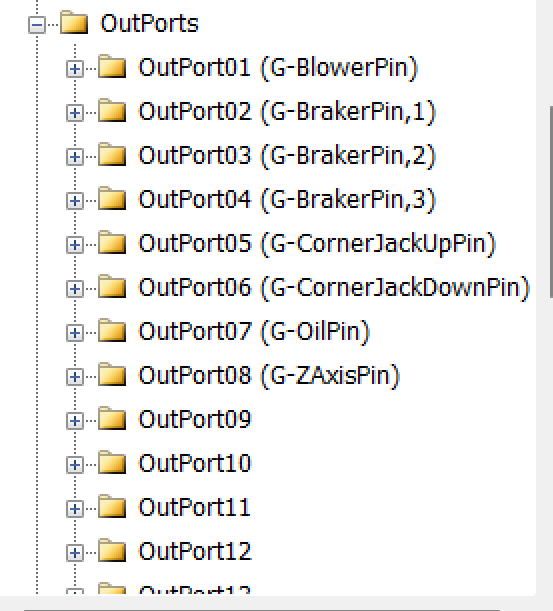
Çıkış Listeleri
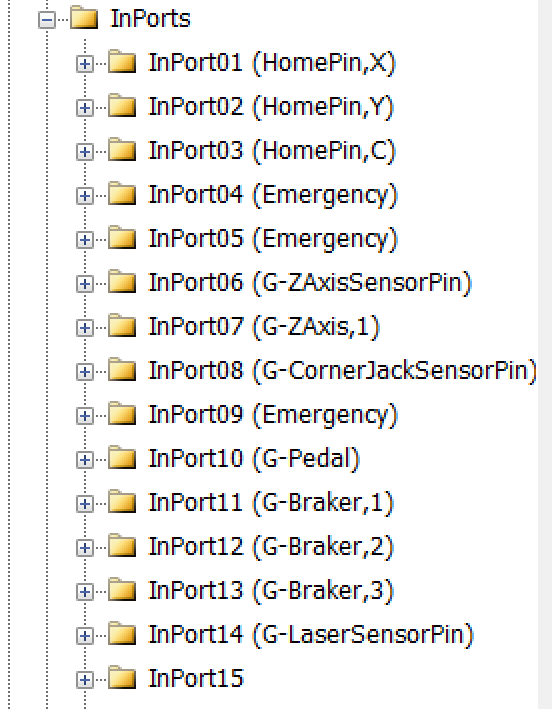
Giriş Listeleri
Girişler
Bu bölümde, Girişlerin yapılandırmasını inceleyeceğiz.
Temel olarak, Inports (Giriş Portları) dalı açıldığında bu ayarlar görüntülenir.
Girişleri Yapılandırma: Genel Bakış
CNC sistemimizde girişlerin yapılandırılması, düzgün çalışma, hassas kontrol ve güvenlik sağlamak için temel bir adımdır. Girişler, yapılandırma ve amaçlarına göre iki ana kategoriye ayrılabilir: Donanım Tabanlı Girişler ve Yazılım Tabanlı Girişler. Bu esneklik, sistemin çok çeşitli uygulamalara ve makine gereksinimlerine uyum sağlamasına olanak tanır.
1. Donanım Tabanlı Girişler
Donanım girişleri, kontrol cihazına fiziksel olarak bağlı cihazları içerir ve makinenin çevresiyle doğrudan etkileşime olanak tanır. Bu girişler, güvenlik, makine kontrolü ve gerçek zamanlı geri bildirim açısından kritik öneme sahiptir.
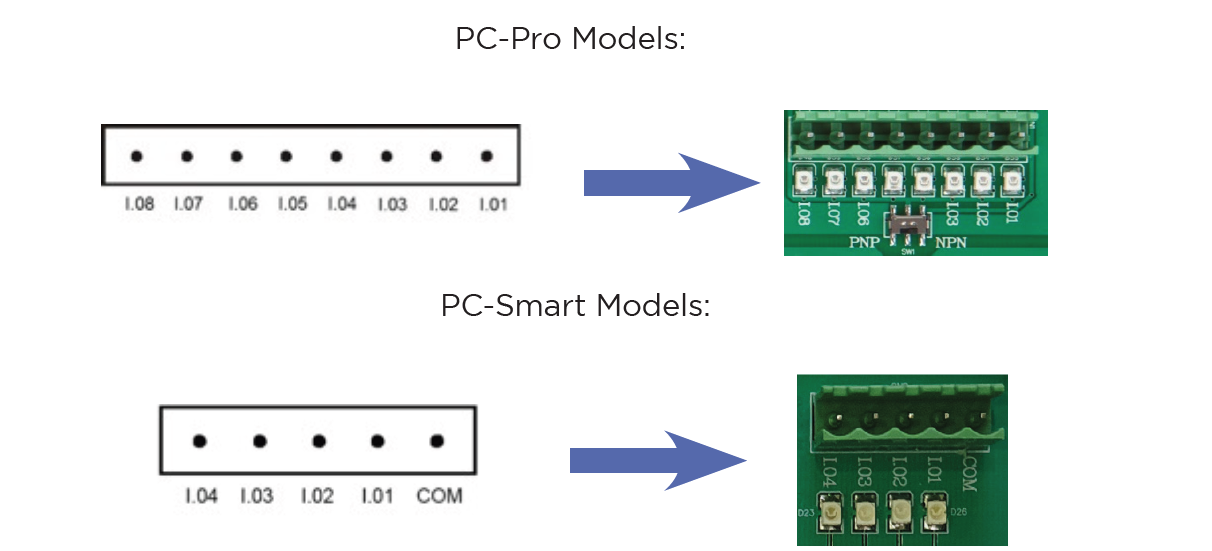
Radonix kontrol cihazlarının dijital girişleri, I.[n] olarak adlandırılır. Buradaki n, sıfırdan büyük bir sayıdır ve giriş numarasını temsil eder. Bu girişler optik izolatörlerle izole edilmiştir ve düşük empedans nedeniyle düşük parazit toleransına sahiptir.
Radonix kontrol cihazlarındaki dijital girişler, cihazın veya sensörün çıkışına bağlı olarak NPN ve PNP modları arasında geçiş yapabilir. Mod değişim anahtarı, PNP çıkışlı cihazlar için PNP konumuna ve NPN çıkışlı cihazlar için NPN konumuna ayarlanmalıdır.
Endüstriyel otomasyonun çeşitli alanlarında, PNP ve NPN için eşdeğer terimler bulunur. Bu terimlerden bazı örnekler şunlardır:
NPN = Sink = Low Active
PNP = Source = High Active
Radonix Sistemlerinde PNP ve NPN Modları Arasında Geçiş Yapma
Radonix kontrol cihazlarında PNP (pozitif mantık) ve NPN (negatif mantık) modları arasında geçiş yapabilme yeteneği, kullanılan kart modeline bağlıdır. Bu esneklik, sistemin farklı kablolama ve sensör konfigürasyonlarıyla uyumlu olmasını sağlar.
-
PC Pro LAN:
-
Kart üzerinde küçük bir DIP anahtarı bulunur.
-
Bu anahtar, kullanıcıların PNP ve NPN modları arasında geçiş yapmasını sağlar.
-
Nasıl Kullanılır:
- Kart üzerindeki DIP anahtarını bulun.
- Anahtarı istenilen moda (PNP veya NPN) göre çevirin.
- Değişiklik yapmadan önce kartın kapalı olduğundan emin olun, aksi takdirde hasar oluşabilir.
-
-
PC Smart:
-
PC Smart modelinde DIP anahtarı yerine her 4 giriş pini seti için bir Come Pin (Ortak Pin) kullanılır.
-
Bu pin, ilgili girişler için giriş mantığını (PNP veya NPN) tanımlamanıza olanak tanır.
-
Nasıl Kullanılır:
- Come Pin, uygun voltaja bağlanmalıdır (PNP için pozitif, NPN için toprak).
1. PNP Modu (Source Mode):
- COM pini 0V'a bağlıysa, giriş pinleri 24V sinyali ile tetiklenir (Açılır).
- Bu konfigürasyonda, sensörün çıkış kablosu girişin tetiklenmesi için 24V sağlamalıdır.
2. NPN Modu (Sink Mode):
-
COM pini 24V'a bağlıysa, giriş pinleri 0V sinyali ile tetiklenir (Açılır).
- Bu konfigürasyonda, sensörün çıkış kablosu girişi tetiklemek için 0V’a çekmelidir.
-
Her 4 giriş pinlik grup kendi Come Pin’ine sahiptir, bu sayede aynı kart üzerinde karışık konfigürasyonlar yapılabilir.
-
Donanım Girişi Örnekleri:
- Limit Switchler (Sınır Anahtarları): Eksen hareketleri için fiziksel sınırları tanımlar.
- Home Sensors (Referans Sensörleri): Makine için referans (Home) konumunu belirler – çoğunlukla yakınlık sensörleri (proximity) kullanılır.
- Acil Durdurma Butonları: Acil durumlarda işlemlerin anında durdurulmasını sağlar.
- Diğer Yakınlık Sensörleri: Makinenin çalışma alanında nesne veya takımları algılar.
- Basmalı Butonlar ve Seçici Anahtarlar: Belirli makine işlevlerini veya modlarını tetikler.
- Tarayıcılar (Scanners): Özellikle cam veya altın CNC işlemleri gibi özel süreçlerde belirli özellikleri ölçmek veya algılamak için kullanılır.
Yapılandırma Süreci:
- Bağlantı: Donanım bileşenini (ör. bir anahtar veya sensör) fiziksel olarak kontrol cihazındaki belirlenmiş giriş pinine bağlayın.
- Giriş Tanımlaması: Girişin rolünü tanımlamak için kontrol cihazı yazılımını kullanın (örneğin
HomePin
,LimitPin
veya belirli işlevler için özel bir giriş). - Kutupluluk Ayarları:
- Bağlı donanımın varsayılan durumuna göre giriş tipini Normalde Açık (NO) veya Normalde Kapalı (NC) olarak ayarlayın.
- Örneğin:
- NC bir acil durdurma butonu, basılana kadar aktif (kapalı) durumda kalır.
- NO bir yakınlık sensörü, yalnızca bir nesne algılandığında (kapalı) aktif hale gelir.
2. Yazılım Tabanlı Girişler
Yazılım Tabanlı Girişler, isteğe bağlı bağlantıların yapılandırılması ve ilgili fiziksel donanımla entegre edilmesi için basit mantıksal işlevsellik sağlar. Mikro programlamaya gerek duymadan hızlı ve basit kurulum sağlarlar. Kullanıcılar sadece listeden seçim yaparak ayarları yapılandırabilir ve verimliliği maksimize edebilir.
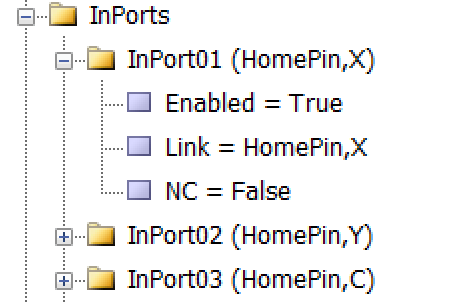
Şekilde gösterildiği gibi, her giriş aşağıdaki gibi üç alt dala ayrılmıştır:
- Enable (Etkinleştir): Bu alt dal iki değerden birine ayarlanabilir: True veya False.
- Link (Bağlantı): Gerçekleştirilmesi veya kontrol edilmesi gereken görev veya işlevi belirtir. Sensörler, butonlar ve anahtarlar gibi giriş görevi görebilecek tüm cihazları içerir.
- NC: Belirli girişin Normalde Açık (NO) mu yoksa Normalde Kapalı (NC) mı olduğunu belirler.
Yazılım Girişi Örnekleri:
- Sanal Limit Anahtarları:
- Eksen hareket sınırlarını, makine tablası boyutuna göre yazılım parametreleri ile tanımlar.
- Mantıksal Tetikleyiciler: Belirli işlemler için koşullu tetikleyicileri tanımlar (örneğin, eksen limit anahtarına ulaştığında).
- Simüle Girişler: Fiziksel bileşenlerin mevcut olmadığı test senaryolarında kullanılır.
Yapılandırma Süreci:
-
Yapılandırma Arayüzüne Erişim:
- Girişleri yönetmek için kontrol cihazı yazılım ayarlarını açın.
-
Parametreleri Tanımlayın:
Örnek olarak bir limit anahtarı ayarlamak için:
-
ayar —→ System —→ In ports —→ Enabled = True
Linked = LimitPin,X
NC = True
-
Kilitlemeler veya simülasyonlar için ek mantıksal koşullar yapılandırın.
-
-
Ayarları Doğrulama:
- CAM Pro TEST girişi yapılandırmaları ile yazılımı test edin ve işlevselliği ve güvenliği sağlayın.
Çıkışlar
Bu bölümde, Çıkışların yapılandırılmasını inceleyeceğiz.
Girişleri Yapılandırma: Genel Bakış
Radonix sistemlerinde, Outports (Çıkış Portları) röleler, aktüatörler, alarmlar ve diğer cihazları kontrol eden çıkış sinyallerini yöneten kritik bileşenlerdir. Çıkışlar, yapılandırma ve amaçlarına göre iki ana türe ayrılabilir: Donanım Tabanlı Çıkışlar ve Yazılım Tabanlı Çıkışlar. Bu esneklik, sistemin çeşitli uygulamalara ve makine gereksinimlerine uyum sağlamasına olanak tanır.
1. Donanım Tabanlı Çıkışlar
Donanım çıkışları, kontrol cihazından harici cihazlara gönderilen fiziksel sinyalleri içerir ve makinenin çevresinin doğrudan kontrol edilmesini sağlar. Bu çıkışlar, operasyonel güvenlik, makine çalıştırma ve gerçek zamanlı komut yürütme açısından kritik öneme sahiptir; CNC sistemi içinde verimli iş akışı ve koordinasyon sağlar.
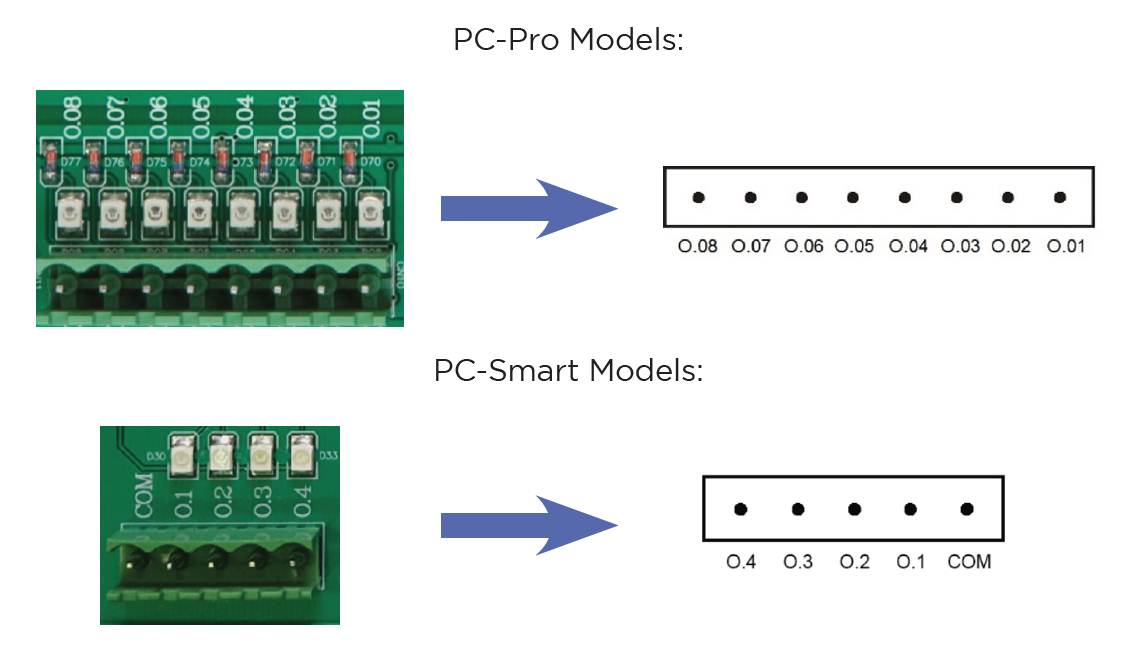
Radonix kontrol cihazlarının dijital çıkışları O."N" olarak adlandırılır. Buradaki n sıfırdan büyük bir sayı olup çıkış numarasını temsil eder.
Radonix kontrol cihazları, Outports için dayanıklılığı, güvenliği ve güvenilirliği sağlamak amacıyla sağlam koruma mekanizmaları içerir. Bu mekanizmalar, özellikle PC-Pro ve PC-Smart kartları olmak üzere farklı modeller arasında değişkenlik gösterir ve her biri kendine özgü koruma özelliklerine ve arıza yönetim süreçlerine sahiptir.
PC-Pro LAN Modellerinde Çıkış Davranışı
- PC-Pro LAN modelinin çıkışları sabit olarak NPN modunda çalışır.
- Nasıl Çalışır:
- Bir çıkış ON olduğunda, sinyali toprağa çekerek 0 volt sağlar.
- Bir çıkış OFF olduğunda, yüksek empedans durumundadır ve devreyi fiilen ayırır.
- Kablolama Dikkate Alınması Gerekenler:
- Bağlı cihazlar, yükün pozitif bir kaynaktan voltaj aldığı ve çıkış sinyali toprağa çekildiğinde aktif hale geldiği NPN mantığıyla uyumlu olmalıdır.
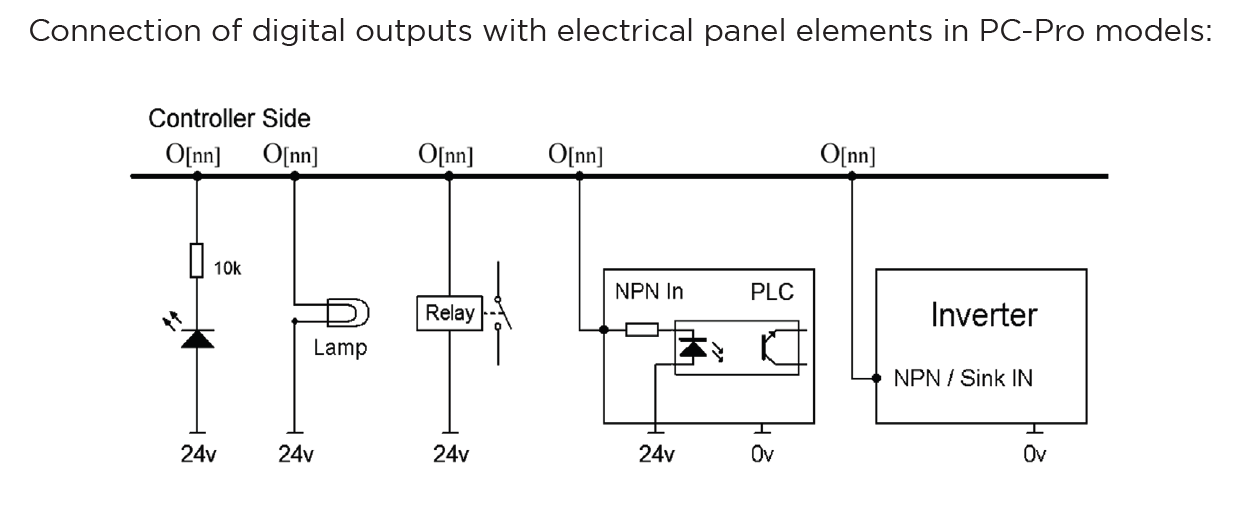
PC-Smart Modellerinde Çıkış Davranışı
- PC-Smart modeli, çıkışların PNP modu veya NPN modunda çalışmasını sağlayan esnek bir yapı sunar; bu, COM Pin bağlantısına bağlıdır.
- Nasıl Çalışır:
- Çıkışların sağladığı voltaj, COM Pin'e ne bağlandığına bağlıdır:
- COM Pin 24V'a Bağlıysa: Çıkışlar etkin olduğunda 24 volt sağlar.
- COM Pin Toprağa Bağlıysa: Çıkışlar etkin olduğunda 0 volt sağlar (NPN modu).
- Çıkışların sağladığı voltaj, COM Pin'e ne bağlandığına bağlıdır:
- Esneklik:
- Bu tasarım, PC-Smart modellerinin farklı kablolama gereksinimleri ve cihaz mantığı tercihlerine uyum sağlamasına imkân tanır.
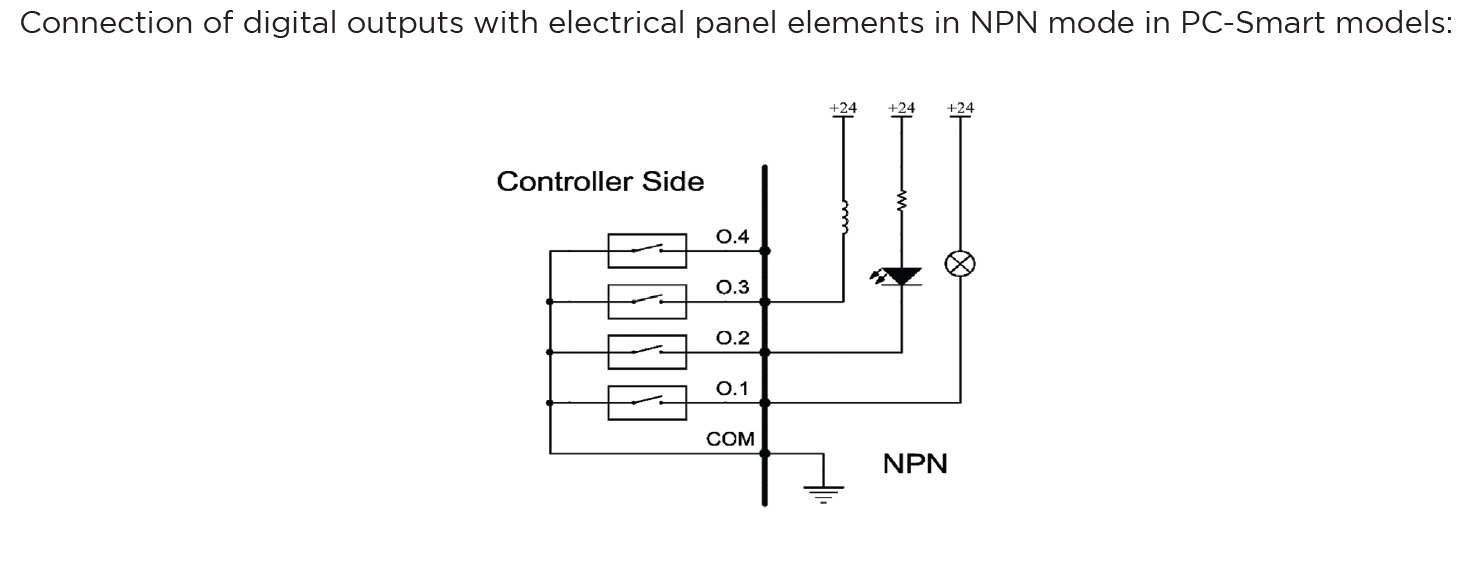
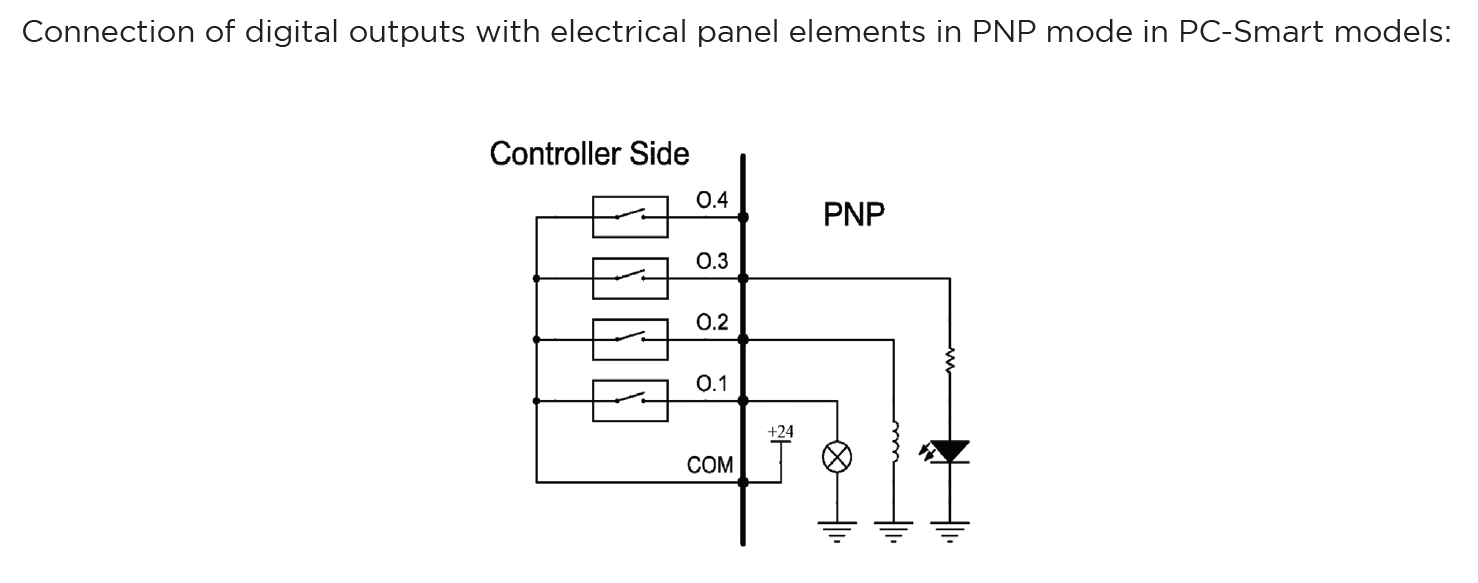
Çıkışlar için Yapılandırma Süreci:
-
Bağlantı:
- Donanım bileşenini (ör. röle, elektrik valfi, fren, alarm) fiziksel olarak kontrol cihazındaki belirlenmiş çıkış pinine bağlayın.
- Gerekli mantık (PNP veya NPN) ve voltaj uyumluluğuna göre doğru kablolama yapıldığından emin olun.
-
Çıkış Tanımlaması:
- Kontrol cihazı yazılımını kullanarak çıkışın rolünü tanımlayın (örneğin,
G-BlowerPin
,G-BrakerPin,2
veya belirli işlevler için özel çıkış). - Çıkışı sistem ayarlarında hedeflenen cihaza veya operasyona atayın.
- Kontrol cihazı yazılımını kullanarak çıkışın rolünü tanımlayın (örneğin,
-
Mantık Ayarları:
- Bağlı cihazın gereksinimlerine göre çıkış mantığını ayarlayın:
- Aktif Yüksek (PNP): Çıkış etkin olduğunda voltaj (örneğin 24V) gönderir.
- Aktif Düşük (NPN): Çıkış etkin olduğunda sinyali toprağa (0V) çeker.
- Bağlı cihazın gereksinimlerine göre çıkış mantığını ayarlayın:
-
Test ve Doğrulama:
- Yapılandırmadan sonra, çıkışın CAM Pro Test uygulamasında amaçlandığı gibi çalıştığından emin olun.
- Multimetre veya diğer tanı araçları ile çıkış voltajını ve davranışını doğrulayın.
2. Yazılım Tabanlı Çıkışlar
Yazılım Tabanlı Çıkışlar, ilgili fiziksel donanımlarla entegre edilebilen basit mantıksal işlevsellik sağlar. Bu özellikler, kontrol yeteneklerini geliştirmek için kritik öneme sahiptir. Mikro programlamaya gerek kalmadan hızlı ve kolay kurulum sağlarlar. Kullanıcılar sadece listeden seçim yaparak ayarları yapılandırabilir ve verimliliği en üst düzeye çıkarabilir.
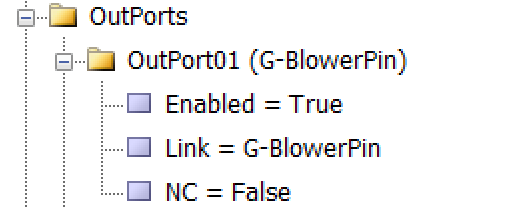
Şekilde gösterildiği gibi, her çıkış üç alt dala ayrılmıştır ve bunlar aşağıda detaylandırılmıştır:
- Enable (Etkinleştir): Bu alt dal iki değerden birine ayarlanabilir: True veya False.
- Link (Bağlantı): Gerçekleştirilmesi veya kontrol edilmesi gereken görevi belirtir. Aktüatörler, ışıklar, alarmlar gibi çıkış görevi görebilecek tüm cihazları içerir.
- NC: Belirli çıkışın Normalde Açık (NO) mu yoksa Normalde Kapalı (NC) mı olduğunu belirler.
Yazılım Tabanlı Çıkış Örnekleri:
- Sanal Röleler:
- Cihazların operasyonel ihtiyaçlara göre etkinleştirme sınırlarını tanımlamak için yazılım parametrelerini kullanır.
- Mantıksal Tetikleyiciler: Belirli çıkışları (ör. alarmlar veya belirli işlevler için röleler) etkinleştirmek için koşullu tetikleyicileri tanımlar.
- Simüle Edilmiş Çıkışlar: Test veya fiziksel bileşenlerin mevcut olmadığı senaryolarda kullanılır.
Yapılandırma Süreci:
-
Yapılandırma Arayüzüne Erişim:
- Çıkışları yönetmek için kontrol cihazı yazılım ayarlarına gidin.
-
Parametreleri Tanımlayın:
-
Örneğin, bir frekans konvertörünü ileri yönde çalıştırma komutu vermek için aşağıdaki gibi parametreleri girin:
- setting —→ System —→ Outports —→ Enabled = True
- Linked = C-CutPin
- NC = True
-
-
Ayarları Doğrulama:
- Yapılandırılan yazılım çıkışlarının doğru ve güvenli şekilde çalıştığını test edin ve gerçek uygulamalarda etkinliklerini doğrulayın.
Radonix CNC Kontrol Cihazı için Kurulum ve Ayarlama Süreci
Radonix, bir Radonix CNC kontrol cihazını kurmak ve yapılandırmak için bu ayrıntılı adım adım kılavuzu takip etmenizi önerir. Süreç, donanımın kablolanmasından yazılımdaki parametrelerin ayarlanmasına kadar her şeyi kapsar. Bu yaklaşım, tüm kritik bileşenleri ele alarak müşterilere sorunsuz bir kurulum deneyimi sağlamayı amaçlar.
Radonix CNC Kontrol Cihazı için Bileşenlerin Kablolanması
Doğru kablolama, güvenilir ve yüksek performanslı bir CNC makinesinin temelidir. Kablolamaya profesyonel bir yaklaşım, Radonix kontrol cihazı, servo veya step motorlar, sensörler, VFD’ler (Değişken Frekanslı Sürücüler) ve diğer çevre birimleri arasında sorunsuz iletişimi sağlar. Bu kılavuz, uygun güç kaynaklarının seçilmesi, güvenliğin sağlanması ve en iyi performansın elde edilmesi dahil olmak üzere tüm bileşenlerin kablolaması hakkında uzman tavsiyesi sunar.
1. Ana Bileşenlere Genel Bakış
Tipik bir CNC sistemi aşağıdaki bileşenleri içerir ve bu bileşenlerin her biri hassas ve güvenli kablolama gerektirir:
- Radonix CNC Kontrol Cihazı: Merkezi kontrol birimi.
- Servo veya Step Motorlar: Eksen hareketinden sorumludur.
- Değişken Frekanslı Sürücü (VFD): Mil motorunu kontrol eder.
- Sensörler:
- Home Sensörleri: Eksen referanslaması için.
- Limit Switch’ler: Sınır kontrolü için.
- Home Sensörleri eksen referanslaması için.
- Limit Switch’ler sınır kontrolü için.
- Acil Durdurma (E-Stop): Acil durumlarda anında durdurma sağlar.
- Güç Kaynakları: Farklı bileşenler için düzenlenmiş güç sağlar.
- Çevresel Çıkışlar: Röleler, soğutma pompaları ve alarmları içerir.
2. Ana Güç Kaynağının Kablolanması
Uygun Güç Kaynağının Seçilmesi
-
Kontrol Cihazı Güç Kaynağı:
Radonix kontrol cihazlarını beslemek için 24V anahtarlamalı güç kaynakları kullanılması önerilir. Elektrik panosundaki gerekli güç kaynağı akımını belirlemek için, güç kaynağına bağlı her bir elemanın akım tüketimi hesaplanmalıdır. Örneğin, bir pano içinde 4 röle, 3 pnömatik solenoid valf ve bir kontrol cihazı varsa, akım tüketimi Ohm Kanunu (V = I*R) kullanılarak belirlenebilir. Elektrik akımları hesaplanmalı ve güvenlik katsayısı da dikkate alınarak güç kaynağı akımı olarak toplamları değerlendirilmelidir. Örneğin, rölelerin akımı 0.1A ve solenoid valflerin akımı 0.25A ise, toplam akım şöyle hesaplanabilir:
Toplam Akım = kontrol cihazı akımı + röle akımı + solenoid valf akımı IT = 0.5 + 4 * 0.1 + 3 * 0.25 = 1.65A
3. CNC Kablolaması için Parazit Önleyici Önlemler
Elektromanyetik girişim (EMI) veya elektriksel parazit, özellikle kontrol cihazları, servo sürücüler ve sensörler gibi hassas bileşenler kablolanırken CNC sistemlerinde yaygın bir sorundur. Parazit, sinyalleri bozabilir, makine davranışında dengesizlik yaratabilir ve zamanla bileşenlere zarar verebilir. Sağlam parazit önleyici önlemler uygulamak, CNC makinenizin güvenilir ve hassas çalışmasını sağlamak açısından kritiktir.
Elektriksel Parazit Kaynakları
- Yüksek Frekanslı Cihazlar:
- Değişken Frekanslı Sürücüler (VFD) – (İlgili Makinelerde)
- Anahtarlamalı güç kaynakları
- Yüksek Güçlü Bileşenler:
- Mil motorları – (İlgili Makinelerde)
- Servo ve step motorlar
- Uzun Kablolar:
- Uzun kablolar anten gibi davranır, EMI toplar.
- Güç Hatlarına Yakınlık:
- Sinyal ve güç kablolarının yakın geçmesi parazite neden olabilir.
Temel Parazit Önleyici Önlemler
1. Korumalı Kablolar Kullanın
- Amacı: Korumalı kablolar, elektromanyetik parazitin hassas sinyaller üzerindeki etkisini azaltır.
- Uygulama:
- Pulse+, Pulse-, Direction+, Direction- ve sensör sinyalleri gibi sinyal hatları için bükümlü çift korumalı kablolar kullanın.
- Korumayı yalnızca bir uçtan toprağa bağlayarak topraklama döngülerinden kaçının.
2. Sinyal ve Güç Kablolarını Ayırın
- Amacı: Yüksek güçlü kabloların düşük güçlü sinyal kablolarında parazit oluşturmasını önleyin.
- Uygulama:
- Sinyal kablolarını (ör. sensör ve kontrol sinyalleri) motor gücü ve VFD çıkışı gibi güç kablolarından ayrı yönlendirin.
- Bu kablolar arasında en az 10-15 cm mesafe bırakın.
- Güç ve sinyal hatları için farklı kablo tavaları veya boruları kullanın.
3. Uygun Topraklama
- Amacı: İyi tasarlanmış bir topraklama sistemi paraziti en aza indirir ve bileşenleri korur.
- Uygulama:
- Elektrik kutusu içinde merkezi bir topraklama noktası oluşturun (genellikle topraklama barası olarak adlandırılır).
- Tüm topraklama kabloları (kontrol cihazı, sürücüler, motorlar, vb.) bu merkezi noktaya bağlanmalıdır.
- Zincirleme toprak bağlantılarından kaçının; bu, parazite yol açabilir.
4. Ferrit Boncukları Takın
- Amacı: Ferrit boncuklar, sinyal ve güç kablolarındaki yüksek frekanslı paraziti filtreler.
- Uygulama:
- Ferrit boncukları kontrol cihazı veya servo sürücüye yakın sinyal ve kontrol kablolarına takın.
- Özellikle parazitli ortamlarda birden fazla boncuk kullanın.
5. VFD Kablolamasını Düzgün Yapın
- Amacı: VFD’ler önemli bir parazit kaynağıdır ve özel dikkat gerektirir.
- Uygulama:
- VFD ile mil motoru arasına korumalı kablo kullanın.
- Kablo korumasını VFD ucunda toprağa bağlayın.
- VFD giriş ve çıkışlarına hat filtreleri veya şok bobinleri yerleştirin.
6. Kablo Uzunluklarını Kısaltın
- Amacı: Uzun kablolar parazit alma konusunda daha hassastır.
- Uygulama:
- Kabloları esneklikten ödün vermeden mümkün olduğunca kısa tutun.
- Gereksiz gevşeklikten veya kablo halkalarından kaçının.
7. İzole Güç Kaynakları Kullanın
- Amacı: Bir sistemdeki parazitin diğer sistemi etkilemesini önleyin.
- Uygulama:
- Sensörler, enkoderler ve kontrol cihazı gibi hassas bileşenler için ayrı, izole güç kaynakları kullanın.
- Güç kaynaklarının yeterli şekilde derecelendirildiğinden ve düzgünce topraklandığından emin olun.
8. Optik İzolasyon Kullanın
- Amacı: Kontrol cihazını harici bağlantılardaki parazitlerden koruyun.
- Uygulama:
- Sensörler, röleler veya anahtarlar gibi harici cihazlarla bağlantılarda optoizolatörler kullanın.
- Radonix kontrol cihazlarının birçoğunda giriş ve çıkışlar için dahili optik izolasyon bulunur.
9. Güvenli Bağlantılar
- Amacı: Gevşek bağlantılar parazit kaynağı olabilir.
- Uygulama:
- Tüm konnektörlerin sıkı ve sağlam olduğundan emin olun.
- Olası kazara bağlantı kesilmelerini önlemek için kilitli konnektörler kullanın.
10. Hat Filtresi ve Aşırı Gerilim Koruyucular
- Amacı: Yüksek frekanslı paraziti bastırır ve gerilim dalgalanmalarına karşı koruma sağlar.
- Uygulama:
- AC şebeke beslemesine EMI hat filtreleri kurun.
- Kontrol cihazı ve VFD’nin güç girişlerine aşırı gerilim koruyucuları yerleştirin.
Yazılım Yapılandırması: Sistemi Hayata Geçirme
Adım 1: Radonix Cam Pro’yu Yükleyin
- Yazılımı bilgisayarınıza indirin ve yükleyin.
- Kontrol cihazını açtığınızda LAN portundaki LED’lere dikkat edin: biri sabit yanmalı, diğeri ise yanıp sönmelidir.
- Radonix kontrol cihazını bilgisayara LAN veya USB kablosuyla bağlayın.
Adım 2: İlk Kurulum
- Yazılımı açın ve sistemi başlatın.
- Varsayılan ayarların uygulanmasını sağlamak için fabrika ayarlarına sıfırlama yapın.
Adım 3: Girişleri Yapılandırın
- Ayarlar > Sistem > Inports yolunu izleyin.
- Her girişe bir rol atayın:
EmergencyStop
→ Acil Durdurma butonu içinHomePin, X/Y/Z
→ Home (referans) sensörleri içinLimitPin, X/-X
→ Limit switch’ler için
- Her bir girişi fiziksel olarak tetikleyerek ve yazılım yanıtını gözlemleyerek test edin.
Adım 4: Çıkışları Yapılandırın
- Ayarlar > Sistem > Outports yolunu izleyin.
- Her çıkışa bir görev atayın:
C-CutPin
→ Torç açmak içinC-ZfreePin,1
→ Z eksenini yukarı kaldırmak için röleyi etkinleştirmeC-ZfreePin,-1
→ Z eksenini aşağı indirmek için röleyi etkinleştirme
- Yazılım üzerinden çıkışları değiştirerek bağlı cihazların tepkisini gözlemleyin.
Adım 5: Eksen Kalibrasyonu
- Ayarlar > Sistem > Kalibrasyon bölümüne gidin.
- Her eksen için şu parametreleri girin:
- Adım Başına Birim (Steps per Unit): Vida adımı, motor adımları ve enkoder çözünürlüğüne dayanır.
- Maksimum Hareket (Max Travel): Her eksen için maksimum hareket mesafesini tanımlar.
- Kalibrasyonu, hareket komutları vererek ve gerçek hareket mesafelerini ölçerek test edin.
1. Acil Durdurma (E-Stop)
Sanayi ortamlarında kullanılan kritik bir tepki mekanizmasıdır. Cihaz ve ekipmanı derhal durdurarak ani tehlikelere karşı koruma sağlar. Bu işlem genellikle, sistemin enerji beslemesini kesen ve tüm operasyonları durduran bir acil durdurma butonu veya anahtarı ile gerçekleştirilir. Böylece kazalar, yaralanmalar veya makine hasarları en aza indirilmiş olur.
Yapılandırılabilir Acil Durum Modu
Kullanıcıların sistem ayarları aracılığıyla özel acil durum yanıtları tanımlamasına ve kurmasına olanak tanıyan gelişmiş bir kontrol sistemi özelliğidir. Bu mod, tespit edilen tehdidin türüne ve ciddiyetine göre farklı düzeylerde veya türlerde tepkiler oluşturacak şekilde programlanabilir.
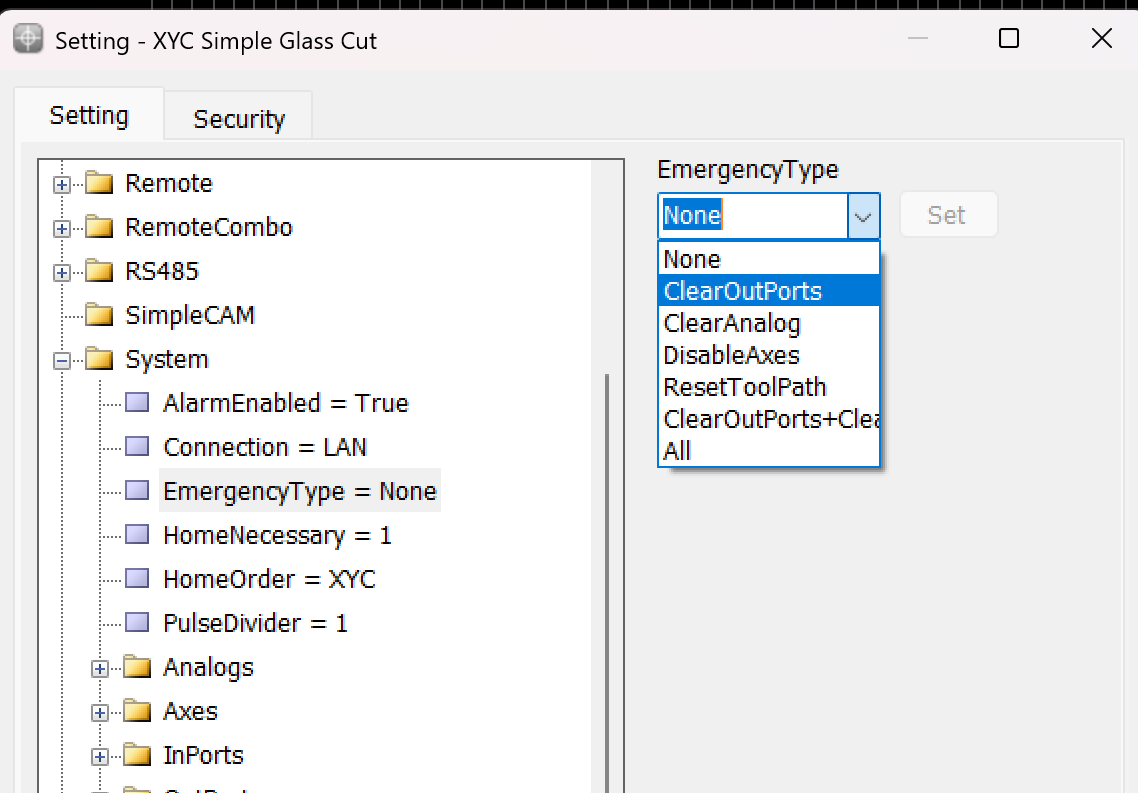
Bu değişken, Acil Durum butonuna basıldığında gerçekleşecek işlemi belirlemek için kullanılır:
- None: Bu mod seçildiğinde, makine duraklatılmış gibi davranır. Cihaz tüm aktiviteleri durdurur ancak bu mod tetiklenmişse aynı noktadan devam edemez.
- ClearOutPorts: Bu mod etkinleştirildiğinde eksenler durur ve kontrol cihazının tüm dijital çıkış portları kapanır. Sistem sıfırlanana kadar başka komutların makineyi etkilemesi engellenir.
- ClearAnalog: Bu mod, eksenleri durdurur ve tüm analog çıkışları kapatır. Takım basıncı veya mil hızı gibi değişkenleri kontrol eden çıkışların devre dışı bırakılmasını sağlar.
- DisableAxes: Bu modda eksenler durur ve devre dışı bırakılır; motorlar ayrılır ve elle itilerek serbestçe hareket edebilir hale gelir.
- ResetToolPath: Eksenleri durdurur ve takım yolunu programın başlangıcına sıfırlar. Hasar önlemek veya bir hatayı düzeltmek için işlemin baştan başlaması gereken durumlarda kullanılır.
- ClearOutPorts+ClearAnalog: Hem dijital hem de analog çıkışları durduran, eksenleri devre dışı bırakan, motorları serbest bırakan ve takım yolunu ilk koordinata sıfırlayan kapsamlı bir acil durum modudur. Sistem çalışma durumunu tamamen sıfırlar.
- All: “All” seçildiğinde yukarıdaki tüm acil durum tepkileri etkinleştirilir; maksimum düzeyde sistem kapatma sağlanır.
2. Home Sensörleri
Home sensörleri, pozisyonların anlamlı hale gelmesini sağladıkları için son derece kritiktir. Bu sensörler sayesinde konumlar anlam kazanır, tablo boyutu tanımlanabilir hale gelir. Sensörler, makinenin sıfır noktası ya da orijin noktasını temsil eder. Eksen sensöre ulaştığında kontrol cihazı bunu algılar ve siyah ızgara (Grid) alanında kırmızı bir tablo oluşturur. Bu özellik sayesinde bu alanın içindeki her nokta, her eksendeki sensöre göre kendi konumuna sahip olur.
Gerçekte, home sensörleri CNC makinelerinin işlevi ve doğruluğu için ayrılmaz bir parçadır. Şimdi bu sensörlerin kontrol cihazıyla nasıl etkileşimde bulunduğunu ve makine çalışma alanını nasıl etkilediğini inceleyelim:
Home Sensörlerinin Rolü ve İşlevselliği:
-
Orijin Tanımı: Home sensörleri, makinenin sıfır noktası ya da orijinini belirler. Bu nokta, makinenin çalışma alanındaki tüm diğer konumlar için referans olarak hizmet eder. Tüm eksenler (genellikle X, Y ve Z olarak adlandırılır) için başlangıç noktası bu sensörler ile belirlenir.
-
Tablo Boyutu ve Çalışma Alanı Tanımı Üzerindeki Etkisi: Bu sensörler ile home pozisyonunun algılanması, makinenin tablo boyutunun tanımlanmasını doğrudan etkiler. Çünkü kontrol cihazı, bu orijin noktasını kullanarak makinenin operasyon alanının (çalışma tablasının) sınırlarını hesaplar. Makinenin hareketleri bu sınırlar içinde kalacak şekilde sınırlandırılır; bu da hem doğruluğu sağlar hem de makinenin kapasitesini aşacak şekilde hareket etmesini ve olası hasarları önler.
-
Kontrol Cihazı Arayüzünde Görselleştirme: Home sensörleri tetiklendiğinde, CNC kontrol cihazı bu durumu görsel olarak arayüzünde gösterebilir. Genellikle bu durum siyah bir ızgara üzerinde “kırmızı tablo” olarak resmedilir. Bu görsel, operatörlerin makinenin aktif çalışma alanını net bir şekilde görmesini sağlar. Takımların nerelerde güvenle hareket edip çalışabileceği belirlenmiş olur.
-
Pozisyonel Doğruluk: Bu kırmızı tablo içindeki her nokta, makinenin orijin noktasına göre özel bir konuma sahiptir. Her eksendeki home sensörleri sayesinde bu konumlar hassas şekilde hesaplanır. Böylece makinenin her hareketi, orijine göre tam olarak izlenebilir hale gelir ve yapılan tüm işlerin doğruluğu ve güvenilirliği artar.
-
Operasyonel Güvenilirlik: Makinenin orijin noktasını yeniden tanımlamak için home sensörlerinin düzenli olarak kullanılması, uzun vadeli tutarlı çıktı elde etmek açısından kritik öneme sahiptir. Özellikle hassasiyet gerektiren uygulamalarda doğruluğu ve güvenilirliği korur.
Genel olarak, home sensörleri yalnızca makinenin operasyon sınırlarını tanımlamakla kalmaz, aynı zamanda tüm işlemlerin belirli ve güvenilir bir referans noktasına göre yapılmasını sağlayarak doğruluğu ve güvenliği artırır. Bu yapı, çalışma alanındaki her noktanın orijine göre tam olarak konumlandırılmasını sağlar ve makinenin tüm işlevlerini öngörülebilir ve hassas hale getirir.
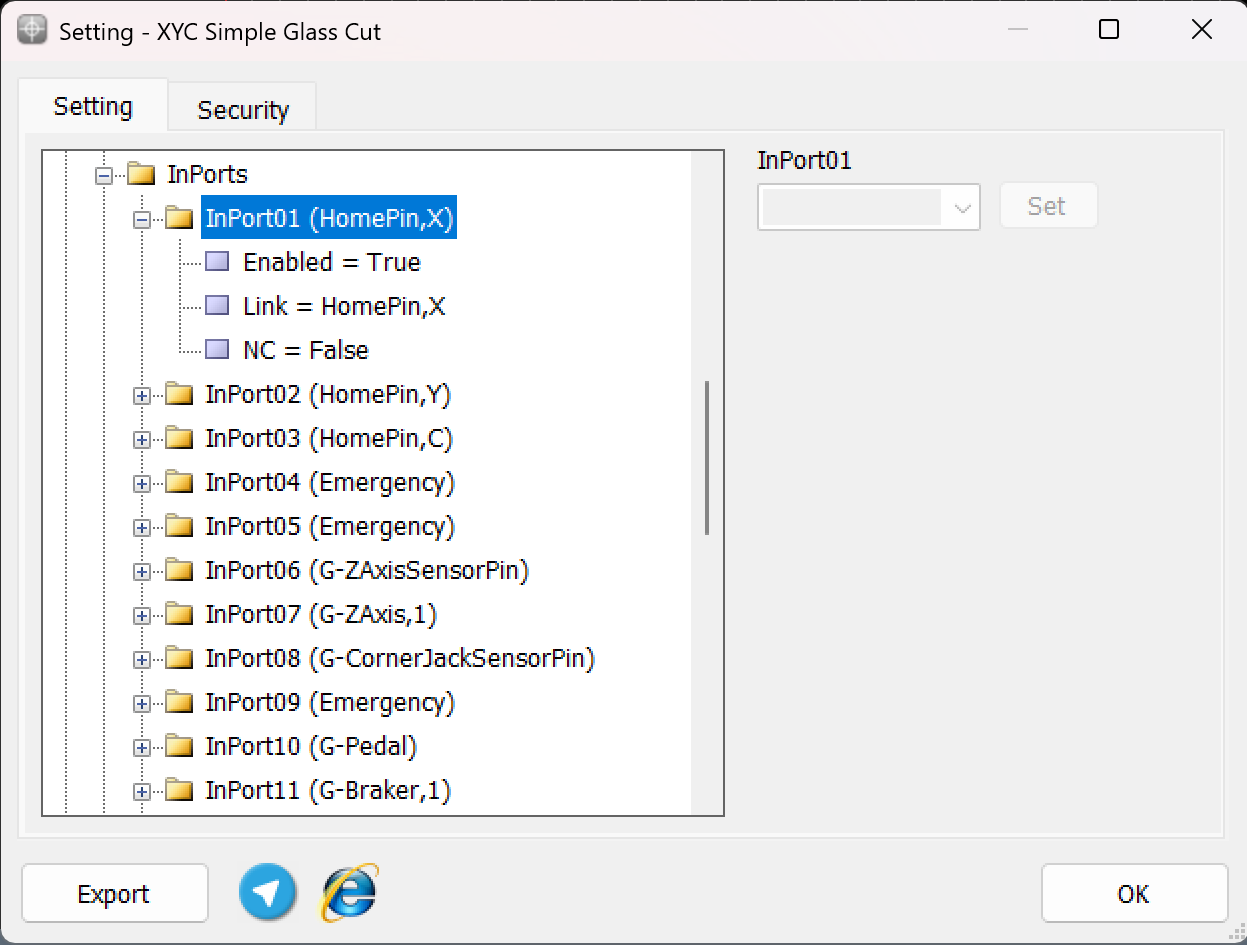
Eksen hareketinin Home komutu verildikten sonra hassas şekilde durmasını sağlamak için yukarıdaki açıklamada gösterildiği gibi uygun giriş bağlantıları yapılandırılmalıdır. Bu yapılandırma, her eksen için home konumunun doğru algılanmasını garanti eder.
Örneğin:
- Giriş HomePin,X, X ekseni home konumunu algılamak için atanır. Bu, X ekseni sensörü kendi home sensörü ile hizalandığında sistemin bunu home pozisyonu olarak tanımladığı anlamına gelir.
- Benzer şekilde, Y, C, Z gibi diğer eksenlerin de kendi sensör hizalamalarına göre HomePin,Y veya HomePin,C gibi giriş bağlantılarının doğru yapılandırılması gerekir.
Bu yapılandırılmış sistem sayesinde, her eksen home konumuna ulaştığında hareketi hassas şekilde durdurur ve homing işlemleri sırasında güvenli ve güvenilir çalışma sağlanır.
3. Kalibrasyon
Kalibrasyon Tanımı
Kalibrasyon, bir eksenin hareket değerinin standart birimlerden biriyle veya belirli bir değerle hizalanması sürecidir. Endüstriyel cihazlarda yaygın olarak kullanılan birimler genellikle milimetre, santimetre, metre, inç, feet, derece vb. olup ihtiyaca göre kullanılabilir. Bu nedenle, milimetre birimi için kalibrasyon kavramı, istenen eksenin hareket değerinin milimetre birimi ile hizalanması şeklinde ifade edilebilir. Yani ölçüm araçlarıyla ölçüm yapıldığında, eksenin hareketinin sayısal değeri ile milimetre cinsinden ölçülen değer birbiriyle tutarlı olmalıdır.
Kalibrasyonda Motor Tipleri
Radonix kontrol cihazlarında her eksen için kalibrasyon prosedürü motor tipine göre belirlenir. Farklı motor tipleriyle uyumluluğun sağlanması için temel gereklilik, seçilen motorun hem pulse (nabız) hem de direction (yön) sinyallerini desteklemesidir.
Servo motorlar
Bir servo motor, açısal veya doğrusal pozisyon, hız ve ivmenin hassas kontrolüne olanak tanıyan döner ya da doğrusal bir aktüatör türüdür. Genellikle pozisyon geri bildirimi sağlayan bir sensörle bağlantılı bir motor içerir. Servo motorlar, robotik, CNC makineleri ve otomatik üretim gibi hassas konumlandırmanın gerektiği uygulamalarda gereklidir. Geri besleme sinyalleri kullanarak hareket parametrelerini ayarlarlar ve performansı düzeltmek için hata algılama geri beslemesi kullanan servo mekanizmalar aracılığıyla kontrol edilirler.
Elektronik Şanzıman: Modern servo sistemlerinde özellikle otomasyon ve robotikte kullanılan servo motorları içeren uygulamalarda Elektronik Şanzıman temel bir bileşendir. Bu teknoloji, motorun hızını ve torkunu mekanik olarak değil, elektronik olarak ayarlayan sanal bir dişli kutusu gibi çalışır. Motorun giriş sinyallerinin frekansı ve genliği değiştirilerek, elektronik bir şanzıman motorun çıkış karakteristiklerini fiziksel bir dişli değişimine gerek kalmadan belirli görevler için ayarlayabilir.
Bir sonraki temel adım: Enkoder Çözünürlüğü
Enkoder Çözünürlüğü, servo motorların temel bir özelliğidir ve motor milinin tam bir devrinde enkoderin ürettiği darbe sayısını ifade eder. PPR (pulse per revolution – devir başına darbe) cinsinden belirtilen bu özellik, motorun pozisyonu, hızı ve ivmesinin ne kadar hassas kontrol edilebileceğini belirler.
Örneğin, Delta servo motorun B2 modeli, her devirde 160.000 darbe (PPR) üreten bir enkodere sahiptir. Aynı markanın A2 modeli ise 1.280.000 PPR gibi çok daha yüksek bir çözünürlük sunar. Bu yüksek çözünürlük, özellikle hassas pozisyonlama ve detaylı hareket kontrolü gerektiren uygulamalarda daha ince ayarlar yapılmasına olanak tanır.
Yüksek çözünürlüklü enkoderler, özellikle robotik, CNC makineleri ve otomatik montaj hatları gibi hassas hareketlerin hayati önem taşıdığı alanlarda son derece yararlıdır. Enkoder çözünürlüğü ne kadar yüksekse, tespit edilip kontrol edilebilecek hareket de o kadar küçük olur; bu da sistemin doğruluğunu ve çıktı kalitesini artırır. Bu kontrol yeteneği, yüksek hassasiyet gerektiren görevlerin performansını optimize etmek, her bileşenin sıkı toleranslar içinde çalışmasını sağlamak ve kalite standartlarına uymasını garanti etmek için kritiktir.
Enkoder çözünürlüğünü anlamak ve doğru şekilde ayarlamak, otomatik sistemlerin kalibrasyonunda atılması gereken ilk önemli adımdır. Bu, makinenin sorunsuz çalışmasını ve her bir parçanın kesin spesifikasyonlara uygun üretilmesini sağlayarak üretim hatalarını azaltır ve genel verimliliği artırır.
Servo Sürücülerde Elektronik Dişli Oranı (E.G.) Ayarı için Genel Kılavuz
Genel Bakış
Servo sürücülerde Elektronik Dişli Oranı (E.G.)’nın yapılandırılması, hassas hareket kontrolü gerektiren uygulamalarda performansı optimize etmek için kritiktir. Bu kılavuz, Delta B2 servo sürücü örneği üzerinden genel bir E.G. yapılandırma yaklaşımı sunar.
Gereklilikler
- Enkoder entegreli servo sürücü
- Darbe sinyalleri üretebilen kontrol cihazı (örneğin bir CNC kontrol cihazı)
- Servo sürücü ve kontrol cihazına ait teknik özellikler
Adım Adım Yapılandırma
Adım 1: Enkoder Çözünürlüğünü Anlayın
- Amaç: Servo motorun milinin tam bir dönüşü için gereken darbe sayısını tanımlayın.
- Genel Bilgi: Enkoder çözünürlüğü, devir başına darbe (PPR) olarak belirtilir. Bu değer, servo sürücünün motor pozisyonunu ne kadar hassas kontrol edebileceğini belirler.
Adım 2: Motor Hızını Saniye Başına Devir (RPS) Cinsine Çevirin
- Amaç: Kontrol cihazının çıkış frekansıyla uyumlu olması için istenen motor hızını RPM’den (dakika başına devir) RPS’ye (saniye başına devir) dönüştürün.
- Yöntem:
- Formül: RPS = RPM / 60
Adım 3: Gerekli Darbe Sayısını Hesaplayın (Pulses per Second)
- Amaç: RPS ve enkoder çözünürlüğüne göre gerekli toplam darbe sayısını saniyede hesaplayın.
- Yöntem:
- Formül: Darbe/saniye = RPS × Enkoder Çözünürlüğü
Adım 4: Elektronik Dişli Oranını (E.G.) Ayarlayın
-
Amaç: Kontrol cihazının çıkışının, servo motorun darbe ihtiyacını karşılayabilmesi için elektronik dişlileme oranını ayarlayın.
-
Yöntem:
E.G. = Gerekli Darbe / Kontrol Cihazı Darbe Kapasitesi
-
Kontrol cihazı ayarlarını hesaplanan E.G. oranıyla eşleştirin.
Örnek: Delta B2 Servo Sürücü
- Motor Hızı: 3000 RPM
- Enkoder Çözünürlüğü: 160.000 PPR
- Kontrol Cihazı Darbe Kapasitesi: 500.000 darbe/saniye
- Hesaplama:
- RPS = 3000 / 60 = 50
- Gerekli Darbe = 50 × 160.000 = 8.000.000
- E.G. = 8.000.000 / 500.000 = 16
- Ayar: E.G. oranı = 16:1
Test ve Doğrulama
- Amaç: Yeni ayarlarda servo sistemin doğru çalıştığından emin olun.
- Yöntem:
- Test çalışması yaparak servo sürücünün doğruluğunu ve tepkisini gözlemleyin.
- Hareketin beklendiği parametrelerle uyumlu olup olmadığını kontrol edin.
Ek Notlar
- Ayrıntılı teknik bilgiler ve gelişmiş ayarlar için ilgili servo sürücü kılavuzlarına başvurun.
- Optimum performansı sürdürmek için düzenli bakım ve yeniden kalibrasyon önerilir.
Bu kapsamlı yaklaşım, çeşitli tipteki servo sürücülerin otomasyon ve robotik gibi yüksek hassasiyet gerektiren sistemlere verimli şekilde entegre edilmesini ve çalıştırılmasını sağlar.
Step motorlar
Step motor, elektriksel darbeleri belirli mekanik hareketlere dönüştüren elektromekanik bir cihazdır. Elektromanyetizma prensibine göre çalışır; sabit adım artışlarıyla döner ve bu sayede hassas hareket ve konumlandırma elde edilir. Bu özellik, step motorları 3D yazıcılar, CNC makineleri ve robotik gibi son derece hassas ve kontrollü hareketler gerektiren uygulamalar için ideal hale getirir. Step motorlar, kısa mesafeli veya sınırlı açılı uygulamalarda hassas kontrol gerektiren sistemlerde, genellikle açık çevrim kontrol sistemlerinde tercih edilir.
Step motor sürücüler genellikle motor çalışmasını ayarlamak için kullanıcıların belirli ayarları yapılandırabilmesine olanak tanıyan DIP (Çift Hatlı Paket) anahtarları içerir. Bu anahtarlar, step motorun performansını belirli bir uygulamanın ihtiyaçlarına göre uyarlamak açısından kritiktir. Aşağıda, bir step motor sürücüsünde DIP anahtarları ile kontrol edilebilecek yaygın ayarların bir dökümü verilmiştir:
Step Motor Sürücülerindeki Yaygın DIP Anahtarı Ayarları:
- Microstepping (Mikroadımlama):
- Mikroadımlama, step motorların daha küçük adımlarla hareket etmesini sağlayan bir kontrol yöntemidir. Bu, daha pürüzsüz hareket ve daha yüksek çözünürlükte konumlandırma sağlar. DIP anahtarları, tam adım, yarım adım, çeyrek adım vb. farklı mikroadımlama konfigürasyonlarını ayarlamak için kullanılır.
- Akım Ayarı:
- Performans ve verimliliği optimize etmek için, step motora verilen akım DIP anahtarlarıyla ayarlanabilir. Bu, motorun özelliklerine uygun akımı sağlayarak yetersiz performans veya aşırı ısınmayı önler.
- Decay Modu:
- Decay modu, motorun off çevrimdeki akımının ne kadar hızlı azaldığını kontrol eder. Uygun decay ayarları, özellikle yüksek hızlarda veya değişken yüklerde motor performansını ve tepki süresini iyileştirebilir.
- Tork Ayarları:
- Bazı sürücüler, motorun çıkış torkunu DIP anahtarlarıyla ayarlamaya izin verir. Bu ayar, motorun çalışması sırasında farklı yükler veya basınçların beklendiği durumlar için kritiktir.
DIP Anahtarları Nasıl Kullanılır?
- Kılavuza Başvurun: Her zaman step motor sürücüsünün kılavuzunu inceleyin; her DIP anahtarının neyi kontrol ettiğine dair talimatlar burada bulunur. Bu, ihtiyaçlarınıza göre doğru ayarları yapmak için hayati öneme sahiptir.
- Güç Vermeden Önce Ayarlayın: DIP anahtarları, sürücü kapalıyken ayarlanmalıdır; aksi halde motor veya sürücü zarar görebilir.
- Test ve Ayarlama: DIP anahtarlarını ayarladıktan sonra, motorun yük altında beklendiği şekilde çalışıp çalışmadığını test edin. Gerekirse istenen performansa ulaşmak için ayarları yeniden yapın.
Step motor sürücüsündeki en yüksek mikroadımlama değeriyle DIP anahtarlarının ayarlanması, uzmanlar tarafından genellikle motorun mümkün olan en pürüzsüz hareketi sağlaması açısından önerilmektedir. Bu uygulama, özellikle yüksek hassasiyetin ve yumuşaklığın önemli olduğu yüksek hassasiyetli işleme, robotik veya medikal ekipman gibi uygulamalarda yaygındır. Aşağıda bu önerinin neden yaygın olduğu ve nasıl etkili biçimde uygulanabileceği açıklanmıştır:
Neden En Yüksek Mikroadımlama Değeri Seçilmeli?
- Daha Yüksek Çözünürlük ve Pürüzsüzlük:
- Yüksek mikroadımlama değerleri, motorun bir tam dönüşü tamamlaması için gereken adım sayısını artırır. Bu da daha küçük adım aralıkları ile hareketi yumuşatır, daha düşük mikroadımlama ayarlarında belirginleşen titreşim ve rezonansı azaltır.
- Azaltılmış Mekanik Gürültü:
- Daha küçük adım aralıkları daha sessiz çalışmaya katkı sağlar. Adımlar arasındaki geçişin daha pürüzsüz olması, step motorların ani hareketlerinde oluşan sesi azaltır; bu da gürültü hassasiyeti olan ortamlarda faydalıdır.
- Geliştirilmiş Konumsal Doğruluk:
- Mikroadımlama çözünürlüğü artırır; ancak bu, adım hatalarının zamanla birikmesi nedeniyle her zaman mutlak pozisyon doğruluğunu artırmaz. Yine de pratik uygulamalarda daha ince adımlar, motorun konumlandırılması üzerinde daha hassas kontrol sağlar; bu da hassas işlemler için kritik öneme sahiptir.
Kalibrasyon Yöntemleri
Radonix kontrol cihazında her eksen ayrı ayrı kalibre edilebilir ve hatta eksenler farklı birimlerde kalibre edilebilir. Bu kontrol cihazında kalibrasyon faktörünü temsil eden değişken Step değişkenidir ve bu değere erişmek için Radonix yazılımını açmalı, ardından Ayarlar penceresini açıp System dalına ve sonra Axis"N" alt dalına gitmelisiniz (buradaki "N", eksen numarasını temsil eden 1 ila 6 arasındaki bir sayıdır).
Artık bu E.G. kalibrasyon süreci iki şekilde gerçekleştirilebilir:
1. Radonix CAM Kalibratör ve Ölçüm
Bu kalibrasyon yönteminde temel, ölçüm aletleri ve ekipmanları ile yapılan fiziksel ölçüme dayanır. Bu nedenle ölçüm aracının doğruluğu, ölçüm hassasiyeti ve cihazın mekanik hataları kalibrasyon kalitesini doğrudan etkiler. Bu yöntem, motorlar, şanzımanlar, kasnaklar ve dişliler hakkında yeterli bilgiye sahip olunmayan durumlarda oldukça yaygın bir şekilde kullanılır. Temel prensip, belirli sayıda darbe için eksen yer değiştirmesinin ölçülmesidir.
Bu ölçüm yönteminin doğruluğunu ve hızını artırmak için, Radonix tarafından CAM-Pro Calibrator adlı ücretsiz bir yazılım sunulmuştur. Bu yazılım, Radonix’in ana yazılımı ile birlikte otomatik olarak yüklenir. Eksenin fiziksel yer değiştirme miktarı ve bu yer değiştirme için gereken darbe sayısı temel alınarak yazılım step değerini hesaplar.
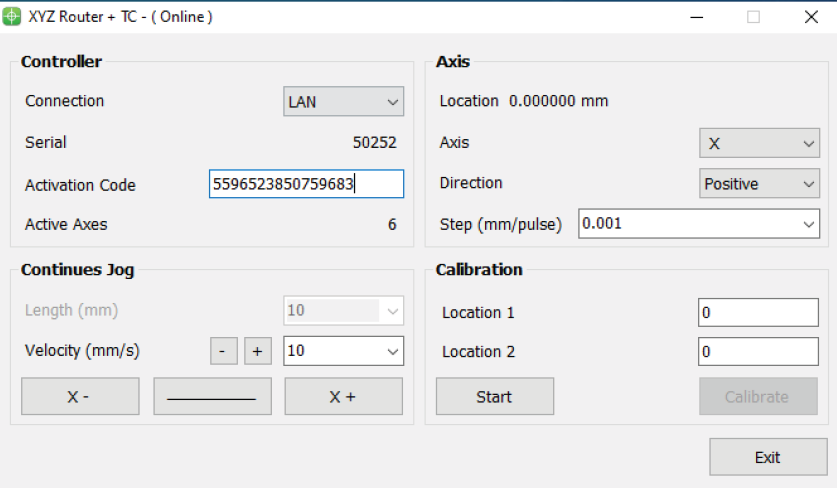
Bu yöntemde darbe sayımı kontrol cihazı tarafından yapıldığından, darbe ölçümünde hata yoktur. Bu nedenle, ölçüm doğruluğu doğrudan fiziksel ölçüm doğruluğuna bağlıdır. Ayrıca, iki ölçüm noktası arasındaki mesafe ne kadar büyükse, darbe değeri de o kadar büyük olur; bu da paydayı artırır ve sabit hata dikkate alındığında, elde edilen step değeri daha doğru olur. Bu nedenle iki nokta üzerinden yapılan kalibrasyon daha hassas sonuçlar verir.
CAM-Pro Calibrator Tanıtımı
Yukarıda açıklandığı gibi, CAM-Pro Calibrator yazılımı CAM-Pro ile birlikte kurulur. Yazılımı kurduktan sonra bulmanın iki yolu vardır. Birinci yönteme göre, yazılımın kurulum konumuna (varsayılan olarak C sürücüsünde) gidin, ardından (x86) Program Files klasörünü açın, Radonix klasörünü bulun ve CAMProCalibrator yazılımı bu dizin içinde bulunur. İkinci yöntemle, Başlat menüsüne gidip arama kutusuna “Radonix CAM-Pro Calibrator” yazın.
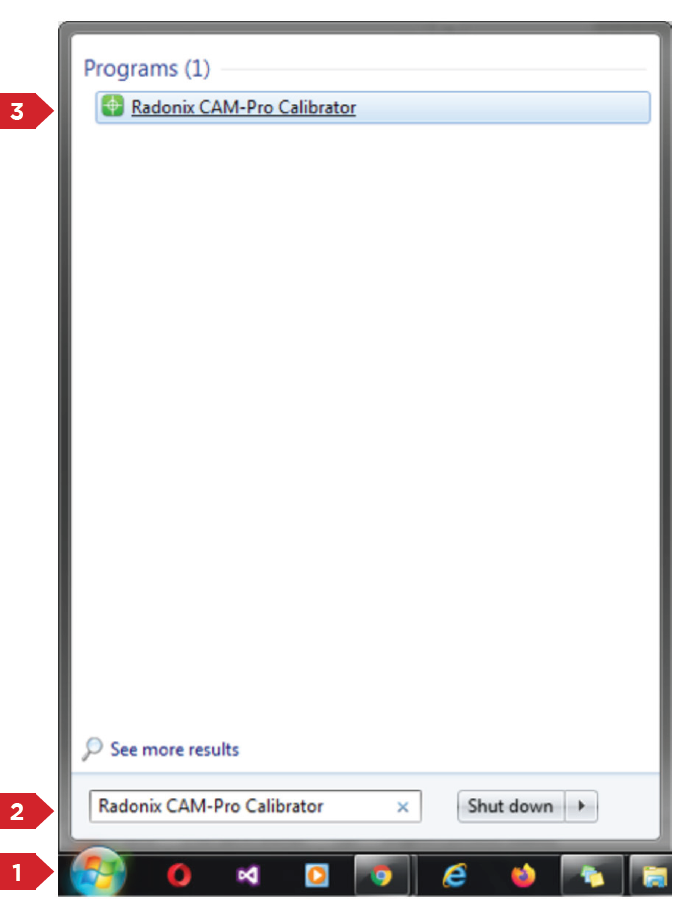
Bu program iki pencereden oluşur. İlk pencere yalnızca bilgisayarda birden fazla aktif arayüz varsa görünür (Şekil 3). Bu pencerede istenen arayüzü seçebilir ve 'Ok' butonuna basarak başlatabilirsiniz. Bilgisayarda yalnızca bir aktif arayüz varsa bu pencere açılmaz, doğrudan ana pencere açılır.
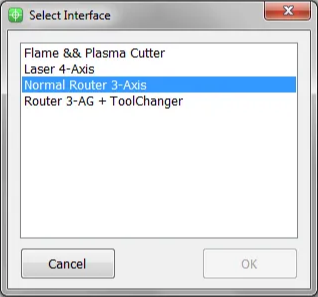
CAM-Pro Calibrator yazılımı açıldığında Şekil (4) ekranı görünür ve bu ekranın bileşenleri şunlardır:
1. Connection (Bağlantı):
- ProLAN kontrol cihazları için bağlantı modu LAN olarak ayarlanmalıdır.
- ProUSB kontrol cihazları için bağlantı modu USB olarak ayarlanmalıdır.
2. Serial (Seri):
- Kontrol cihazının seri numarasını gösterir.
3. Activation Code (Aktivasyon Kodu):
- Eksenleri etkinleştirmek için kullanılan 16 haneli aktivasyon kodunu görüntüler.
4. Active Axes (Aktif Eksenler):
- Aktivasyon kodu ile etkinleştirilmiş eksen sayısını gösterir.
Eksen Bölümü
5. Axis (Eksen):
- Kalibrasyon için istenen ekseni seçmenizi sağlar.
6. Direction (Yön):
- Standart eksenler için uygun hareket yönünü seçmenizi sağlar:
- Negative (Negatif): Negatif yöne doğru hareket.
- Positive (Pozitif): Pozitif yöne doğru hareket.
7. Step (Adım):
- Kalibrasyon veya çıkış darbeleri için step (adım) büyüklüğünü ayarlar. Kalibrasyondan sonra, bu değer ayarlara otomatik olarak kaydedilir.
Sürekli Jog Bölümü
8. Negative Jog (Negatif Jog):
- Eksenin negatif yönüne manuel hareketi etkinleştirir.
9. Jog Mode (Jog Modu):
- Jog hareket türünü seçmenizi sağlar:
- Continuous (Sürekli): Kesintisiz, akıcı hareket.
- Incremental (Adımlı): Belirlenen miktarlarda adım adım hareket.
10. Positive Jog (Pozitif Jog):
- Eksenin pozitif yönüne manuel hareketi etkinleştirir.
11. Length (Uzunluk):
- Incremental (Adımlı) mod aktifken, adım adım hareketlerde geçilecek mesafeyi tanımlar.
Hız Bölümü
12. Velocity (Hız):
- Manuel hareketler için hız ayarı yapmakta kullanılır.
- Velocity seçeneğinin yanındaki artı ve eksi butonları, manuel hareketin hızını artırır veya azaltır.
Kalibrasyon Bölümü
13. Start (Başlat):
- Kalibrasyon sürecini başlatmak için buton.
14. Location 1 (Konum 1):
- Kalibrasyon için ilk pozisyonu belirlemek amacıyla kullanılır.
- Bu pozisyon, ölçülen eksen üzerindeki sabit bir referans noktasına göre ayarlanmalıdır.
15. Location 2 (Konum 2):
- Kalibrasyon için son pozisyonu belirlemek amacıyla kullanılır.
- Bu pozisyon da ölçülen eksen üzerindeki sabit bir referans noktasına göre ayarlanmalıdır.
16. Calibrate (Kalibrasyon):
- Kalibrasyon sürecini tamamlamak ve kalibrasyon katsayısını hesaplamak için buton.
17. Exit (Çıkış):
- Kalibrasyon programından çıkmak için buton.
Kalibrasyon yazılımı özeti – şu adımları izleyin:
Önce, kalibrasyon için Eksen bölümünden istenilen ekseni seçin. Ardından düşük bir hız seçip ekseni hareket ettirerek hareket yönünün doğru olduğundan emin olun. Eğer hareket yönü yanlışsa, Yön bölümünü kullanarak uygun yönü seçin. Sonra ekseni hareket aralığının uç noktalarından birine götürün. Bu yöntemde başlangıç yönü önemli olmadığından, eksenin hangi ucu başlangıç olarak seçildiği fark etmez. Eksen doğru konumdayken, eksen üzerindeki bir noktayı makinedeki sabit bir noktaya göre uygun bir ölçüm aracıyla ölçün, bunu Location 1'e kaydedin ve Start butonuna basın.
Birim seçimi tamamen opsiyoneldir; eğer belirli bir birimde kalibrasyon yapılması isteniyorsa, tüm ölçümler o birime göre yapılmalıdır. Örneğin; cihaz inç, metre, santimetre, milimetre hatta mikrometre cinsinden kalibre edilebilir.
Eksenin karşı uç noktasına hareket edin. Eğer daha büyük mesafeler ölçülebiliyorsa ve ölçüm aracı yeterince hassassa, daha uzun mesafelerde yapılan ölçümler daha hassas sonuçlar verecektir. İkinci noktaya ulaşıldığında, bu noktayı da makinenin sabit referans noktasına göre birinciyle aynı şekilde ölçün, Location 2'ye kaydedin ve ardından Calibrate butonuna basın. Bu ölçümlere dayanarak kalibrasyon adımı ya da katsayısı hesaplanır ve otomatik olarak arayüze kaydedilir. Bu kalibrasyon işlemi, her eksen için gerektiği kadar tekrarlanabilir.
Not: CAM-Pro Calibrator yazılımı açıldığında, eğer aktivasyon kodu girilmemişse bir hata mesajı görüntülenir.
2. Matematiksel Hesaplama
Hesaplamalı Yöntem
Eksen hareketini istenen birimle hizalamak için "Step" adlı bir kalibrasyon katsayısı kullanılır. Bu değişkene erişmek için önce yazılımı açın, ardından Ayarlar penceresine gidin, Sistem dalına ve eksen numarasını temsil eden Axis"N" alt dalına (buradaki "N", 1 ile 6 arasında bir sayı) ilerleyin. Step değişkeni bu alt dallar içinde yer alır ve her eksenin kendine ait özel bir Step değişkeni bulunur.
Eğer eksen hareketinin birimi milimetre cinsindense, bu değişkenin birimi de darbe başına milimetre olur. Eğer birim santimetre, inç veya başka bir birimse, Step değişkeni de bu birim cinsinden ifade edilir. Esasen bu değer, o eksenin motor sürücüsüne gönderilen her bir darbe için gerçekleşen hareket miktarını temsil eder. Bu nedenle bu değeri hesaplamak için, motor sürücüsüne gönderilen her bir darbenin motor şaftına olan etkisini ve varsa şanzıman, kasnak ya da diğer aktarma sistemlerinin dönüşüm oranlarını bilmek gerekir.
Aşağıda bu hesaplamaların daha iyi anlaşılabilmesi için örnekler verilmiştir:
Örnek 1:
Bir CNC makinesinin doğrusal eksenini düşünün; ölçüm birimi milimetredir ve 10:1 şanzıman oranına sahip Panasonic A5 motorlarla donatılmıştır. Bu motor, çapı 66 mm olan bir pinyon aracılığıyla bir kremayer raya bağlıdır. Şimdi, belirtilen eksen için Step değerini hesaplayın.
Not: Her bir bilgi bu hesaplamalarda kritik rol oynar ve kalibrasyon amacıyla step büyüklüğünü belirlemek için kullanılabilir. Örneğin, kullanılan motor sürücüsünün tipi ve teknik özellikleri, sürücüye gönderilen darbenin motor şaftındaki hareketle olan ilişkisini belirler.
Panasonic A5 motorlarında, saniyede 500.000 darbe verildiğinde motor 3000 rpm hıza ulaşır. İlk adımda, motorun saniyedeki dönüş sayısı hesaplanır:
Motor devir hızı (r/s) = 3000 rpm / 60 = 50 r/s
İkinci adımda, motorun 1 turunda eksenin ne kadar hareket ettiğini bulmamız gerekir.
Bu örnekte, kat edilen mesafe bir çemberin çevresi kadar olacaktır. Çemberin çevresi, çap × π (yaklaşık 3.1415) ile hesaplanır.
66 mm çaplı pinyon ve 10:1 şanzıman kullanıldığına göre:
Eksen hareketi = (1/10) × 66 × 3.1415 = 20.7339 mm
Son adımda, Step değişkeni için nihai formül yazılır. Gördüğümüz gibi, 500.000 darbe/saniye ve 3000 rpm esas alınmaktadır.
1 pulse başına hareket miktarı = 50 × 20.7339 / 500.000 = 0.00207339 mm/pulse

Bu formülden Step değeri elde edilir. Bu, motorun aldığı her 1 darbe için 0.0207339 mm hareket ettiği anlamına gelir.
Not: Bu hesaplamalı yöntem, doğrusal eksenlerin kalibrasyonu için kullanılır.
Genel formül:
Step (birim/darbe) = (1 devirdeki eksen hareketi) × (saniyedeki motor devri) / (saniyedeki darbe sayısı)
Örnek 2:
Bir CNC makinesinin döner eksenini düşünün; ölçüm birimi derece. 25:1 şanzımanlı Panasonic A5 motorlar ve 12 dişli bir kasnak kullanılıyor. Bu kasnak bir kayış ile 44 dişli başka bir kasnağa bağlı. Şimdi bu eksen için Step değeri hesaplayın.
Motor devri: 3000 rpm / 60 = 50 r/s
Step = 50 × (1/25) × (12/44) × 360 / 500.000 = 0.000392727272
Buradan Step değeri elde edilir.
Döner eksenler için genel formül:
Step (birim/darbe) = (saniyedeki motor dönüşü) × (etkin oran) × 360 / saniyedeki darbe sayısı
Not:
Gerek doğrusal gerek döner eksenlerde, daha fazla ondalıklı basamak kullanıldıkça hesaplama doğruluğu artar.Not: Step motorlardaki darbe bölünmeleri bu hesaplamaları doğrudan etkiler. Hesabı basitleştirmek için önce belirli bir darbe değeri için motor dönüşü hesaplanıp, bu sonuç yukarıdaki denklemlere yerleştirilebilir.
Not: Sürücüde maksimum motor hızına ulaşmak için gereken darbe sayısı kontrol cihazının ürettiği darbeleri aşıyorsa, elektronik dişli oranı artırılarak bu hız elde edilebilir. Örneğin, bir sürücü 4 milyon darbe/saniye isterken, Radonix 500.000 darbe/saniye üretebiliyorsa, 8:1 oranındaki bir elektronik dişli oranı bu farkı telafi eder.
4. G-ZAxis
CNC cam kesme makinelerinde, Z ekseni hareketi genellikle operatörler tarafından krikolar (jacks) kullanılarak manuel olarak kontrol edilir. Bu durum, genellikle G-code programlamasında otomatik olarak kontrol edilen X, Y ve C eksenlerinden farklıdır. Bu manuel kontrol, hassas çalışma ve güvenliği sağlamak amacıyla makinenin sisteminde belirli yapılandırmaları içerir. İşte bu sistemin nasıl çalıştığının ve süreçte yağ kullanılmasının nedenlerinin ayrıntılı açıklaması:
Z Ekseninin Manuel Kontrolü
- Giriş Yapılandırması:
- Z ekseni boyunca hareketi başlatmak için bir giriş ayarı gereklidir. Bu genellikle makinenin arayüzünde
Inports
dalı altındaG-ZAxis,1
gibi bir tanımla ayarlanır. - Bu girişe bağlı bir arayüz düğmesi, Z ekseninin aşağı doğru hareketini kontrol etmek için kullanılır. Bu düğme genellikle bir geçiş anahtarı (toggle) olarak çalışır ve bu düğmeye bağlı işlevi erişmek için belirli bir tuş kombinasyonu gerekebilir (örneğin Ctrl + Shift + Alt + Sağ Tık).
- Z ekseni boyunca hareketi başlatmak için bir giriş ayarı gereklidir. Bu genellikle makinenin arayüzünde
- Çıkış Bağlantısı:
- Z ekseni motorunu etkinleştiren çıkış, örneğin
G-ZAxisPin
gibi tanımlanır. Böylece operatör kontrolü etkinleştirdiğinde motor devreye girer ve Z ekseni komutlandığı şekilde hareket eder. - Aynı anda, yağ çıkışı otomatik olarak aktif hale gelir ve hareketi yağlayarak hasarı önler, sorunsuz bir çalışma sağlar.
- Z ekseni motorunu etkinleştiren çıkış, örneğin
CNC Cam Kesiminde Yağın Önemi
Yağ, CNC cam kesme sürecinde aşağıdaki nedenlerden dolayı hayati rol oynar:
- Yağlama: Kesici alet ile cam arasındaki sürtünmeyi azaltır, yontulma veya çatlama riskini düşürür.
- Soğutma: Kesme sırasında oluşan ısıyı dağıtarak hem aleti hem de camı aşırı ısınmaya karşı korur.
- Kesim Kalitesi: Daha temiz ve hassas bir kesim sağlar, yüzey bitişini iyileştirir ve kusurları azaltır.
- Alet Koruması: Kesici aletin aşınmasını azaltarak kullanım ömrünü uzatır.
- Toz Azaltma: Kesme sırasında oluşan cam tozlarını bağlar, bu hem sağlık hem de mekanik bütünlük açısından faydalıdır.
Özelleştirme ve Güvenlik Özellikleri
- Özelleştirilebilirlik: Makine varsayılan kurulumla gelir ancak uzmanlar, belirli operasyonel ihtiyaçlara ve tercihlere göre arayüzü ve kontrolleri özelleştirebilir.
- Güvenlik ve Sensörler: Sistem, güvenlik özellikleri ve home sensörler için çeşitli girişleri içerir. Bu girişler, makinenin güvenli sınırlar içinde çalışmasını ve home pozisyonlarına doğru şekilde dönmesini sağlar.
Bu ayarlar ve CNC cam kesiminde yağ kullanımı, manuel kontrol, makine hassasiyeti ve operasyonel güvenlik arasındaki hassas dengeyi vurgular. Bu da zorlu endüstriyel ortamlarda optimum performans ve dayanıklılık sağlar.
5. Braker
CNC cam kesim makinelerinde, cam levhaların ayrılmasını kolaylaştırmak için özel ekipmanlar entegre edilmiştir. Bu araçlar, elmas kesici aletle inceltilmiş veya çizilmiş bölgelere, camın altından kontrollü basınç uygulayarak ayrılmasını sağlar. Bu işlem, camın çizgi boyunca temiz şekilde ayrılmasını ve geri kalan kısmında istenmeyen çatlakların veya hasarın oluşmamasını sağlar. Bu kontrollü ayırma tekniği, özellikle karmaşık tasarımlar veya dar toleranslar gerektiren uygulamalarda yüksek hassasiyet ve camın yapısal bütünlüğünü korumak açısından kritiktir.
Bu amaçla CNC cam kesim makinelerinde breaker (ayırıcı) sayısı dikkatle değerlendirilmelidir. Tipik olarak üç adet breaker, ayırma işlemini etkili şekilde gerçekleştirmek için kurulur. Her bir breaker, çalıştırma komutlarını almak için özel giriş bağlantılarına, bu komutları yürütmek için de çıkış bağlantılarına ihtiyaç duyar.
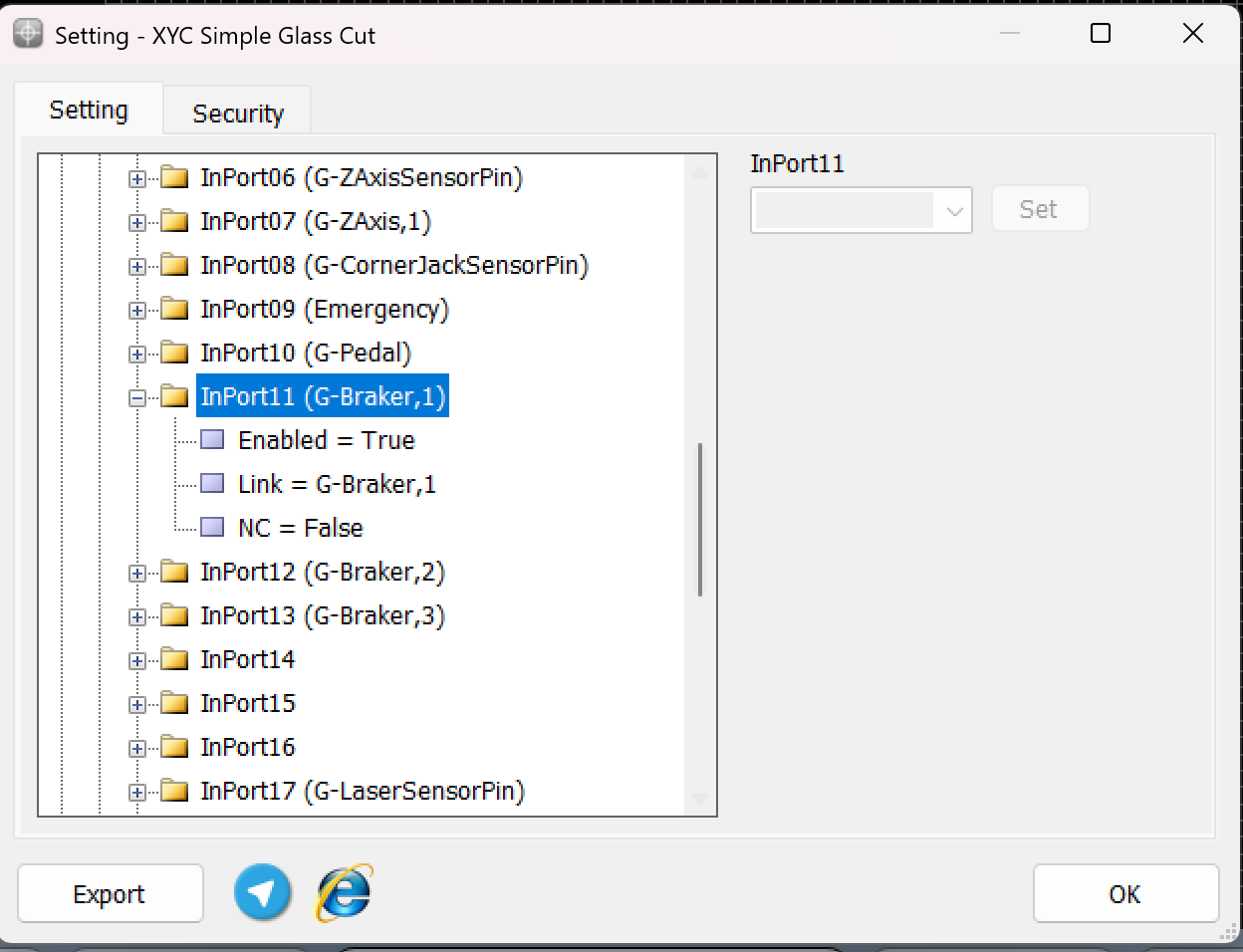
Yukarıdaki açıklamada gösterildiği gibi, bu görev için uygun bağlantı G-Braker,n formatındadır; burada n = 1, 2, 3 her bir breaker’ı temsil eder. Bu giriş bağlantıları genellikle kontrol kutusundaki basmalı düğmelere bağlanır, manuel kullanım için. Alternatif olarak, bu bağlantılar uzaktan kumanda, el çarkı (handwheel) veya hatta klavye gibi daha esnek ve gelişmiş kontrol seçeneklerine atanabilir.
Bu yapılandırma, operatörlerin breaker’lara komutları kolaylıkla vermesini sağlar ve farklı operasyonel senaryolara uyum sağlanmasına olanak tanır. Bu girişlerin çeşitli cihazlara bağlanabilme esnekliği, kullanıcı konforunu ve CNC cam kesim makinelerindeki operasyonel verimliliği artırır.
Diğer tarafta, breaker’ları kontrol etmek için çıkışlar G-BrakerPin,n formatında yapılandırılmalıdır. Buradaki "n", ilgili breaker’ı temsil eder (1, 2 veya 3).
Örneğin:
- G-BrakerPin,1: Birinci breaker’ı kontrol eder.
- G-BrakerPin,2: İkinci breaker’ı kontrol eder.
- G-BrakerPin,3: Üçüncü breaker’ı kontrol eder.
Bu çıkışlar doğru şekilde atandığında, sistem her breaker’ı ayrı ayrı yönetebilir. Bu da camın ayrılma sürecinin hassas ve etkili bir şekilde yürütülmesini sağlar. Bu yapılandırılmış yaklaşım, CNC cam kesim operasyonlarında senkronizasyonun korunması ve yüksek kalite sonuçların elde edilmesi açısından kritiktir.
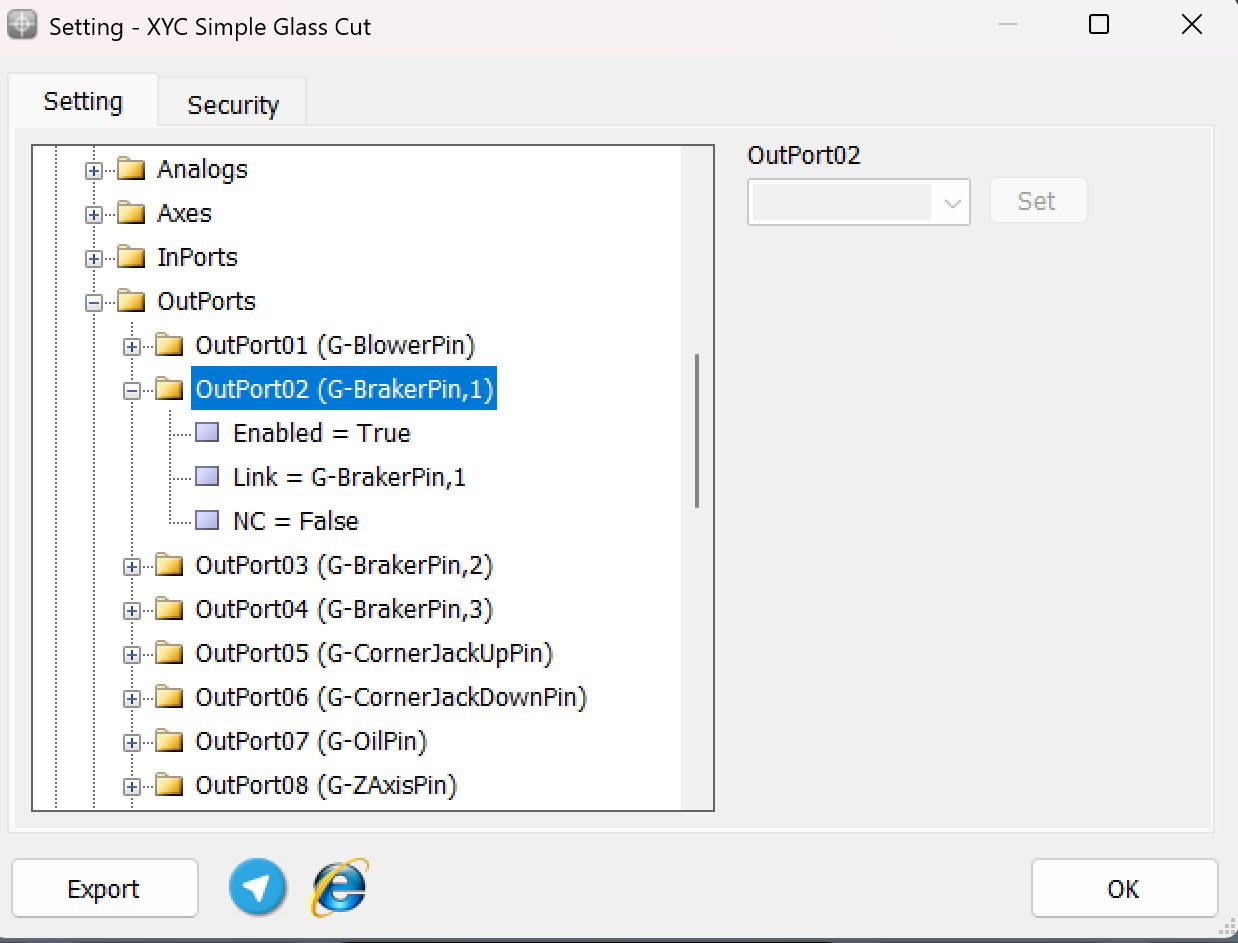
6. Oil (Yağ)
CNC Cam Kesiminde Yağın Önemi
Yağ, CNC cam kesme sürecinde şu nedenlerle hayati öneme sahiptir:
- Yağlama: Kesici alet ile cam arasında sürtünmeyi azaltır, çatlama veya kenar yontulmalarını önler.
- Soğutma: Kesim sırasında oluşan ısıyı dağıtarak hem aleti hem de camı aşırı ısınmaya karşı korur.
- Kesim Kalitesi: Daha temiz ve hassas kesim sağlar, bitiş kalitesini artırır.
- Alet Koruması: Kesici aletin aşınmasını azaltarak kullanım ömrünü uzatır.
- Toz Azaltma: Yağ, kesim sırasında oluşan cam tozlarını bağlar; bu hem sağlık hem de makine için faydalıdır.

Yağ Kontrolü için Çıkış Yapılandırması
Yağ kontrol çıkışı, çıkış bağlantılarında G-OilPin
formatında yapılandırılmalıdır. Bu, sistemin yağ çıkışını gerektiğinde açıp kapatabilmesini sağlar.
G-OilPin
doğru şekilde yapılandırıldığında:
- Makine, CNC işlemi sırasında yağ akışını hassas bir şekilde kontrol edebilir.
- Bu yapılandırma, genel kontrol sistemiyle sorunsuz entegrasyon sağlar ve yağ aktivasyonunun belirli komutlarla verimli bir şekilde tetiklenmesini sağlar.
7. Jack Corner Pin
Köşe hizalama aparatı (squaring tool), CNC cam kesme makinelerinde cam levhayı makine tablası üzerinde doğru şekilde hizalamak ve konumlandırmak için tasarlanmış temel bir bileşendir. Bu aparat, kesim hassasiyetini sağlamak ve operatörün camı doğru açı ve pozisyonda yerleştirmesine yardımcı olmak için kullanılır.
CNC Cam Makinelerinde Köşe Aparatının Kullanım Alanları
-
Cam Hizalama:
Köşe hizalama aparatı, cam levhayı hizalamak için bir referans noktası görevi görür. Doğru hizalama, hassas ve temiz kesimleri garanti eder.
-
Camın Sabitlenmesi:
Vakum kelepçeleri veya krikolar gibi diğer tutucu araçlarla birlikte köşe aparatı, kesim sırasında cam levhayı sabit tutar ve istenmeyen hareketleri önler.
-
Manuel ve Otomatik Kullanım:
Köşe aparatı, operatör tarafından manuel olarak veya tablanın altından yukarı çıkan ayarlanabilir krikolar ile otomatik olarak çalıştırılabilir.
-
Yazılım Entegrasyonu:
Gelişmiş CNC makinelerinde, köşe aparatının konumu makinenin yazılımına entegre edilmiştir. Bu sayede Otomatik Hizalama (Auto Align) veya Manuel Hizalama gibi özellikler, köşe aparatının konumuna göre kesim yolunu hassas şekilde ayarlayabilir.
Avantajları
- Kesim hassasiyetini artırır.
- Yanlış hizalanmış camlardan kaynaklanan hataları azaltır.
- Operatör için hizalama sürecini basitleştirir.
- Nihai kesim parçalarının kalitesini yükseltir.
G-Cornerjacksensorpin
Bu giriş, tabla üzerindeki köşe jack sensörü içindir. Bu giriş aktif hale geldiğinde, köşe jack’inin açık mı kapalı mı olduğunu belirler.
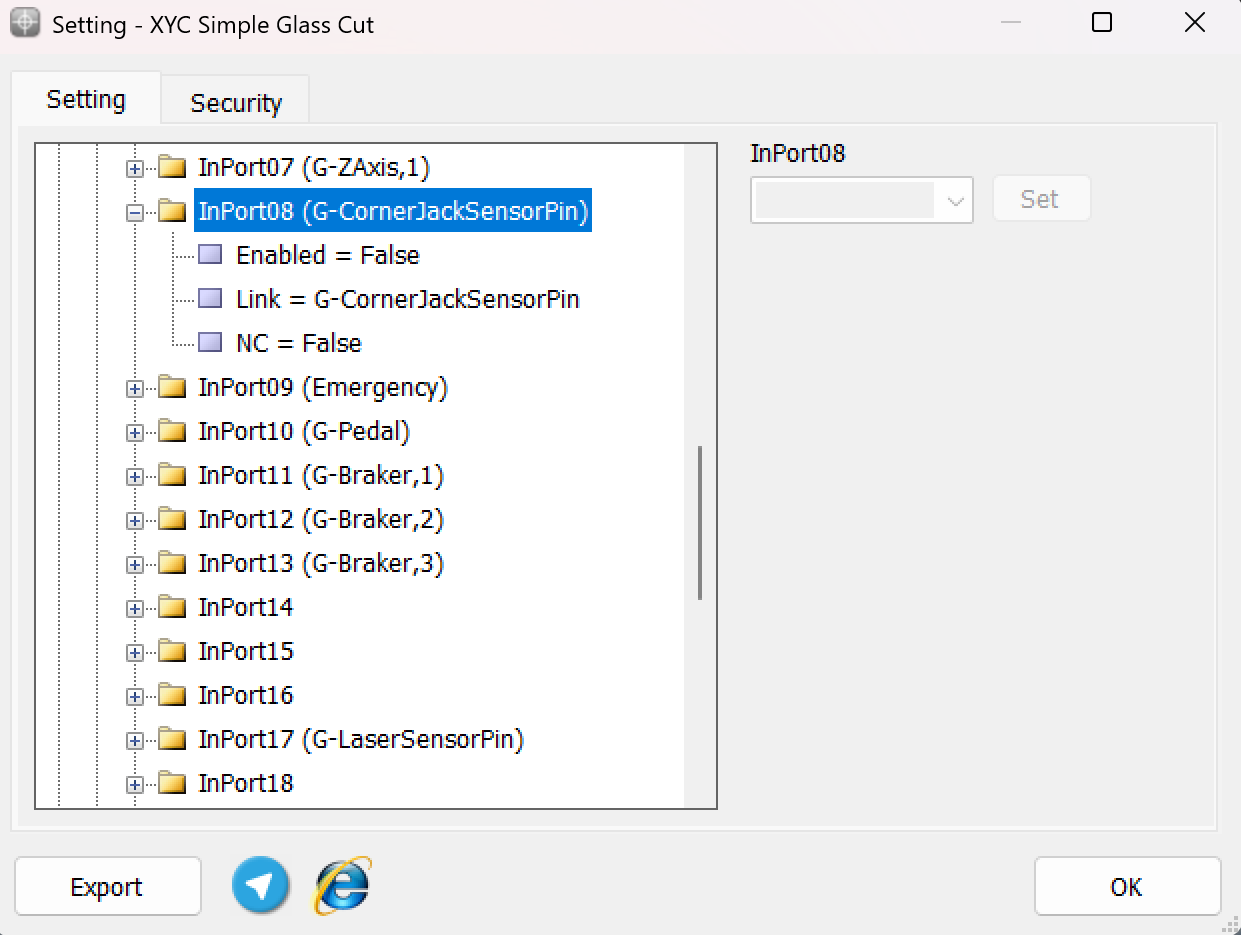
CNC Cam Makinelerinde Krikoları Kontrol Etmek İçin Çıkışlar
CNC cam makinelerinde krikoları kontrol etmek için kullanılan çıkışlar, işleme sırasında cam levhayı kaldırmak veya sabitlemek gibi işlemleri yönetmek açısından kritiktir. Bu çıkışlar, ilgili kriko motorlarına ya da aktüatörlere komut göndermek üzere yazılımda tanımlanır.
Tipik Çıkış Yapılandırması
-
Çıkış Tanımı:
- Her kriko için hareketini kontrol eden belirli bir çıkış bağlantısı atanır.
- Örneğin, çıkışlar şu şekilde etiketlenir:
- G-CornerJackUpPin: Krikonun yukarı hareketini kontrol eder.
- G-CornerJackDownPin: Krikonun aşağı hareketini kontrol eder.
-
Fonksiyonellik:
- Yukarı Hareket: İlgili çıkışı aktif ederek krikoyu yukarı kaldırır.
- Aşağı Hareket: İlgili çıkışı aktif ederek krikoyu aşağı indirir.
-
Bağlantı ve Kontrol:
- Bu çıkışlar, kontrol kartının çıkış terminallerine bağlanır ve buradan kriko motorlarına veya solenoidlerine kablolanır.
- Operatörler, makine arayüzü veya kontrol yazılımı üzerinden bu çıkışları etkinleştirmek için komut gönderebilirler.
Kullanım Senaryoları
- Cam Yükleme/Boşaltma: Krikolar cam levhayı yükleme veya boşaltma işlemleri sırasında kaldırır ya da indirir.
- Hizalama: Krikolar, camın yüksekliğini ayarlayarak doğru konumlandırılmasına yardımcı olur.
- Sabitlenme: Kesim ya da diğer işlemler sırasında camı güvenli şekilde yerinde tutarlar.
Yazılımda Yapılandırma:
- System > Outports bölümüne gidin.
- Her kriko için çıkış bağlantılarını atayın:
- G-JackUpPin
- G-JackDownPin
- Enable (Etkin) parametresini True olarak ayarlayarak çıkışı aktif hale getirin.
Bu çıkışların doğru şekilde yapılandırılması ve kullanılması, CNC cam makinelerinde krikolar üzerinde hassas kontrol sağlayarak işlem verimliliğini ve doğruluğunu artırır.
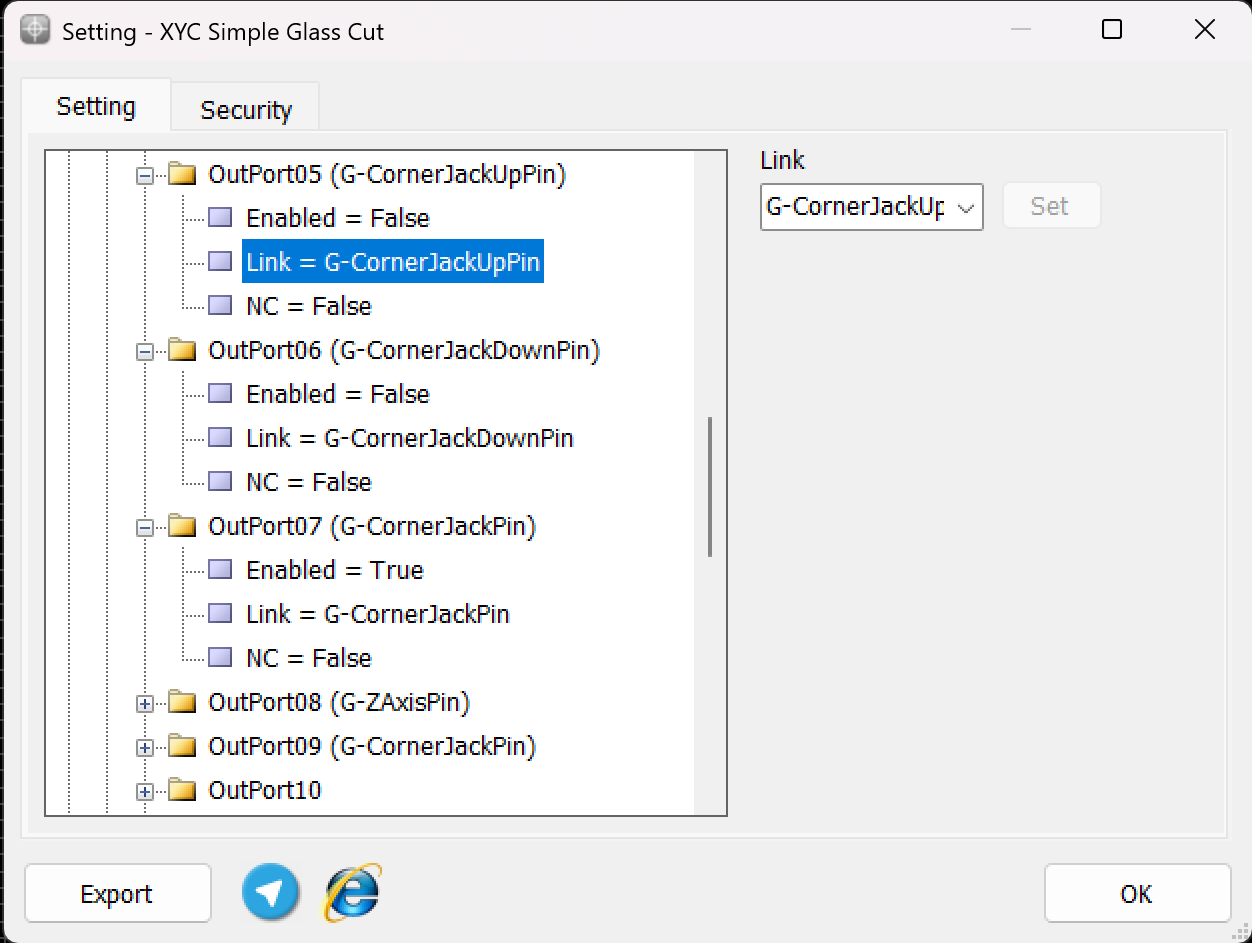
CNC Cam Makinelerinde Pedal Kontrollü Çoklu Görev Rutini
CNC cam makinelerinde, pedal kontrol sistemi, tek bir anahtarla birden fazla işlemi yönetmek ve düzenlemek amacıyla sıkça kullanılır. Bu sistem, operatörlerin belirli bir sırayla pedala basarak çeşitli işlemleri verimli şekilde gerçekleştirmesini sağlar. Her pedal basımı farklı bir işlemi tetikler, böylece koordineli ve akıcı operasyonlar sağlanır.
İşlem Rutini
-
İlk Pedal Basımı:
- Köşe jack aktif hale gelir ve yukarı hareket eder.
- Bu adım, cam levhayı hizalama veya sabitleme için uygun konuma getirir.
-
İkinci Pedal Basımı:
- Hava üfleyici sistemi açılır.
- Üfleyici, cam levhanın altına hava yastığı oluşturarak hizalama için camı yeniden konumlandırmayı kolaylaştırır.
-
Üçüncü Pedal Basımı:
- Üfleyici sistemi kapatılır.
- Bu, camın sabitlenmesini sağlar ve bir sonraki aşamaya hazır hale getirir.
Pedal Kontrollü Sistem Avantajları:
- Basitleştirilmiş Operasyon: Birden fazla anahtar ve manuel ayar ihtiyacını azaltır.
- Geliştirilmiş İş Akışı: Operatörlerin yerinden ayrılmadan işlemleri hızlı ve verimli yönetmesini sağlar.
- Esneklik: Pedalın çok işlevli rolü, çeşitli operasyonel ihtiyaçlara uyum sağlar.
Yapılandırma ve Özelleştirme
Pedal sistemi, kontrolör yazılımında özelleştirilebilir:
- Her pedal basımı, belirli çıkışlara atanır:
- İlk basım: G-JackUpPin (köşe kriko yukarı çıkışı) ile bağlantılıdır.
- İkinci basım: G-BlowerOnPin (üfleyici aktivasyon çıkışı) ile bağlantılıdır.
- Üçüncü basım: G-JackDownPin (köşe kriko aşağı çıkışı) ile bağlantılıdır.
- Zamanlama ve sıra, operatörün özel ihtiyaçlarına göre ayarlanabilir.
Updated 4 months ago